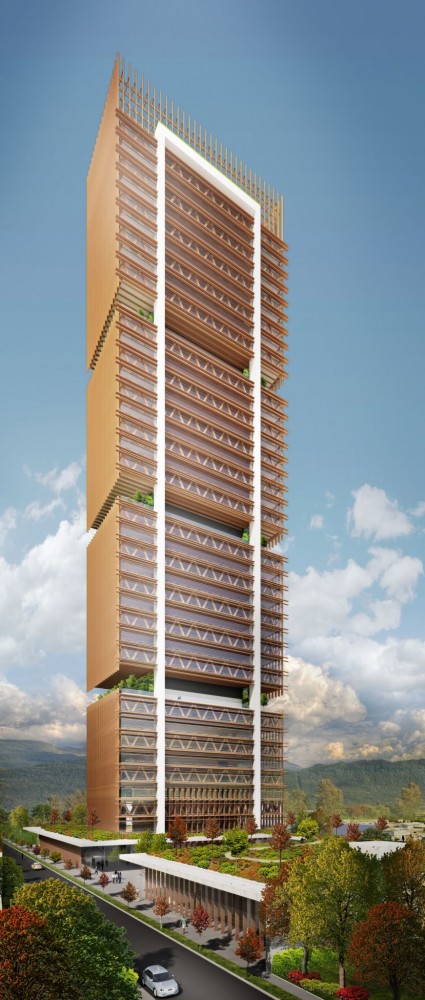
by Nick Bevanda, Architect AIBC, MRAIC, AIA, NCARB
In North America, wood in multi-story structures is becoming more prevalent, with some industry visionaries expecting to see high-rise within their lifetime. Today’s building codes, coupled with advances in building technology, have expanded the options for wood construction. As the effects of climate change become more evident, alternative construction methods should be explored by architects and engineers. One such option is to maximize use of wood throughout the built environment.
The growing exploration of engineered and hybrid technologies is driving the design of wood buildings to new heights. Such was the inspiration behind CEI Architecture’s design of a proposed 40-story office tower, planned for the realities of contemporary urban
office developments in a typical North American city, such as Vancouver.
CEI’s objectives for the project—conceived for a design competition by the NAIOP–Commercial Real Estate Development Association with a view to explore the potential for tall wood structures—included a design that would:
- incorporate advanced sustainable strategies;
- be visually iconic;
- be flexible to accommodate changes in tenant needs;
- attract tenants for its functionality and warmth; and
- respond to the climate and environment of the Pacific Northwest.
The team developed a design combining wood with other materials, minimizing concrete and steel as the primary support and emphasizing wood for secondary structural systems. The design proposed a building footprint of 45 by 27 m (150 by 90 ft) with a central concrete core. Floor decks were made of wood-concrete composite elements that take advantage of the wood’s tension capacity and concrete’s compression capacity.
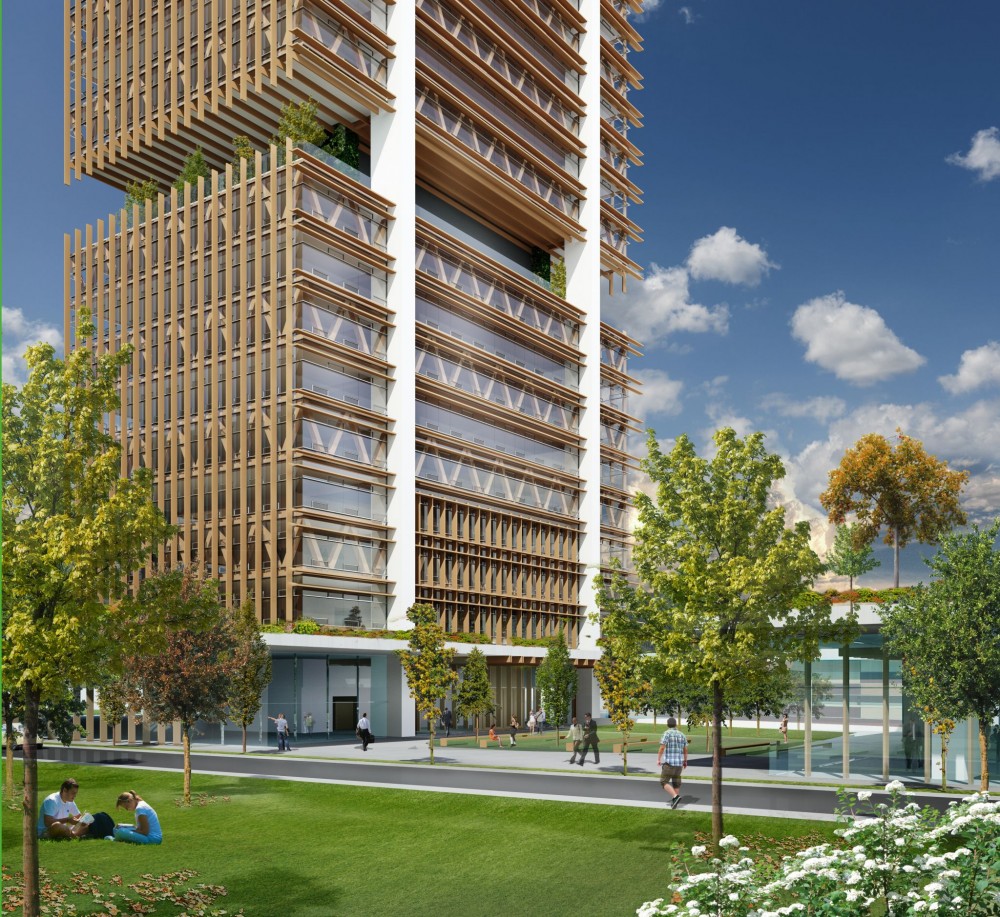
Floors are built from engineered panels spanning 9 m (30 ft) from the core to perimeter truss. An east-west axis helps maximize solar gain and control east-west exposure. Exterior sunshades are vertically oriented on the east-west elevations, with horizontal shades on the south that incorporate photovoltaic (PV) solar panels.
