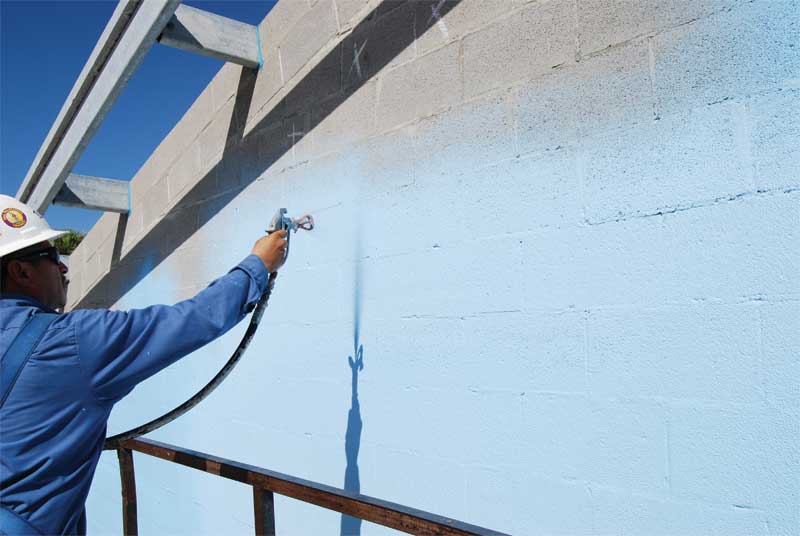
Ratings and reality
Ratings for both the primary air barrier materials and the air barrier assemblies are important for product comparisons. Ratings for the latter, however, offer a perspective one step closer to actual field conditions, since components are tested together as a system.
It should be understood air barrier material and assembly specifications for any given product or system are generated under laboratory conditions, usually by independent test labs. Test assemblies are constructed to be as airtight/watertight as possible before final test results are reported. There can obviously be a significant difference between performance derived under laboratory conditions and the field. For this reason, ABAA recommends verified air barrier products
and assemblies be installed by ABAA-certified installers. Such individuals have gone through a three-day class in each category of air barrier to learn best practices. Some manufacturers also offer training programs, often through distributors, and provide onsite training and technical support for major projects.
Proper installation is essential to achieve desired air barrier properties. Quality assurance inspections done while installation is in progress have generally proven to be the most effective way to manage the final installed performance. Of course, finished structures can also be air-barrier tested, which may be required or desired in some circumstances, particularly for commercial construction. However, field testing adds a cost and may not always be practical. If there is an issue with an air barrier once the exterior wall has been cladded, additional certified tests may be needed, and expenses can mount. Rework can be very expensive.
Specifying ABAA-verified ASTM E2357 assemblies is generally the shortest route to air barrier compliance, though it is always important to check state and local code requirements. ABAA verification indicates the assembly meets not only the basic requirements, but also the additional test requirements in Figure 1. However, specifiers should always be mindful actual field performance is the ultimate goal of construction projects, and the industry as whole.
DOE, which also supports IECC and American Society of Heating, Refrigerating, and Air-conditioning Engineers (ASHRAE) standards fostering energy conservation, is also interested in the distinction between test and field performance and ways to close the gap. A study conducted by Oak Ridge National Laboratory (ORNL) for DOE last year examined air leakage rates in typical air barrier assemblies for residential buildings. The study reviewed how airtightness of residential walls heavily depends on the skills of installers. Although liquid air barriers were not the focus of the study, the results are informative for both residential and commercial construction.
Specifically, the study examined both insulating and non-insulating sheathing, as well as mechanically fastened membranes or housewraps, widely used as water barriers (though not necessarily air barriers) on new homes in the United States. Nine test walls (three of each type) were erected by three different installers. Air leakage was then measured based on procedures set by ASTM E283, Standard Test Method for Determining Rate of Air Leakage Through Exterior Windows, Curtain Walls, and Doors Under Specified Pressure Differences Across the Specimen, with leakage rates normalized to standard temperature and pressure. The results indicated wide variability due to workmanship, with flow rates varying up to 200 percent from their average values. Most of the average leakage rates exceeded the IECC maximum leakage rate. The researchers noted variability will likely be higher under actual field conditions.
The study also quantifies the potential impact of imperfections in air barrier assemblies at foundation wall joints, at wall-roof joints, and around electrical outlets. Such airflows are not always easily tackled by air barriers, and not always addressed in installation manuals. The study calculated if left unsealed, these three areas alone could contribute 27 percent to total air infiltration (per IECC leakage requirements for homes in Climate Zones 3 and above).