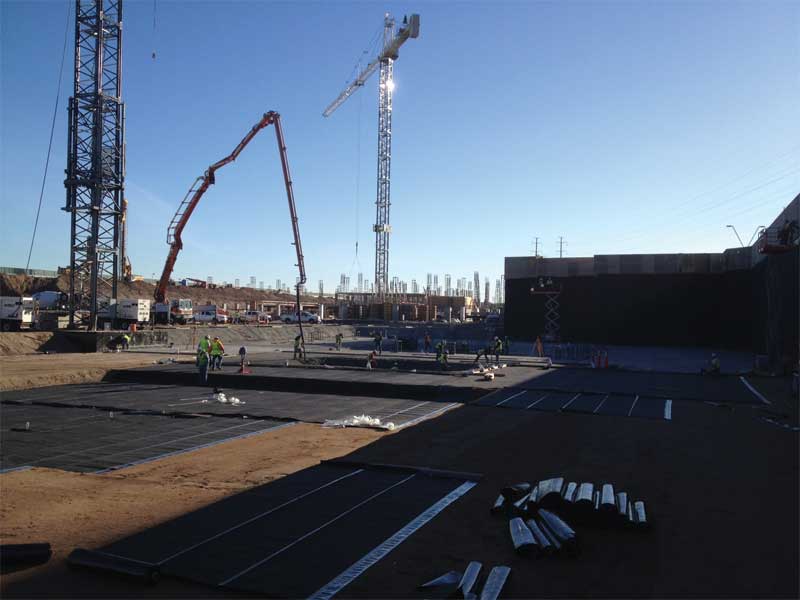
To keep these various groups informed and engaged, Intech held presentations and monthly public forums. They told the neighbors about the job—what to expect day-to-day and long-range. Meetings were convened ahead of any significant milestone in the work that might have an impact on the neighboring community—including demolishing the existing buildings, placing the mat foundation, and erecting and dismantling the tower crane.
They completed preconstruction surveys, which included photos to document existing interior and exterior conditions. Vibration monitors were installed in the neighboring buildings, including the Port Authority Transit Company rail tunnel, which abuts the site to the north.
There were some claims, Moses says, but that is to be expected on any urban site, especially one requiring more than two years of construction time.
“This was a very tight site with no room for laydown,” he adds.
That meant a constant stream of delivery trucks at certain points during construction. During the snowy winter, Intech’s trucks plowed the narrow streets and even carted trash to dumpsters.
However, perhaps the most compelling story was when a young couple scheduled a wedding at St. Mark’s at 3 p.m. on a Saturday, while the builders scheduled the foundation pour to start Friday night. The trucks arrived all night and into the following morning. Finally, by about 1 p.m., the crew began cleaning the streets and neatening the site. By the time the horse and carriage trotted down the street, at about 2 p.m., all was tidy.
MARINA HEIGHTS |
Spread across approximately 8 ha (20 acres), Tempe, Arizona’s Marina Heights is one of the largest office park developments in the United States. The project includes 185,800 m2 (2 million sf) of office space, 5575 m2 (60,000 sf) of retail, and two podium-based parking garages. The entire project is underlined by a below-grade parking structure—this means 8 ha of parking, says Buck Yee, project architect with the Tempe-based architectural firm DAVIS.
Marina Heights, built on the site of a former Arizona State University (ASU) parking lot, is hemmed in to the south by ASU’s football stadium, which is presently under renovation. Two major thoroughfares, Rio Salado Boulevard and Rural Road, border its other edges. Tempe Town Lake is located to the north. The developers of the site wanted to maximize land usage, so excavation began at the edges of the property. Waterproofing does not seem to be a major concern in the dry southwest, but the water table is only 9 m (30 ft) below grade at this location, and annual monsoons dump plenty of rain. Most of the building is atop subterranean parking garages, though elevator pits and other depressions go down as deep as 12 m (40 ft)—where there was water, according to Mark Storck, project manager for the Ryan Companies, the Minneapolis-based developer and general contractor. Other stakeholders include developer Sunbelt Holdings and DAVIS architects. The project is design-build. The first step below-grade was to build slurry walls to provide a first layer of protection and a substrate for the waterproofing. The team evaluated several waterproofing products and systems, ranging from concrete admixtures to bentonite. The latter was rejected quickly in favor of a composite sheet membrane. Due to its weight and stiffness, bentonite would be slow to apply, according to the contractors. The composite sheet membrane was flexible, affording quick, easy installation. This allowed the waterproofers, Firestop Southwest, to stay ahead of concrete contractors. “You can’t hold up concrete pours,” says Firestop’s Tracy Smith. “About the only thing tighter than space on this site was our schedule. Contractors can’t pour concrete until our installation is done.” Just delivering material to the site presented a logistical nightmare. Traffic was confined to a single in/out ramp. More than 305,825 m3 (400,000 cy) of soil were removed to make way for the two garages. Delivery of concrete, steel, and waterproofing materials was done in stages to provide room for storage while avoiding traffic jams. Altogether, approximately 78,970 m2 (850,000 sf) of waterproofing was installed over the course of about 14 months. After the membrane was installed, the waterproofers faced a jungle of rebar and more than 3000 soil nails, which were carefully detailed. The concrete was poured in lifts as work on the waterproofing progressed. Coordination among concrete and waterproofing contractors was paramount—planning meetings began almost a year ahead of the project commencement. Regular meetings continued during the project to make sure coordination was complete and the project was moving forward on schedule. |
Excellent points. Great case studies