Preliminary project costing showed this plan could be constructed with a five percent savings over traditionally constructed office buildings that use concrete as their primary building material. This is due in part to the project’s construction time, which is predicted to be substantially quicker as prefabricated wood panels are delivered directly to site for construction.
Environmental performance
In addition to low cost, wood offers environmental, aesthetic, structural, and safety benefits in multi-story structures.
The choice of products used to build, renovate, and operate structures has a significant impact on the environment. When specifying any material, it is important to consider the environmental impacts throughout the lifecycle. Lifecycle assessments (LCAs) consider these effects from extraction or harvest of raw materials through manufacturing, transportation, installation, use, maintenance, and disposal or recycling. An environmental benefit of wood products are they have less embodied energy, are responsible for lower air and water pollution, and have a lighter carbon footprint than other commonly used building materials.
Trees and forest products play a critical role in helping to tackle climate change and reduce greenhouse gas emissions. Using wood products that store carbon—and responsibly managing forests in a way that balances harvesting and replanting—can minimize the carbon footprint over the long term.
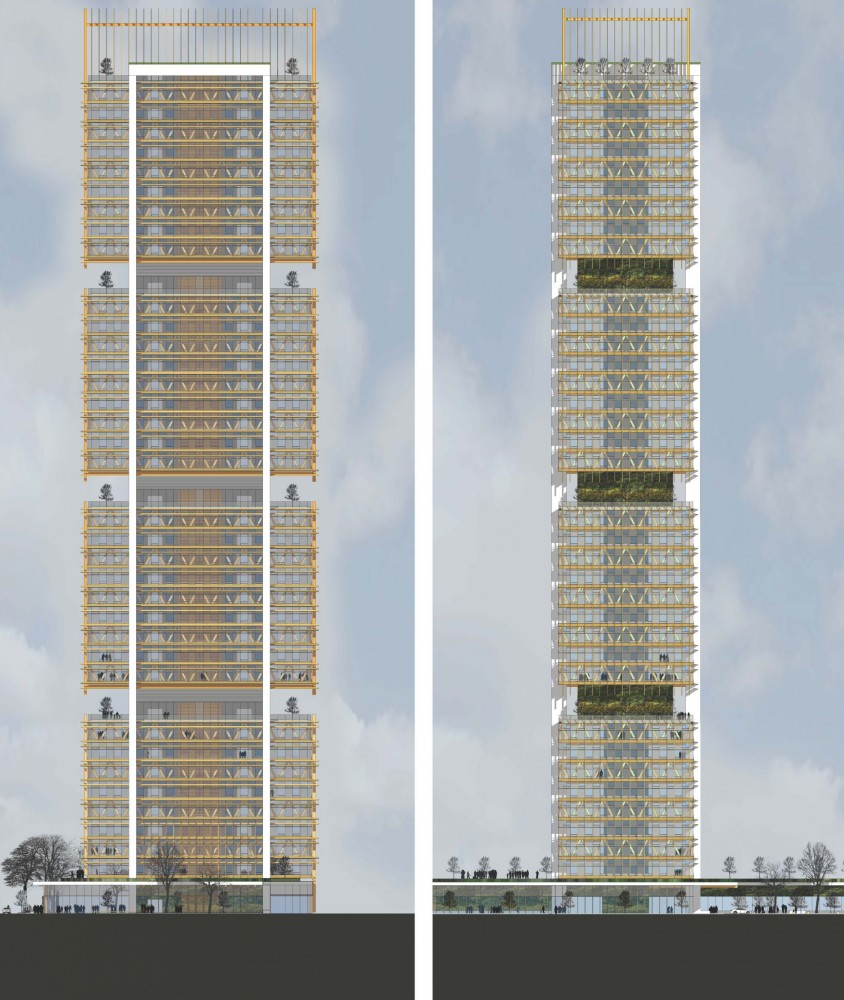
For the proposed 40-story office tower, CEI’s goal was to maximize the use of wood and propose innovative systems as a commitment to environmental sustainability. Building with wood would allow this proposed building to achieve many sustainable features, including sequestering more than 10,000 tons of carbon dioxide (CO2). This carbon remains embedded in the wood for the life of the building—essentially, until the wood rots.
