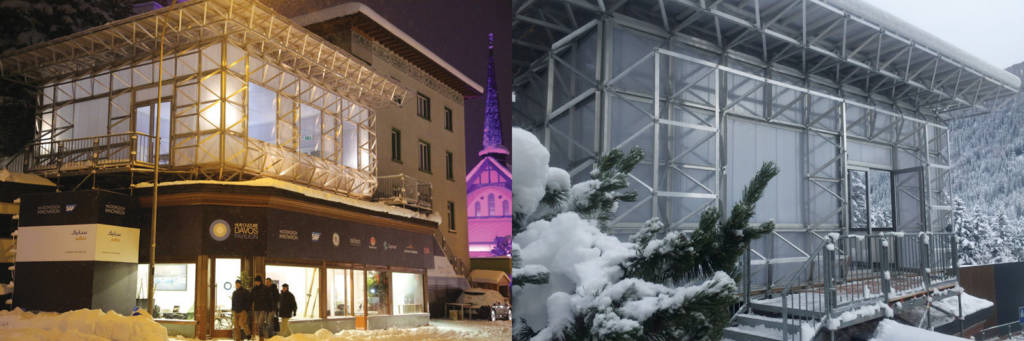
Photos courtesy SABIC
Giant’s Causeway visitor center
A new visitor center at the Giant’s Causeway, a designated UNESCO World Heritage Site in Northern Ireland, displays how polystyrene chemistry can be used for two important building objectives—sustainability and resiliency. Designed by Dublin-based firm heneghen peng, the facility’s vegetated roof offers panoramic views of the scenic Antrim coastline. The geometry of the cast-in-situ reinforced concrete roof contains varying slopes, angles, and fold lines onto which the IRMA was placed, helping to restore the natural ridgeline of the surrounding landscape while also enabling the structure to blend into its surroundings. In the future, indigenous grasses and wildflowers will naturally take root and cover the roof. The vegetated roof also allows rainwater harvesting that, in turn, reduces surface water runoff. The rainwater and greywater recovery from the roof is then routed through a recycling system, allowing it to be used for toilet flushing and roof irrigation.
An XPS product specifically designed for roofs was used to provide durable, moisture-resistant insulation to support thermal efficiency demands, as well as growth of delicate ecology in the area. Such boards have low susceptibility to rot, meaning mold and fungal growth is minimized. Further, the material has shiplapped edges offering interlock between boards, helping prevent thermal bridging and acting against wind uplift—particularly important in exposed conditions such as coastal Ireland.
The material also provides support for drainage layers and growth mediums or soil substrates on vegetated roofs due to its compressive strength sustaining high design loads. Inverted roof insulation must withstand constant loadings from ballast material, for example, without suffering substantial alterations to thickness that could affect thermal performance. The closed-cell structure of XPS gives the material its mechanical strength and a design load of 130 kN/m2 (2700 psf), with a maximum deflection of two percent over 50 years. Declaring the design load of insulation products allows specification against the building’s long-term requirements. The design load offers an indication of a material’s mechanical strength over a building’s expected lifetime—an important metric when it comes to quantifying resiliency.
Chemistry of polycarbonate
In 1953, chemists synthesized a viscous substance that hardened inside a beaker. Despite these chemists’ best efforts, the substance could not be broken or destroyed. Today, this high-impact material is called polycarbonate—a type of plastic known for its resistance to cracking and breaking, as well as for allowing the internal transmission of light nearly in the same capacity as glass.
Since its creation, polycarbonate has been used in a variety of applications, ranging from lenses for glasses or goggles to medical devices. The material’s toughness is useful when impact resistance and/or transparency are specified or required in a product, such as the sheeting used to create bulletproof glass.
A transparent, amorphous thermoplastic, polycarbonate sheet can be made in various colors and as translucent or opaque. Its applications include vertical or overhead glazing, as well as canopies, façades, security windows, shelters, and skylights. Thin, ultraviolet (UV)-resistant coatings can be applied to polycarbonate when it is extruded, offering enhanced protection for both performance and aesthetics.
The material’s chemistry makes it resilient to impact and to damaging weather conditions such as strong UV rays or hail. Polycarbonate panels were among the first window glazing materials certified under Florida’s Miami-Dade County building codes. In lab settings, hurricane-tested polycarbonate storm panel windows can successfully resist the impact of a 2.4-m (8-ft) long 2×4 fired from an air cannon at 55 km/h (34 mph). In another test of panel strength, a polycarbonate barrel-vault skylight was impact load and high-pressure tested to 19,727 Pa (412 psf)—the equivalent to 571-km/h (355-mph) winds.
Improved technology in cellular polycarbonate has led to new polycarbonate panel profiles, which are wider, thicker (ranging from 6 to 41 mm [0.25 to 1.6 in.]), and have as many as seven polycarbonate cells (eight walls).
In addition to impact resistance, polycarbonate panels offer opportunities for daylighting—a key component of sustainable building. Daylighting strategies can allow a building to operate without electrical lighting for 91 percent of the annual daytime office hours. U-values as low as 0.16 can be achieved through cellular polycarbonate panel systems comprising double-panels with an air space between the sheets. The material can also be recycled after use or simply reused.
In addition to windows and glazing, polycarbonate can be used as a primary material for a resilient structure. Terrorism, crime, and natural disasters such as hurricanes have led to increased demand for high-performing materials in evolving spaces—particularly where people do business, travel, and gather in large crowds. Polycarbonate sheets with hard-surface coatings, on one or two sides, offer a high level of resistance to abrasion, graffiti, and weathering in infrastructure projects like airports, rail stations, and metro rails. These sheets are also capable of bearing significant weight and wind loads up to 225 km/h (140 mph).
For example, the Shanghai South Railway station, which represents one of the largest buildings with polycarbonate sheets ever constructed, was updated with 55,000 m2 (592,015 sf) of tailor-made sheeting to increase the railway’s resiliency and durability. Much of the polycarbonate roof of the station covers the upper departure area, which is around 300 m (984 ft) in diameter and capable of holding up to 10,000 people.
Polycarbonate laminate sheets have also been engineered to help defend buildings—and their occupants—against ballistics impact, forced entry, and bomb blasts. Modern polycarbonate laminates may withstand both physical attack and gunfire from weapons ranging from 9-mm handguns to 7.62-mm NATO high-power rifles, giving more resiliency to construction projects that include embassies, government buildings, and corporate headquarters.