Choice of methods
Dewatering
Temporarily lowering groundwater levels to allow for construction and excavation activities is a common procedure for sites with high ground water levels. There are various techniques, from open sump pump immersion to ejection systems. A Wellpoint system was selected for this project as a cost-effective, manageable way to lower water levels for the site utility installations. It used an above-grade pump to generate a vacuum suction to pull water up into a header pipe and carry it to permitted, approved locations. Groundwater can be lowered approximately 6 m (20 ft) with this technique.
Vibro-floatation
Subsurface soils exploration revealed an underground makeup of soft sand, soft limestone, and local ‘muck’—not uncommon for coastal areas saturated with salt and brackish water. A geotechnical engineer was consulted for recommendations for a pile foundation selection. Various pile options include, but are not limited to, bored/cast-in-situ, driven pre-cast, and micropiles (with steel casings). A vibro-floatation foundation system was chosen due to its advantages of simplicity and speed, and cost-affordability. It did not require excavations of materials or management of water table issues and could be performed without harming existing building structures. This method improves the soil strata by injecting air and/or water through probe jets to liquefy the soil, and then uses probe vibrations to densify the soil, creating a void that is filled with crushed stone which is compacted as the probe is slowly removed. The design was delegated to a qualified sub-contractor, and the installation consisted of 367 stone piles, 0.9 m (3 ft) in diameter were injected, ranging in depth from 3 to 7 m (10 to 24 ft), and compacted to resist 287 kPa (6000 psf) loads, and were placed to support the spread concrete grade beam footings. This system improved the soil using its own characteristics, was environmentally friendly, and will reduce the possibility of differential settlements of the building’s structure.
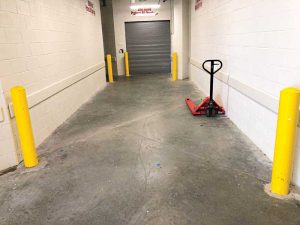
Concrete and masonry
A reinforced, poured-in-place concrete and masonry structure was selected due to its resistance to high winds and flood water loads, local labor supply availability, and performance as an excellent substrate backing for exterior stucco finishes. Mix designs were developed to achieve desired 27,579 kPa (4000 psi) or higher concrete strengths, placement of reinforcement was meticulous and heavily inspected, and methods and schedule of concrete placement was carefully coordinated to include night-time pours. A total of 1152 tons (1045 tonnes) of rebar and 7535 m3 (266,085 cf) of concrete went into the structure.
Waterproofing, joint sealants
Various products with proven success in the Southwest Florida environment were considered. For below grade concrete, options include both liquid and membrane waterproofing systems. Liquid membranes are applied similarly to paint and are most effective for smooth surfaces and for smaller and more intricate work. Multiple coats can be applied, but care must be taken to provide an even application. Membranes are applied as elastomeric or plastic sheets that are bonded to the substrate with cement mortar or adhesive and are lapped at seams. Sheet membranes are commonly used in larger areas, and where backfilled against, are covered by a protection board product. As an alternate (or additional) method of waterproofing concrete, a crystalline admixture can be added to the concrete. This admixture product creates a crystalline structure inside the concrete, and where there is a presence of water, reacts with the byproducts of cement hydration, and becomes resistant to extreme hydrostatic pressures. In addition, at the intersection of horizontal and vertical surfaces in concrete work, a water-stop product made from rubber, vinyl, or bentonite should be used to seal the joints against water penetration. The final design choices included self-adhered, rubberized asphalt/polyethylene sheet membranes (for walls) as the primary waterproofing, crystalline waterproofing admixtures added to the concrete mix (for underground cast-in-place concrete footings, walls, and pits) as primary and secondary waterproofing, and bentonite water-stops at joint intersections. The combination of these products provided some duplicity and overlap coverage while eliminating the need for intricate work.
Exterior wall openings in CMU and concrete structures are particularly susceptible to water permeability and migration issues. Products that coat the perimeter surfaces of these openings which are specifically made to prevent this vapor drive and absorption include typical concrete/masonry water-proofers and specifically formulated liquid flashings that can be applied by either spray, brush, or trowel methods. The advantage of the product use is that it creates a weather resistant, fully adhered air barrier membrane around these openings. The design choice included a troweled on, fluid-applied liquid flashing product that proved to be compatible with the joint sealants tested in the mockup.
Joint sealant choices should be based on a number of factors, among which are environment, performance, material compatibility, joint width. The design choices of urethane acrylic and polymer elastomeric sealants were ultimately based upon proven products for the Southwest Florida environment, sealants that exhibit superior adhesion and bond strength, durability, and elongation, and compatibility performance with other materials in the mockup testing.
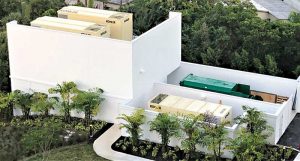
Roofing
Appropriate choices for roofing must include qualities of longevity, weather resistance and energy efficiency. The building design of the roof contemplated a flat structure that houses many mechanical pieces of equipment. The choices considered by the design team included BUR (built up roofing), modified bitumen (MB), and single-ply membranes. BUR systems consist of alternating layers of hot bitumen (asphalt) with layers of roofing felt that can then accept a reflective coating to combat the harsh heat and ultraviolet (UV) radiation effects of the sun. BUR’s have a typical life span of 12 to 20 years but can last up to 40 years with proper maintenance. MB systems are like BUR’s but are lighter weight (per square foot) and utilize layers of asphalt that are modified with other materials like polymers and fiberglass for increased durability. MB systems can be put down hot or ‘cold’ (as a self-adhering compound.) These can be single or multiple layers with average life spans ranging from 10 to 12 years, but up to 25 years depending on maintenance. Single-ply systems include TPO (thermoplastic polyolefin) and polyvinyl chloride (PVC) membranes which are low maintenance, energy efficient, and reliable against water and high winds. A 1.5-mm (60-mil), white color, thermoplastic polyolefin (TPO) membrane over lightweight concrete and expanded polystyrene (EPS) insulation was selected to provide an energy efficient and NOA compliant roof system.