The proposed 40-story tower also leveraged the benefit wood appeals to people’s senses, and can affect the building’s general atmosphere. These attributes, paired with the stress-reducing effects of biophilia (i.e. the instinctive connection and attraction people have to natural materials) have created a strong movement among architects to use wood in new facilities to create a more relaxing and productive work environment. FPInnovations and the University of British Columbia (UBC) recently conducted the study, Wood and Human Health,1 on wood’s connection to human health. The study found the presence of visual wood surfaces in a room lowered activation of the sympathetic nervous system, reducing the psychological stress of the building’s occupants.
The 40-story tower design incorporates engineered trusses using locally harvested wood. The visual presence would contribute to a warm, inspiring work environment, becoming the building’s primary architectural expression.
Structural viability
Engineered wood products offer exceptional stability and strength, and have made the material a viable alternative to steel in many applications where long spans and tall walls are required. Building codes recognize wood’s structural performance capabilities in a broad range of applications—from the light-duty repetitive framing common in small structures to the larger and heavier framing systems used for arenas and schools.
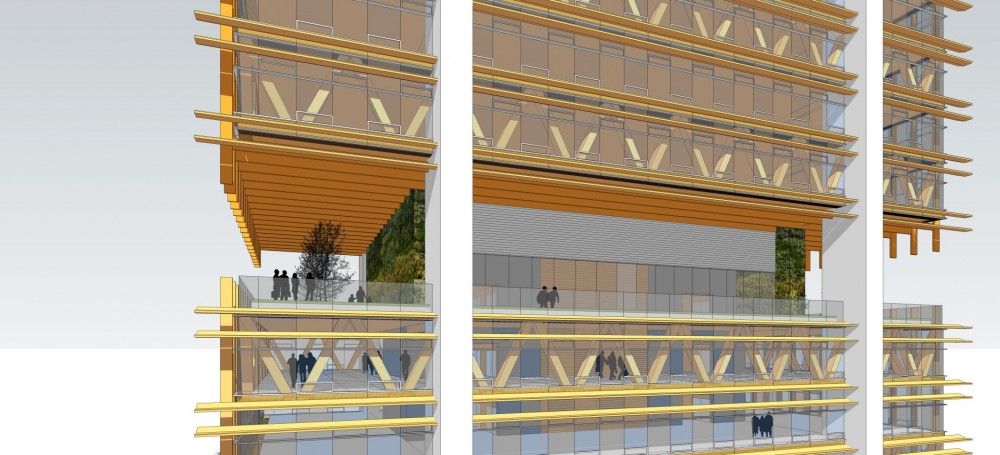
Michael Green, a well-known Canadian architect and wood enthusiast, recently gave a TED talk on why wooden skyscrapers should be built.2 He advocates the use of wood as a building material in order to end global housing and climate crises. During his TED talk, he proposed that it is not only possible to build safe wooden structures up to 30 stories tall, it is in fact necessary. Climate scientists around the world agree the effects of climate change will continue to accelerate if we do not take action. Sequestering substantial amounts of CO2, as is possible with tall wood buildings, is a step in the right direction.
