Building for infrastructure durability
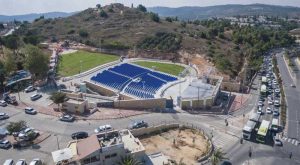
Photo courtesy Glimmer Industrial Consultation and Elisar Civil Engineering
In such environments, there are inherent advantages to the performance-related approach in terms of construction time, direct cost, and longevity. The construction time advantage is demonstrated in the form of built-in remedies to application errors such as segregations, surface cracking, and insufficient rebar coverage, which the contactor does not need to spend time correcting. The cost advantage is demonstrated by both a material cost reduction (less-costly concrete mix, smaller amounts/sizes of rebar) and avoidance of correction expenses. The longevity advantages are reflected in the service life predictions software explained in detail later in the article.
Park of Peace Amphitheater was built in Mevasseret-Zion, not far from Highway 1 running from Tel-Aviv to Jerusalem. With a proximity of only 200 m (565 ft) from this main thoroughfare, there was a greater likelihood of early carbonation, which could reduce the naturally high alkaline environment of new concrete that initially protects rebar from corrosion. The site was considered to have a moderately aggressive chemical environment from direct exposure to the ground. These factors had classified the concrete according to EN 206-1: Exposure Level XC-4 and XA-2, high exposure levels for concrete exposed to the air and ground, respectively. The project included a large concrete pour to make the steps and graduated seating platforms.
The Kidron Valley Culvert was designed to safely funnel seasonal flood waters underneath Highway 90 near the Dead Sea. The sulfate-rich ground classified the project’s exposure level at XA-3 (harsh soil aggressiveness), according to Table One of EN 206-1 (equivalent to IS 118 Exposure Level 11). The environment was also extremely hot, and the casting of very thick elements posed a higher risk for thermal cracking.
The Kinnet Tunnel project was also classified as having an XA-3 (harsh soil aggressiveness) exposure level, according to EN 206-1 and IS 118. The tunnel was needed to capture floodwater from the Arava and Eilat region and was, therefore, slated for construction in an environment of sulfate-rich ground and high temperatures. Additionally, the region’s soft water is very aggressive toward concrete and is also drift-rich (i.e. it will collect debris in the uncovered channel), promising a tunnel environment that will be corrosive both internally and externally.
Strategies for a 100-year service life
Use and/or specification of a migrating corrosion inhibitor or its equivalent were an integral part of building durability into each project and creating a cost-effective alternative to the deficiencies of the limiting-values/prescriptive-specifications approach. Whereas the limiting-values concrete design strategy sought to increase durability and minimize corrosion by delaying the exposure of rebar to corrosive elements, migrating corrosion inhibitors play an important role in both delaying time to corrosion initiation and reducing corrosion rates. This technology will be further enhanced by the use of materials and processes to reduce cracking and resist sulfate attack in the first place.
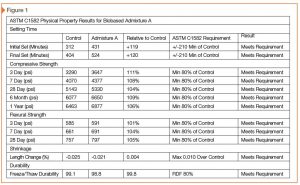
Image courtesy Cortec Corp.
The second-generation migrating corrosion inhibitor admixture specified in these projects is based on salts of amine-carboxylates. This chemistry works its way to the surface of the rebar, where it has an affinity to the metal and forms a protective molecular layer. When the naturally protective alkaline environment of concrete diminishes or when waters, salts, or other corrosives ingress through concrete pores or cracks, this migrating corrosion inhibitor layer disrupts the normal electrochemical process that would otherwise allow a corrosive reaction in the presence of an electrolyte.
Second-generation migrating corrosion inhibitors are said to potentially delay corrosion initiation by two to three times and to reduce corrosion rates after initiation by five to 15 times (read Improving Durability of Infrastructure with Migratory Corrosion Inhibitors [MCI] Handbook by Boris Miksic). The migrating corrosion inhibitor specified in these projects meets ASTM C1582, Standard Specification for Admixtures to Inhibit Chloride-Induced Corrosion of Reinforcing Steel in Concrete, physical property results for set time, compressive strength, flexural strength, shrinkage, and freeze/thaw durability (Figure 1) (consult “Admixture to Inhibit Chloride-induced Corrosion of Reinforcing Steel in Concrete [ASTM C1582] Concrete Properties Testing Final Report,” by Glenn Schaefer). It also meets corrosion properties under ASTM G180, Standard Test Method for Corrosion Inhibiting Admixtures for Steel in Concrete by Polarization Resistance in Cementitious Slurries, (reduced corrosion current by factor of 10, bringing it within the requirements to be 1/8 the value for control specimens) (Figure 2) (read “Re: Evaluation of Corrosion Inhibiting Admixture According to ASTM G180, TCG Project 17057” by Neal S. Burke, PhD). It tends to be easy for ready-mixers to work with.
Service life prediction software can help engineers estimate the service life and cost of a structure based on parameters such as climate, mix design, type of reinforcing steel, and corrosion-inhibiting admixtures. Migrating corrosion inhibitors enhance service life by increasing the chloride threshold of the reinforcement, and by slowing down corrosion once it initiates. The migrating inhibitor used increased the chloride threshold in the service life prediction software from 0.05 percent to 0.18 and also increased the propagation period by five times compared to the base case, as a conservative estimate of corrosion rate reduction found in ASTM-G109, Standard Test Method for Determining Effects of Chemical Admixtures on Corrosion of Embedded Steel Reinforcement in Concrete Exposed to Chloride Environments, testing of the product.