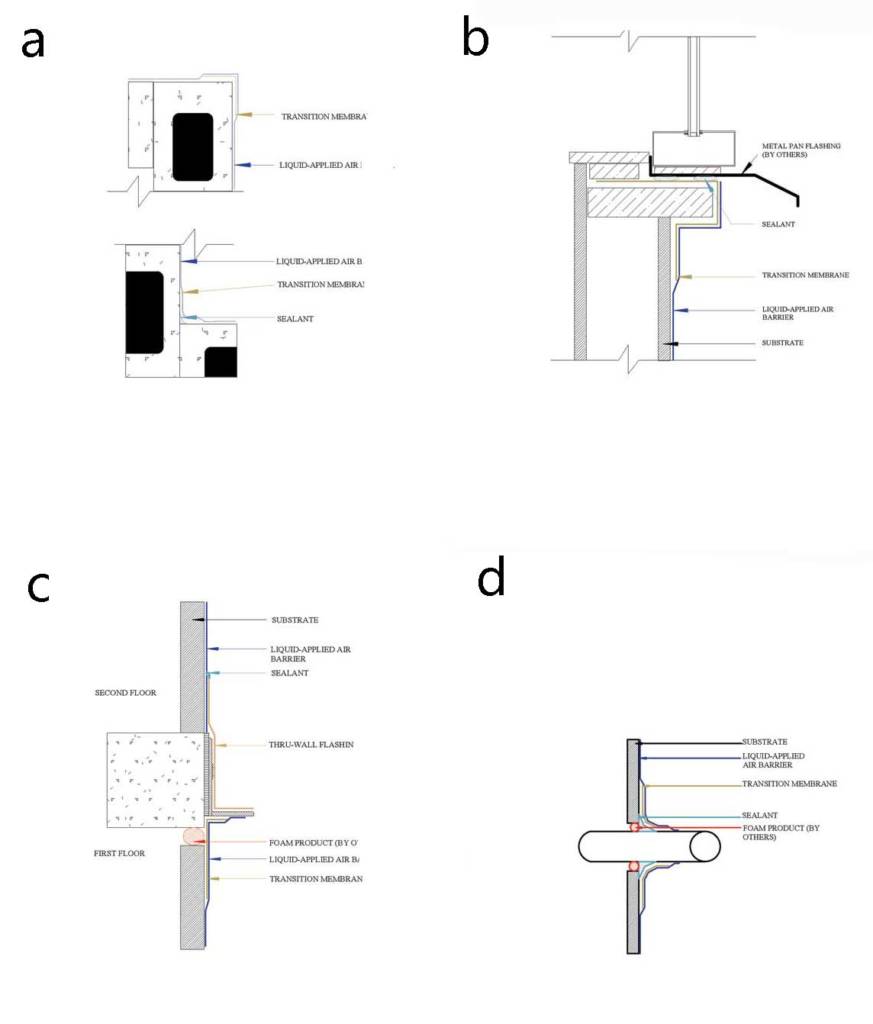
Liquid-applied air barriers
When one considers exterior walls are not always vertical and never completely flat, the general advantages of liquid-applied air barriers become clear. Building façades may be angled or curved. Wall expanses may be interrupted by windows and doors, balconies and overhangs, columns, or outcroppings. There may be multiple penetrations for electrical or plumbing connections. Inside and outside corners of walls and edges are also obvious areas of air infiltration.
The success of any air barrier depends on the ability to handle application details. Liquid-applied air/weather barriers provide seamless protection across exterior wall surfaces and offer versatility for sealing difficult areas. Figure 5 shows recommended details for a variety of applications with liquid air barriers, sealant, and transition tape. All air barrier manufacturers define how to address these details using air barrier components customized to the type of product being applied.
Component materials used in any air barrier system must be compatible with one another and substrates that include flashing materials. When necessary, primers may be employed to key adhesion, such as over weather-coated OSB and exterior drywall.
Once detailing with sealants and tape is complete, liquid air barriers can be applied to field areas with heavy-duty sprayers, rollers, and brushes for spot coverage. Sprayers are generally the fastest method for expansive exterior wall surfaces, including concrete masonry units (CMUs). Rollers are almost as fast and can be faster on foundation walls and low-rise buildings where no scaffolding is required. This method is preferred under windy conditions and at elevations where overspray may be an issue. High-nap rollers are useful for coating porous or uneven surfaces such as brick or block. Proper coverage for a liquid barrier coating is readily identified by continuous coverage and opacity. Coverage in field areas can be checked as the coating is applied using a simple wet mil gauge. If needed, additional coating can be applied while the film is still wet.
Most liquid-applied products can be exposed to the elements for at least 90 to 180 days, which can be essential for construction scheduling. Like other exterior coatings, they should not be applied with rain in the immediate forecast, or under very cold conditions. Liquid-applied barrier coatings can dry quickly, though curing takes longer, and time varies by product and ambient conditions. In warm climate zones, most products can be applied year-round. In more temperate zones, some products are best applied during the normal May to October construction season. Silicone-based products can generally be installed at lower temperatures and to damper surfaces, and can withstand moisture sooner than acrylics. However, some silicones may be vapor-impermeable.
Before specifying any air barrier, specifiers should consider the ability to achieve performance requirements at low installed cost. For many construction projects, liquid air barriers can substantially reduce installation costs compared to other systems—especially self-adhered sheet membranes. These usually take a larger crew and require a primer to be applied to the entire surface first. More labor steps mean a higher cost. Field performance is crucial, so ease of application
and the ability to quality check in the field are important advantages. All materials have their intricacies—for instance, sheet goods can create minute ‘fish mouths’ and air pockets that may go unnoticed. In contrast, liquid-applied air barriers leave a monolithic surface so the installer can easily scan and correct imperfections.
While liquid air barriers are not all the same, as a class they are extremely versatile and can often be applied in a single coat. Meeting or exceeding industry specifications should be a priority, but beyond this, single-pass coverage is perhaps the most important selection criteria for achieving the best value.
James Arnold, PE, RRO, is director of product development for Kemper System America, Inc. He brings more than 30 years of experience from the design, construction management, and roofing industries to his role. Arnold can be reached via e-mail at jarnold@kempersystem.com.
Lynn Walters is West Coast regional sales manager for Kemper System. He is a committee member with the Air Barrier Association of America (ABAA), serves on the board of directors of the Reflective Insulation Manufacturers Association (RIMA), and is a member of ASTM International, the Cool Roof Rating Council, and RCI. Walters has 30 years of experience with energy-efficient building envelope systems. He can be reached via e-mail by contacting lwalters@kempersystem.com.