Green recently conducted the report, Case for Tall Wood Buildings Study, which outlines a compelling case for taller timber structures. The comprehensive study’s proposed building model, dubbed Finding the Forest Through the Trees (FFTT), shows mid-rise (i.e. six to 12 stories) and tall buildings (i.e. up to 30 stories) can be safely, efficiently, and economically built using mass timber construction techniques. The New York architecture and engineering firm Skidmore, Owings, and Merrill LLP also recently released The Timber Tower Research Project, establishing the structural viability of a 42-story-tall prototypical mass-timber-framed building.3 This research project focused on the structural system of the building and the impacts it has on the other aspects of the design. (Non-structural items, such as the design of the exterior wall beyond structural coordination, were outside the scope of this project.) The result is believed to be an efficient structure that could compete with reinforced concrete and steel, while reducing the carbon footprint by 60 to 75 percent.
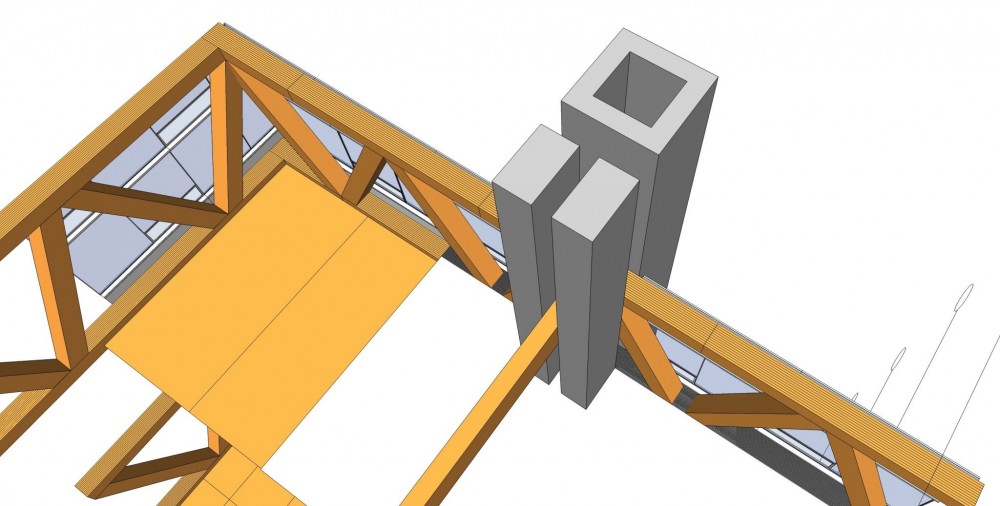
CEI Architecture’s proposed 40-story office tower incorporates a hybrid design to achieve a high level of structural efficiency. The design includes wood trusses with depths matching the 304-mm (12-in.) floor-to-floor heights. These are placed at the building’s perimeter at every alternate floor. The top and bottom chords of the trusses support the floor decks that span from core elements to the perimeter. The ability to support two floors with one trussed level would allow the building to have clear-span sky garden or sky lobby at chosen levels.
This aligns with the International Building Code (IBC), which recognizes wood’s safety capabilities and allows its use in a wide range of building types. These include multi-family, educational, commercial, industrial, retail, public, recreational, and institutional buildings. Building codes require systems to perform to the same level of safety, regardless of material used.
Wood-frame construction has a proven safety and performance record for fire protection, and the addition of sprinkler systems, fire-resistance-rated wall and floor/ceiling assemblies, and open spaces around the building can be used to increase the allowable size of structures. Heavy timber also has a particular advantage in a fire because it chars on the outside while retaining strength, slowing combustion and allowing time to evacuate the building.
