Building Enclosures: Understanding the commissioning process
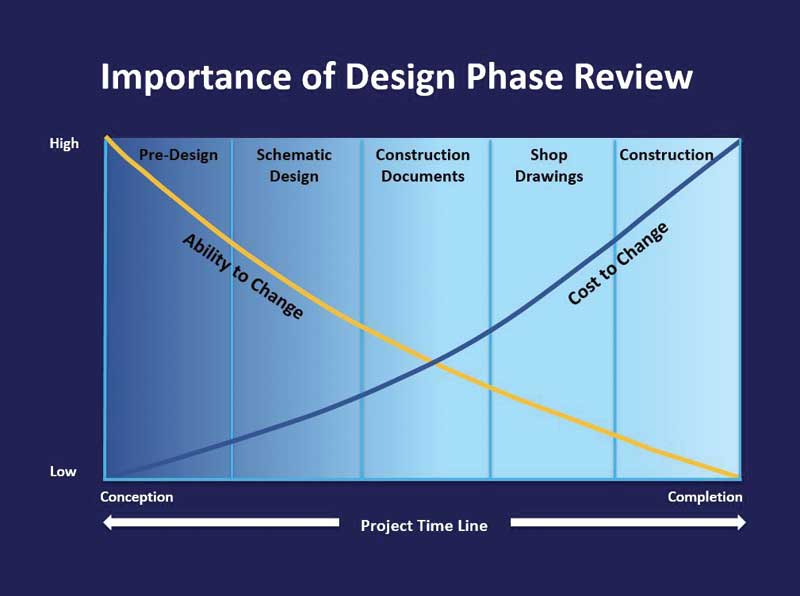
Implementing enclosure commissioning
The building enclosure commissioning process should begin when the owner is first considering building a new facility or renovating an existing one. The earlier the commissioning process begins, the easier it is to incorporate the commissioning comments into the construction documents. The commissioning process in Figure 1 is recommended for each building enclosure system—waterproofing, air barriers, roofing, opaque walls, and fenestration.
Pre-design phase
To initiate the commissioning process, the BECxP should conduct a workshop with the owner, user groups, and design team (if available) to identify the building enclosure performance requirements and level. The items discussed can include program requirements, climate, facility function, budget, delivery schedule, and durability.
If the owner is looking for a building that will last more than 50 years, the materials and detailing proposed during the design should have similar anticipated service lives that correlate to their use. The owner should also identify the commissioning budget and scope to define the project expectations and responsibilities. The BECxP then compiles a commissioning plan, which includes laying out the project requirements, responsibilities, and scope of the commissioning process.
Design phase
The most important aspect of the design phase is the technical peer reviews. While the function of the commissioning team is not to review all items related to the design and construction of the building, the focus is on specific key components within the building enclosure design, or issues occurring during construction known to allow moisture and/or air infiltration. It must be stressed that enclosure commissioning procedures should not slow the design process—all peer reviews should occur within the timeframe of the originally scheduled owner reviews.
The prime architectural design team has the final say, as they are ultimately responsible for signing and sealing the construction documents. However, the BECxP focuses on potential moisture and/or air infiltration issues including (but not limited to) roofs, walls, sealants, air barriers, flashings, windows, waterproofing, curtain walls, and other associated components. Additionally, it is important to focus on the role of the building enclosure as a complete air barrier since it is the connection of components that leads to most construction issues.
Typically, a building is designed for the HVAC system to provide positive pressure to prevent air infiltration into the building. For the HVAC system to work properly, the enclosure system has to function as intended. The BECxP evaluates how the wall systems and fenestration will function together to form a complete air barrier system.
The quantity and timing of the technical peer reviews varies depending on the projects’ complexity and the level of commissioning desired. At a very minimum, one review should be performed before mid-construction documents level.
A typical recommendation is for three reviews occurring at the 50 percent and 100 percent design development phase, and 50 percent construction document phase. The earlier reviews focus on type of assemblies, components, and their relationships and compatibility. The 50 percent construction document review is used to perform a constructability review including the component interface detailing. Depending on the nature/difficulty of the design, an enclosure contractor (part of the construction team) may assist in a review of detail constructability, pointing out areas where a detail would be difficult to construct or where a simplified detail might work more effectively. A fourth review or back check can occur at the 90 percent construction document level. The earlier reviews are important as at this point in the design—it is often too late to make substantial changes to the design phase if problems are identified.
After each review, the BECxP attends meetings with the owner and design team to review comments and develop modifications to the drawings and specifications where necessary. The comments issue log is updated to keep track of the comments to be incorporated in the next construction document set as well as to track responses.
To facilitate the construction phase of the commissioning process and preclude critical commissioning elements from being overlooked, the BECxP prepares enclosure commissioning specifications. The specifications are written by the enclosure commissioning team, but integrated into the overall construction documents by the designer. The enclosure commissioning specifications outline the:
- critical building enclosure systems requiring commissioning;
- mockup/model construction requirements for the enclosure systems;
- various building enclosure functional test requirements; and
- contractor participation requirements during the testing.
For the building enclosure, one of the goals of the commissioning specifications is to alert the various enclosure subcontractors that the enclosure is to be tested to withstand water intrusion and air infiltration, and they have responsibilities for assisting with the testing.
Pre-construction phase
While the pre-construction phase is not always clearly delineated in the various industry standards, guidelines of ASTM, ASHRAE, and NIBS all reference BECxP attendance at a pre-bid conference. The intent of this phase is to introduce the subcontractors to the commissioning process and to review their role and responsibility in the commissioning process. It also provides a good opportunity to vet the proposed material, components, and procurement methods regarding compliance with the owner’s project requirements.
For instance, a contractor may offer a time or cost savings by switching materials or possibly panelizing the project. This gives the BECxP an opportunity to note if the proposal provides equal or better performance than the owner is anticipating.