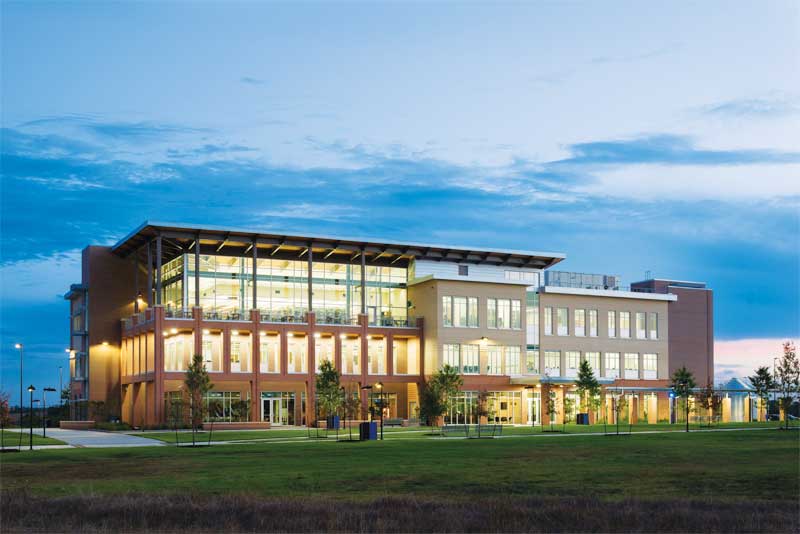
by James Arnold, PE, RRO, and Lynn Walters
According to the Air Barrier Association of America (ABAA), there are seven different categories of air barrier assemblies. (These categories are self-adhered sheet membranes, fluid-applied membranes, sprayed polyurethane foam [SPF], mechanically fastened commercial building wrap, board stock/rigid cellular thermal insulation board, factory-bonded membranes to sheathing, and adhesive-backed commercial building paper. For more, consult Diane Hun’s “New Air- and Water-resistive Technologies for Commercial Buildings.”) Each offers advantages depending on a number of factors, including geography, labor considerations, and even the height of the structure. This article examines the growing role of fluid-applied air barrier systems in meeting code and test specifications, and discusses related approaches and pitfalls. It also reviews common architectural details that present air barrier challenges, as well as fluid-applied assemblies that can address them.
While there is no one-size-fits-all solution, fluid-applied air barriers are growing in acceptance because of their ease of application and versatility across a range of code and performance requirements. Indeed, there are a plethora of commercial air barriers on the market, and it can be difficult to distinguish between products simply by identifying which comply with test code requirements. Specifications between products can vary widely, and ABAA establishes minimum standards per prescribed industry test methods (Figure 1).
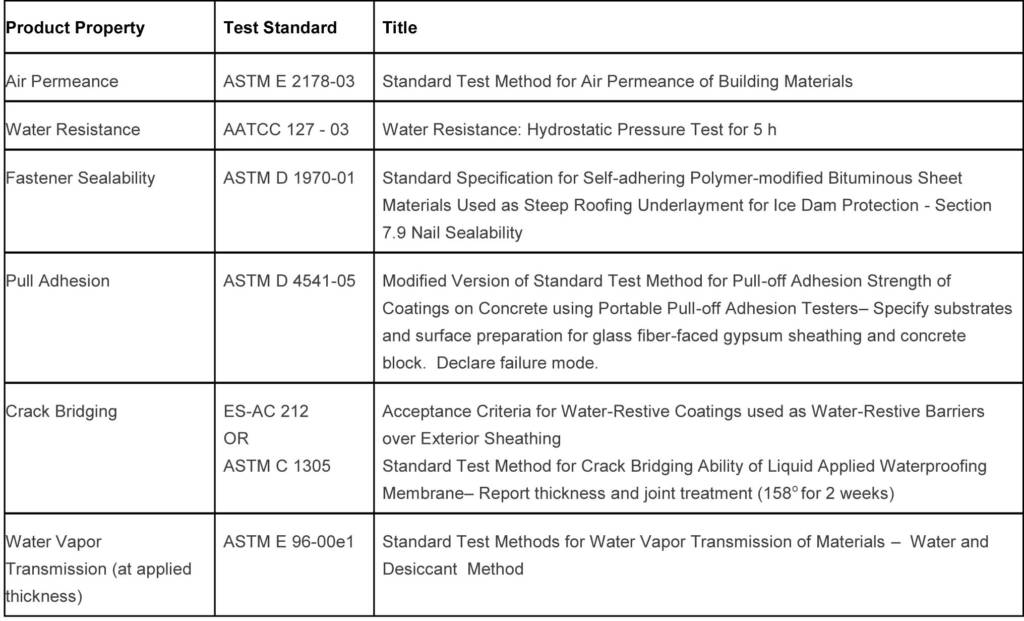
Image courtesy ABAA
To be sure, relevant requirements are a valuable baseline, so an overview frames this discussion. At least 47 states or jurisdictions within states and the District of Columbia adopted the 2012 International Energy Conservation Code (IECC) requirements. Requirements for air barriers tend to evolve slowly. While IECC updates every three years, state and local adoption takes time and is not mandatory. New 2018 IECC requirements were published for the industry’s consideration in August 2017.
