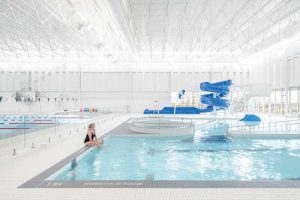
The ISO insulation has an ozone-depletion potential (ODP) of zero, so it is not harmful for the atmosphere, and a negligible global-warming potential (GWP). The panels are made of 30 percent recycled steel on average, and are reusable or recyclable at the end of their service life. IMPs are also easy to disassemble and move, so they can be repurposed, both for interior and exterior use. The plastic film applied to the panel edges helps keep the integrity of the foam system while reducing its off-gassing effect, ensuring a better stability of the thermal resistance over time. None of the materials used contain chlorofluorocarbons (CFCs) or hydrochlorofluorocarbons (HCFCs) and are thoroughly tested to ensure code compliance.
IMPs contribute to earning the Leadership in Energy and Environmental Design (LEED) certification for projects due to its contribution to buildings’ high energy efficiency throughout their lifecycle. They also receive Environmental Product Declaration (EPD) certification in accordance with International Organization for Standardization (ISO) 14025, Environmental Labels and Declarations: Type III Environmental Declarations–Principles and Procedures. A verified EPD form can contribute to earning construction projects credits for LEED v4 and other green building rating systems.
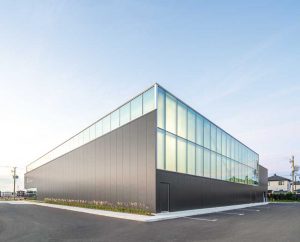
Design versatility
IMPs are celebrated for their aesthetically pleasing clean lines and their design flexibility. Their seamless, uniform look gives the illusion of sleek aluminum without its high price tag. Each project can be customized to suit one’s unique vision and creative flourish, without compromising functionality, durability, or building code compliance. The panels can either be installed vertically or horizontally, depending on creative direction. They can be adapted to existing structures and turnkey buildings without limitations on building height as the panels are fixed to the metal structure.
Further, the formability of the panels allows them to follow the shape of any building while still preserving the coherence of the design. They can also be cut onsite to different angular shapes to accommodate windows and doors, and to match the envisioned building design. Corners can be bent in the factory, giving the facade a continuous look.
IMPs offer multiple design options; they are available in a wide range of color combinations, finishes, and textures that allow designers to create a meaningful concept that reflects the building’s unique aesthetic or mission. For example, panels can be striated, micro-ribbed, fluted, smooth, or embossed. Integrated elements allow for enhanced creative expression. Popular decorative additions include colored fins that can be added to the panel joints, architectural aluminum composite material (ACM), overlay designs, ceramics, and masonry. All these applications are installed using brackets without damaging the panels. The panels can easily be coordinated with other products.
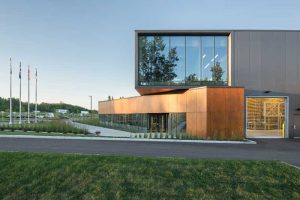
Two types of architectural panels for a range of applications
IMPs are typically either ISO insulation core panels or stone wool insulation core panels. ISO (polyurethane) core panels are made of polyisocyanurate foam which forms a chemical reaction when two liquid components are combined and expand to form the rigid insulating core. Its main structural benefits are a higher thermal value per inch and superior panel stiffness compared to conventional envelope systems. In addition to offering thermal value, this panel provides fire and rain barriers, as well as wind and tear resistance due to its exclusive anchoring system. The joint integrates a pressure equalized chamber that prevents water from being drawn in, reducing the risk of moisture infiltration. ISO core panels can be used as building envelopes, interior partitions, and suspended ceilings. They are suitable for industrial or commercial buildings, as well as for controlled atmosphere environments—such as food processing plants, cold storage, pharmaceutical clean rooms, and laboratories.