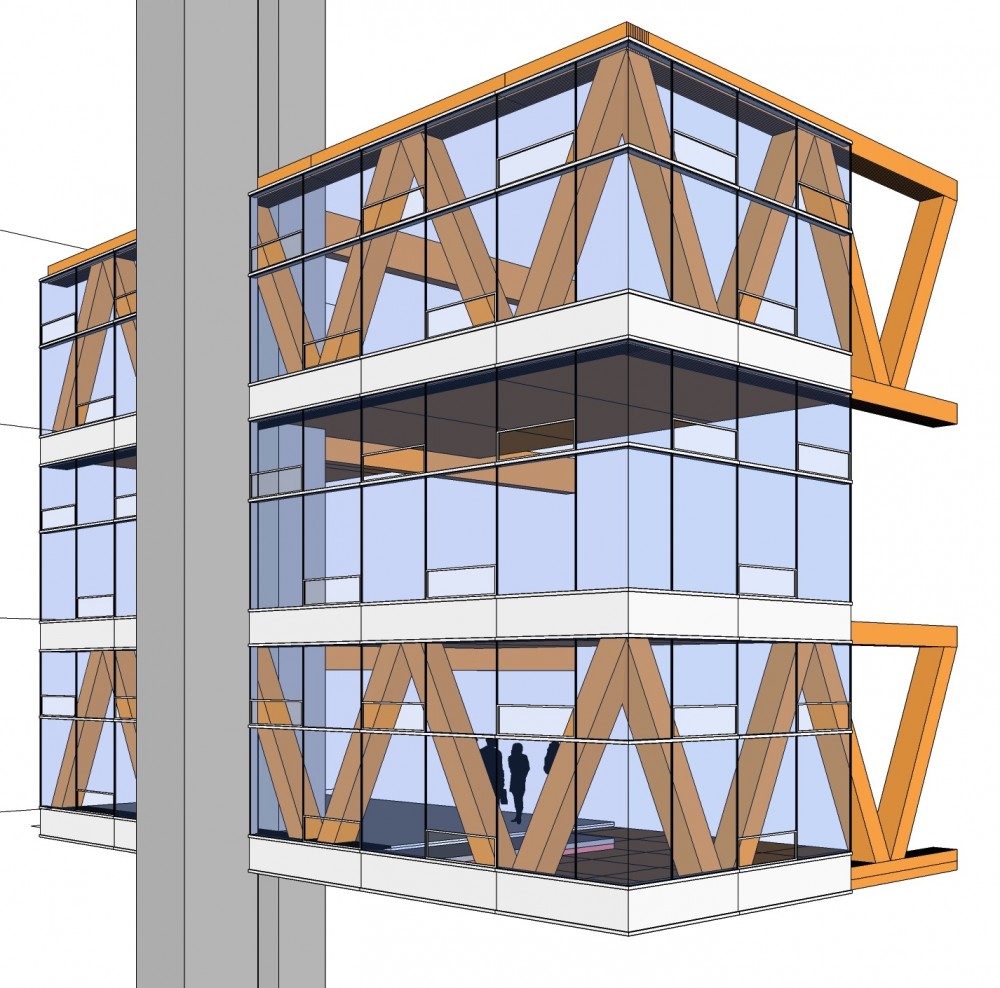
After IBC was introduced in 2000, most jurisdictions have adopted the code, along with its increased possibilities for wood construction by recognizing fire protection systems and techniques with a demonstrated history of fire safety in one of the legacy codes. Subsequent versions of IBC have expanded the opportunities for wood use even further through the application of additional state-of-the-art fire protection features.
Additionally, wood is lighter and more flexible, making it an ideal choice for earthquake safety considerations. Years of research and code development have demonstrated wood-frame and hybrid structures can meet or exceed the most demanding earthquake design requirements.
IBC defines site seismicity by means of seismic contour lines, proximity, construction type, and building occupancy, and provide numerical values for the acceleration used for design. The correct design of critical elements such as frames, shear walls, diaphragms, and their connections is of utmost importance as earthquake forces ‘search out’ the weak links between structural members. Where there is serious damage or collapse, it is often initiated by connection failure.

Forces in an earthquake are proportional to the structure’s weight, and wood is substantially lighter than steel or concrete. The fact wood buildings tend to have numerous nail connections means they have more load paths, so there is less chance the structure will collapse should some connections fail. This is also why they have inherent ductility, which allows them to dissipate energy when faced with the sudden loads of an earthquake. In this case, seismically engineered steal connections including bolt, screws, and adhesives would be used.
