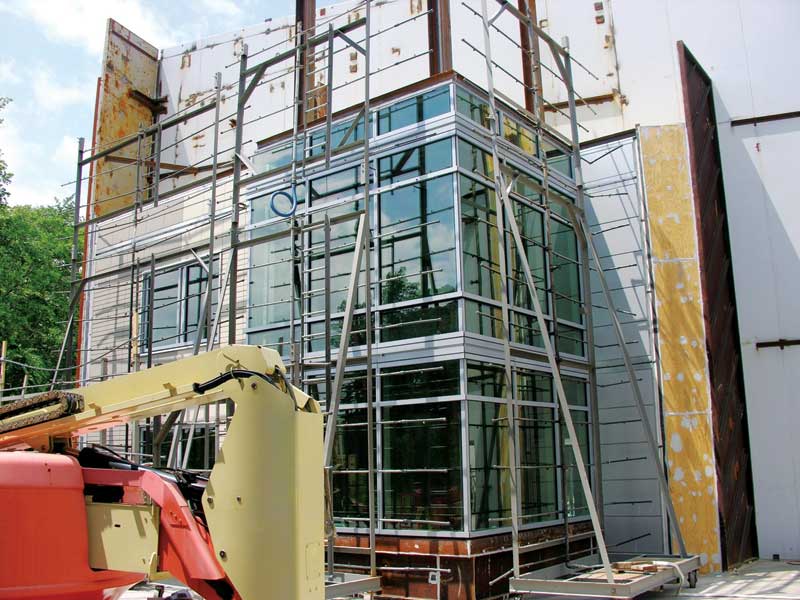
Construction phase
Because the building enclosure subcontractors are often unfamiliar with the commissioning process, one of the first steps for the BECxP is to conduct a commissioning workshop. The general contractor and the subcontractors for the various components of the building enclosure are required to attend. The enclosure commissioning plan is reviewed and includes the project goals, each parties’ responsibilities, and the various inspections and functional test procedures to be performed. Followup meetings are held with all the enclosure contractors to review the various shop drawings with close attention paid to tie-ins between differing components of an assembly (e.g. window frame to wall and air barriers).
The primary goal is to address a major issue in exterior enclosure construction, which is the diffused responsibility entailed in the construction of the building enclosure. This is an issue as no single entity is responsible for guaranteeing the enclosure is properly constructed. Identifying the “by others” is critical to understanding the constructability and sequencing of the enclosure.
The commissioning team reviews submittals and substitutions as related to moisture control and air barrier criteria throughout the construction process, and to finalize the functional test procedures for moisture intrusion testing.
Testing of mockup wall
Since the opaque roofing, waterproofing, wall, door, and window systems must be completely constructed before the enclosure can be tested for watertightness, a mockup is highly recommended. It should include opaque wall, door, window sections, and tie-ins to roofs and sub-grade waterproofing systems in order to set the standard of quality for the enclosure. The mockup allows the subcontractors to work out the project sequencing and provides an opportunity to fine tune details should construction issues arise. The BECxP reviews the installation of each component of the wall assembly for compliance with the construction documents, manufacturer’s installation instructions, and construction checklists.
Each component making up each mockup is photographed for future reference. The photographic documentation is critical to the mockup’s success for setting the standard of quality. Many components in an enclosure assembly are concealed by the next layer of the enclosure. For example, the embedded wall flashings are covered by the membrane waterproofing. Without photographs, there would be no way of referring back to the successful installation to determine if deviations occurred.
Specific building enclosure assemblies—such as curtain walls, punched windows, flashings, and tie-ins to roofs—are typical areas of concern as related to water intrusion or air infiltration. Therefore, rigorous functional procedures are performed based on the following standards (other tests may also be required, depending on the assembly):
- American Architectural Manufacturers Association (AAMA) 502/503, Voluntary Specification for Field Testing of Newly Installed Fenestration Products; and
- AAMA 501.2, Quality Assurance and Diagnostic Water Leakage Field Check of Installed Storefronts, Curtain Walls, and Sloped Glazing Systems.
The specific test method depends on the particular fenestration type.
Windows and doors specified in the contract documents are designed to meet criteria outlined in similar laboratory tests. For field testing, these tests involve placing the door or window assembly under an interior negative pressure differential, while simultaneously simulating a measurable wind-driven rain event over the outside face of the assembly. Due to various fenestration assembly sizes and configurations, the testing apparatus must be modified accordingly. The general contractor, with the BECxP’s guidance, builds a test assembly based on the requirements detailed in the test standards.
Monitoring construction
Based on the changes put in place to address deficiencies uncovered during mockup testing, modified details should be developed for incorporation into revised shop drawings. Each subcontractor is required to perform its work using the modified details and certify the work was performed as detailed. The BECxP and general contractor should follow up the mockup testing with periodic field inspections to determine whether or not the subcontractors are performing the work properly. The commissioning team should also conduct random water spray and/or pressure chamber testing periodically as a check to visual observations.
The BECxP performs periodic site visits to observe and document ongoing construction activities with deficiencies noted and tracked in an ongoing construction issue log. Periodic meetings are held to review ongoing issues and to identify any deviations from the OPR and contract documents.
Acceptance and post-construction phases
While no project should depend on final acceptance testing, there are commissioning tests performed at the end—not to identify pass/fail project compliance, but rather to document results of the commissioning process. One typical test is to confirm the air barrier functions of the enclosure are properly constructed. The BECxP conducts air infiltration testing using a blower door assembly following the protocols detailed in ASTM E779-87, Test Method for Determining Air Leakage by Fan Pressurization. While not currently commonly performed, this test is required for enhanced commissioning and as part of the 2015 International Energy Conservation Code (IECC). Other acceptance tests may include moisture testing of horizontal waterproofing, additional air and water testing of fenestrations, and infra-red (i.e. thermal imaging) of low-slope roof systems.
As the construction phase comes to an end, many owners are continuing the commissioning process, which becomes an ongoing routine in the life of the facility. The BECxP assists the owner in documenting the commissioning process in the final commissioning report. The final report documents the entire design and construction process and includes modifications and changes occurring during construction, as well as responses to the design and construction issue logs.
Since most facilities are complex and require annual maintenance, the BECxP oversees contractor training sessions held to train the facility and maintenance staff in the building features and upkeep. The close-out process may also include owner/user review meetings and warranty period walkthrough to resolve any outstanding performance issues and to have them rectified while the facility is still under warranty.