The fundamental science of air barriers remains the same, though new studies can improve clarity as the building industry adapts. This means specifying air barriers requires an understanding of both product characteristics and science in order to ensure the selection meets the demands of the project and provides strong value in terms of cost and long-term performance.
In general, air barrier assemblies can help reduce building energy demands, minimize HVAC sizing requirements, and improve indoor air quality (IAQ) and occupant comfort. The U.S. Department of Energy (DOE) estimates average air leakage in commercial buildings is six percent, representing substantial energy loss (Figure 2). (Further information on this review can be found in the article, “After London Fire, 600 Tower Blocks Must Be Tested for Flammable Cladding,” published in June at www.reuters.com/article/us-britain-fire-cladding-idUSKBN19D0W5.) Leakage rates would likely be even higher in the industrial and transportation sectors due to structures with uninsulated roofs, vehicle entryways, loading docks, multiple vents, and similar problems. Liquid-applied air barriers—including water-based acrylic air barriers low in volatile organic compounds (VOCs)—can usually reduce installation costs and maximize installed value while meeting or exceeding key requirements.
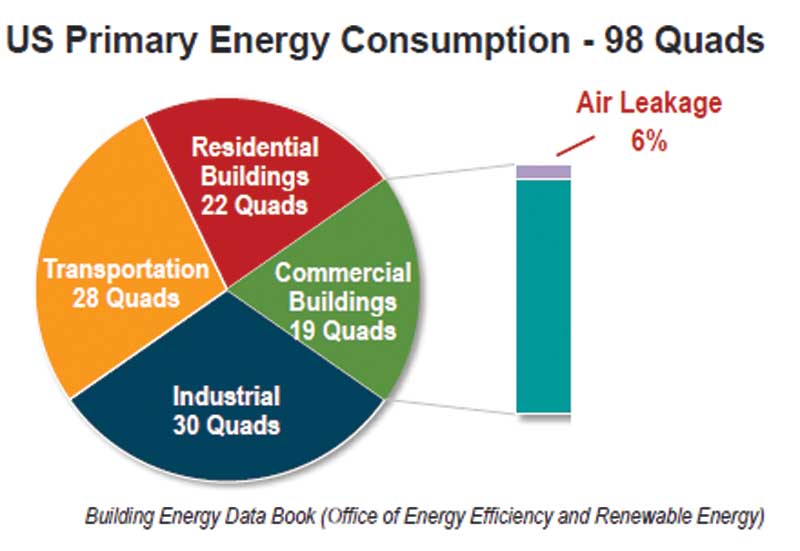
Images courtesy Kemper System America
Safety first
There are at least three primary criteria for selecting a liquid-applied—or any—air-barrier material or system: air leakage, weather resistance, and vapor permeance. These are in addition to safety standards, which may be even more important in terms of risk management. While a zero-risk world does not exist, decisions about building materials can have long-term consequences. The deadly blaze at a residential high-rise in London this June sparked a review of cladding materials on 600 tower blocks. (Learn more with “Spray Polyurethane Foam Under Fire in CA,” published in Durability+Design in June.) In an uncertain world, building codes provide a level of due diligence.
Many construction materials, from wood to polystyrene, are flammable or can ignite; even steel melts at extreme temperatures. Over the past five to seven years, the industry has shifted away from some traditional barrier options such as asphalt-based materials for above-grade exterior walls, and toward water-based barrier coatings. More residential and commercial codes and architects are also specifying fire test standards such as ASTM E84, Standard Test Method for Surface Burning Characteristics of Building Materials, and National Fire Protection Association (NFPA) 285, Standard Fire Test Method for Evaluation of Fire Propagation Characteristics of Exterior Non-loadbearing Wall Assemblies Containing Combustible Components (which measures the spread of fire and smoke in length and width on a test assembly).
Some fluid-applied air barriers dry to a film as thin as 0.6 to 0.75 mm (20 to 25 mils)—the less mass a barrier has, the less there is to support combustion. Other barrier materials that are part of the assembly, including insulation, may produce smoke or toxic fumes. Earlier this year, the California Department of Toxic Substances Control (DTSC) proposed listing sprayed polyurethane foam (SPF) as a ‘priority product’ due to concerns about exposure to unreacted methylene diphenyl diisocyanate (MDI) during application. (This information is derived from an American Institute of Architects [AIA] presentation, “Proper Use and Application of Air Barrier Systems,” by Jim Arnold, one of this article’s authors.) When foam plastic insulation is used in exterior walls (for Types I, II, III, or IV), the International Building Code (IBC) requires exterior wall materials—including the air barrier assembly—meet NFPA 285.