Further, shear walls and diaphragms (i.e. roofs and floors) constructed with plywood or oriented strandboard (OSB) structural sheathing over lumber framing are effective to protect against racking (i.e. distortion) caused by the lateral forces of an earthquake. In locations where there is a high likelihood of strong earthquakes, the stiffness and resistance of structural elements is bolstered by using thicker structural panels (on both sides if necessary) and increasing the number and size of nails.
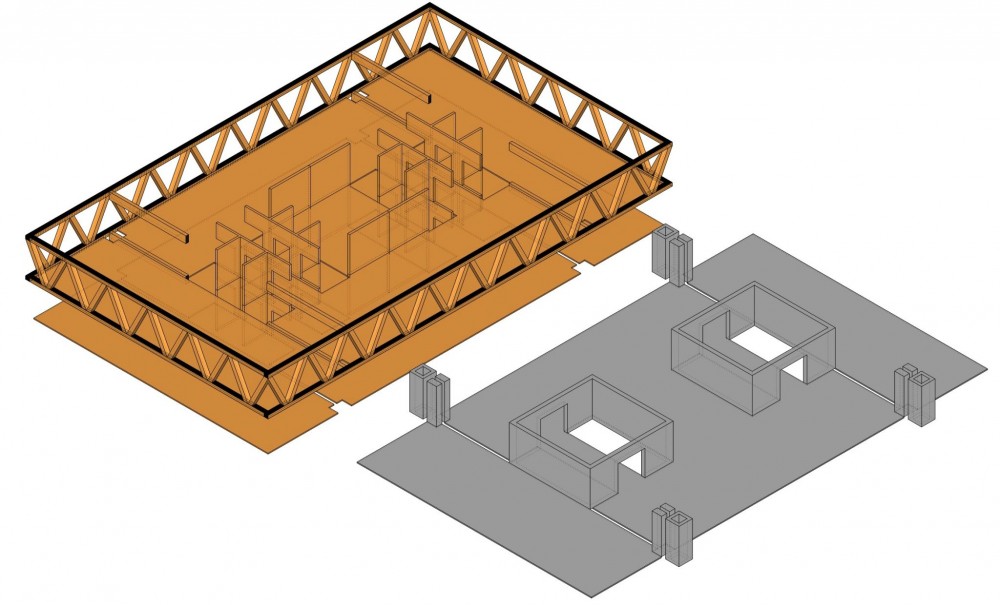
Finally, wood buildings can be effectively designed to resist high winds. Wind’s elastic limit and ultimate strength are higher when loads are applied for a short time, which tends to be the case in high wind events. When structural panels such as plywood or OSB are properly attached to lumber framing, they also form some of the most solid and stable roof, floor, and wall systems available. When used for diaphragms and shear walls, they can also resist high winds.
Conclusion
With growing pressure to reduce the carbon footprint of the built environment, wood can help achieve the balance between functionality and cost objectives with reduced environmental impact. CEI’s proposed 40-story office tower provided an opportunity for the team to explore the issues of constructing a tall office building from wood—achieving a design that meets structural and safety requirements, while creating an attractive working environment and a solution to limit greenhouse (GHG) emissions.
For now this project is a vision of what is possible. Awareness of the possibilities and benefits of building tall wood structures is increasing in the design and building communities, with the general public, and with decision-makers at several levels of government around the world. While current building codes in many jurisdictions limit how high buildings using wood as the primary structural material can be, the team behind this design believes some point in the not-so-distant future, this vision can become a reality.
Notes
1 To view the Wood and Human Health study, see www.fpinnovations.ca/MediaCentre/Brochures/Wood_Human_Health_final-single.pdf. (back top)
2 To watch Michael Green’s TED talk, visit www.ted.com/talks/michael_green_why_we_should_build_wooden_skyscrapers.html. (back top)
3 For more information about the Timber Tower Research Project, see www.som.com/ideas/research/timber_tower_research_project. (back top)
Nick Bevanda, Architect AIBC, MRAIC, AIA, NCARB, is a partner at CEI Architecture, where he brings a wide variety of experience both within the public and private sectors. Several of his projects have been recognized for excellence in design, including the Black Hills Estate Winery— winner of the Lieutenant-Governor of BC Award of Merit in 2008—and the Elenko Residence—honoured by the Design Exchange Awards in 2010. Bevanda can be contacted by e-mail at nbevanda@ceiarchitecture.com.