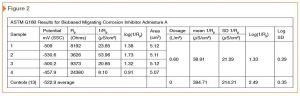
Image courtesy Cortec Corp.
When running a variety of mix designs for the Israeli infrastructure projects through the software, a concrete mix factoring in the expected performance characteristics of the migrating corrosion inhibitor projected longer service life compared to a denser concrete mix, yet without additional costs. The alternative concrete mix would have required C50/60 strength under the limiting values specification, calling for extra cement and leading to poor workability with a high risk of hydration heating, thermal cracking, and plastic cracking—factors counterproductive to durability. Curing also would have been more complicated with limiting values specifications, and extra rebar would have been needed for crack width control under Eurocode 2, Design of concrete structures – part 1-1: general rules and rules for buildings, and IS 466-1, Concrete code: General principals.
Instead, the performance-based design allowed the use of C35/45 concrete, requiring less cement and less rebar than for C50/60 concrete. Sulfate-resistant cement was also specified for additional durability of the two projects in a sulfate-rich environment. Incidentally, this cement has a slower strength development, enabling engineers to reduce hydration heat even further. Finally, even in the event of seemingly inevitable construction errors—such as surface cracking, non-constructive segregation, and insufficient concrete cover—the use of a migrating corrosion inhibitor offered an automatic remedy to mitigate the risk of corrosion to save the constructor considerable repair costs in future.
Applying these lessons in the United States
These projects provide insight into building for durability in the United States. Similar conditions are likely to exist in a southern coastal environment in the country due to high temperatures and the greater likelihood of high sulfate soils. There is also a greater potential for exposure to sea spray with high chloride content. Engineers must take factors like these into account when building in such environments. For example, a structural engineering firm designing a new hotel along the Alabama Gulf Coast considered various durability options before choosing a migrating corrosion inhibitor that allowed them to extend projected service life (compared to epoxy coated rebar) while staying within budget. Judging from the Israeli project examples, future structures facing high sulfate conditions on top of normal marine environments may achieve enhanced durability from the combined use of migrating corrosion inhibitors, sulfate-resistant cement, and C35/45 concrete to reduce cracking without requiring extra rebar.
Even by itself, a migrating corrosion inhibiting admixture can offer increased durability for situations that may be corrosive, although not exposed to marine, high sulfate, or high temperature environments. For instance, northern United States regions that experience harsh winters with lots of snow and ice compensate for the dangerous driving conditions by the heavy application of deicing salts. Roads, bridges, driveways, and parking ramps constructed in these environments are subject to freezing, thawing, cracking, and the ingress of chlorides leading to severe corrosion. Admixing a migrating corrosion inhibitor into the concrete can extend service life with minimal change to the ready-mix other than a slight delay in set time, which is sometimes an advantage for construction workers, but avoidable if necessary.
Another application where migrating corrosion inhibitors contribute to durability is in the risk of stray currents regions (underground re-enforced concrete within 3 km [2 mi] of an electric train, pipes with cathodic protection systems, or high-voltage electric lines). As migrating corrosion inhibitors form a protective molecular insulation layer on rebar, reinforced concrete comprising migrating corrosion inhibitors reduces the rate of corrosion by a factor of three to five (consult “Corrosion Protection of Reinforcement from Stray Current by MCI 2005/2006 NS Admixtures,” by Cortec Corporation. Research is also currently underway at the Israeli National Building Research Institute).
Conclusion
Building for durability of concrete infrastructure in extremely severe environments is an ongoing challenge. Use of a performance-related design method as was done in three Israeli infrastructure projects offers a good strategy for extending service life by taking a long-term approach to mitigating corrosion. Rather than simply delay corrosion by choosing a strategy that might require additional cement and rebar—with minimal protection once cracking and corrosion have started—the performance-based approach described here minimizes cracking, reduces material needs, and provides ongoing protection against corrosion even after cracking has started. A similar approach can be adapted to concrete infrastructure across the United States for greater durability in marine, sulfate-rich, and harsh winter environments (special thanks to Sen Kang, PhD, senior corrosion engineer, at Cortec Corporation, for technical review and editing).
Hadar Halperin is a business development manager of Glimmer Industrial Consultation, Israel, where she helps owners, engineers, and contractors meet service life and durability challenges in construction and infrastructure, through proven technologically advanced products. She has an MBA from the Tel Aviv University Coller School of Management. Halperin has extensive experience in corrosion control and service-life solutions, focusing on cost-effective engineering and realistic application conditions with a long-term perspective. She can be reached via e-mail at hadar@glimmer.co.il.
Julie Holmquist has been a content writer at Cortec Corporation for over four years. She specializes in writing about corrosion-inhibiting technology for concrete, electronics, manufacturing, oil and gas, and many other industries. Her articles have been published in dozens of industry magazines. She can be reached via e-mail at jholmquist@cortecvci.com.
Haggai Shoshany, Eng., has been a structural durability consultant for over 15 years. He specializes in concrete and corrosion technologies and industrial processes. His articles have been featured in many professional engineering magazines in Israel. His presentations have been published in several proceedings of engineering conventions held by NACE-Israel, AEAI, IACIE, and more. He can be reached via e-mail at haggai@gic-eng.com.
Jessi Meyer, FICRI, is vice-president sales – Asia/MCI at Cortec Corporation.She has an MBA from Concordia University, St. Paul, Minnesota and a BS in chemistry and business from the University of Wisconsin-Eau Claire, Eau Claire, Wisconsin. Meyer has extensive experience in the concrete, construction, and corrosion industries and holds six patents in these fields. She is an active member in the American Concrete Institute (ACI), NACE International, and the International Concrete Repair Institute (ICRI). She can be reached via e-mail at jmeyer@cortecvci.com.