Environmental impact of concrete
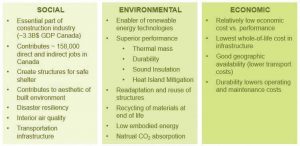
Images courtesy Lehigh Hanson
The primary environmental concerns regarding concrete are related to its CO2 footprint and the amount of energy required for manufacturing. These impacts are predominantly associated with concrete’s active ingredient, cement. Concrete is formed when cement is mixed with water, which binds the aggregate into a strong, cohesive structure. Cement production is energy- and CO2-intensive, but the product itself accounts for only 10 to 15 percent of the volume of a concrete mix. The other ingredients in concrete consist of aggregates, taking up 60 to 75 percent of the volume, and water, which accounts for around 15 percent of the volume (Figure 4).
Cement is manufactured by heating a mixture of ground limestone and other minerals containing silica, alumina, and iron up to around 1450 C (2642 F) in a rotary kiln. At this temperature, the oxides of these minerals chemically transform into calcium silicate, calcium aluminate, and calcium aluminoferrite crystals. This intermediate product, called clinker, is then cooled and finely ground with gypsum (added for set-time control), limestone, and specialized grinding aids, which improve mill energy consumption and performance to produce cement (Figure 5). Those calcium silicates chemically react with the mixing water in concrete, through a process called hydration, to form an extended network of bonds. These bonds bring the aggregates together and give concrete its characteristic strength and durability.
On average in the United States, 1 tonne of cement results in a global warming potential (GWP) of approximately 1040 kg CO2-eq. Approximately 1/3 of this is from the energy and heat requirements for manufacture, and 2/3 is from the calcination of calcium carbonate into calcium oxide and CO2.
How is the industry addressing sustainability?
The CO2 impact of concrete construction is due to the sheer volume required to keep up with global needs.
While the cement and concrete industry has long been committed to providing responsible and sustainable high-performance options, there has been a stronger focus on enhancing concrete’s inherent sustainability in recent years.
Cement
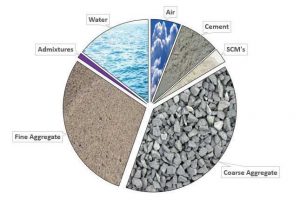
Cement producers have made significant strides in operational efficiency and heat recovery, plant modernization, and recycling of industrial byproducts as raw material sources. The cement industry is investing in many innovative technologies, products, and research projects on its journey towards carbon neutral concrete before 2050. Finding ways to reduce both the energy needs and reliance on fossil fuels is a top priority for cement companies and they have been making measurable progress since the early Seventies (more than a 40 percent) (For more information, read “U.S. and Canadian Labor-Energy Input Survey 2012.”).
On top of this, manufacturers are offering lower carbon products. Portland-limestone cements are specially formulated to provide performance equivalent to traditional Portland varieties, but with a portion of the limestone diverted past the pyro-processing stages and incorporated directly into the product. This avoids around 10 percent of the CO2 emissions from calcination and combustion.
SCMs, such as ground slag, are recycled materials that react with relatively inert byproducts of the hydration reaction (mainly calcium hydroxide) to form compounds that densify the cementitious matrix and enhance later age strength and permeability. SCMs are added to concrete as part of the total cementitious system, and judicious use is desirable not only for the technical advantages, but also environmental benefits. In Canada, it is common to see 25 percent replacement or more of the cement in concrete with these materials—this corresponds to a comparable reduction in manufacturing energy consumption and GHG emissions, as captured in environmental product declarations (EPDs). Due to these benefits, the industry is trying to increase SCM utilization and investigate new sources of potential materials.
The substitution of traditional fossil fuels with lower carbon alternatives derived from non-recyclable waste, including single-use plastics and waste biomass, has the potential to reduce the industry’s carbon emissions by 20 to 30 percent across Canada.
Finally, breakthrough carbon capture, utilization, and storage (CCUS) technologies could yield, when scaled, carbon-neutral or even carbon-negative cement and concrete.
Admixtures
Admixtures are small quantities of various nanomaterials or chemicals added to concrete to improve both performance and efficiency. They can provide air entrainment, control setting characteristics, and improve the workability and constructability of fresh concrete. For hardened concrete, they can increase compressive strengths, reduce shrinkage, and help lower permeability. Admixture producers are evolving their technology to enhance concrete’s durability and longevity, while reducing the need for higher quantities of environmentally intensive and costly materials within a particular mix.
Concrete
Concrete producers develop and optimize mix designs to balance the performance requirements of a project while minimizing the environmental impact, resource use, and waste. Several concrete associations in Canada and internationally have developed eco-certification programs for their members. The industry has also been diligent with developing independently verified regional EPDs for various mix designs to communicate transparent and comparable information about the life-cycle impact of products.
The academic research community is at the leading edge of testing and developing new materials and innovative technologies. This involves working with the standards community to identify requirements for material properties and use, developing appropriate test methods to measure performance, and ensuring the fitness of these products. This includes CCUS-related innovations, such as replacing virgin aggregate with alternatives manufactured from captured carbon as well as various methods for injecting carbon directly into the concrete mix as it sets.