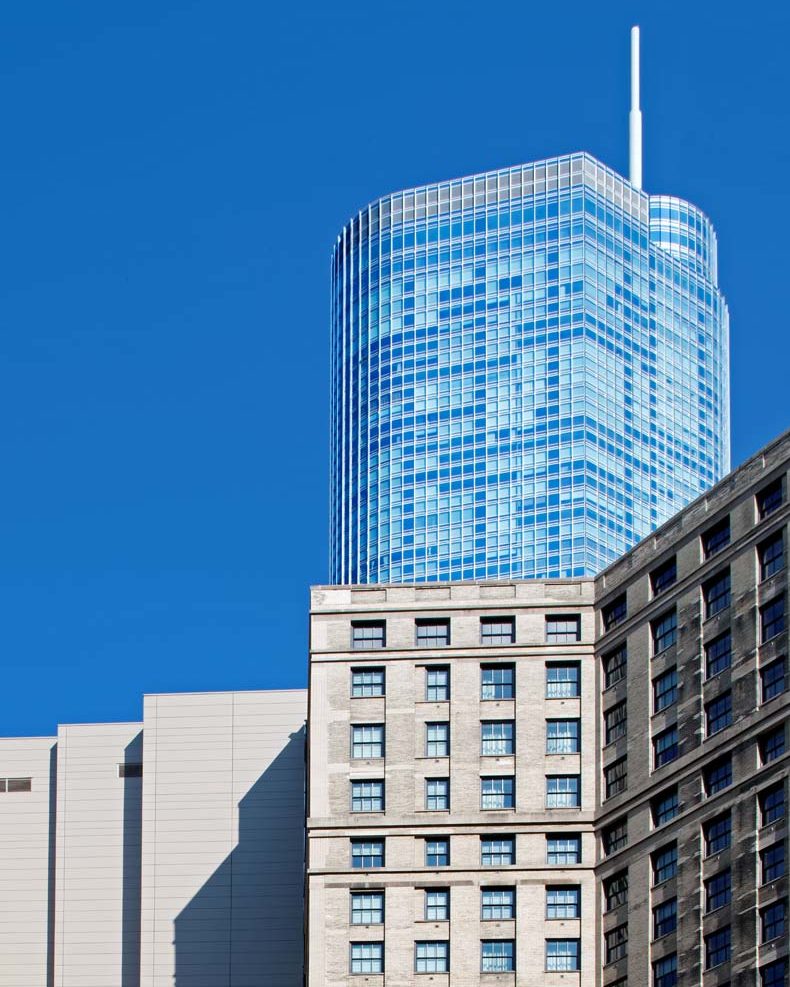
Photos courtesy Metl-Span
Back in 2013, Chicago’s historic LondonHouse underwent an extensive renovation. The transformation of this luxury hotel, completed for a grand reopening this past May, included the use of insulated metal panels (IMPs).
“The renovation consisted of adaptive reuse of the existing building and a new 22-story glass tower addition on the adjoining property,” says Randall Chapple, CSI, CCS, AIA, SE, LEED AP, an associate principal at Goettsch Partners Inc. of Chicago. “The goal was to create a boutique five-star hotel from the existing London Guarantee & Accident building. The building anchors one of the corners at the Michigan Street Bridge. Our goal was to breathe new life into the existing building and provide an addition that would complement the existing building. The location provided the opportunity to create an outstanding entertainment space on top of the building.”
When the London Guarantee & Accident Building was erected in 1923, it was one of the ‘Big Four’ skyscrapers at the foot of the Michigan Street Bridge. (The others were the Wrigley Building, Chicago Tribune Tower, and the 333 North Michigan Avenue building.) IMPs have been installed on the back side of its addition.
All American Exterior Solutions (Lake Zurich, Illinois) installed more than 2415 m2 (26,000 sf) of 914-mm (36-in.) wide panels and almost 185 m2 (2000 sf) of 610-mm (24-in.) panels. Both profiles, a 22-gauge outer skin and a 26-gauge inner panel, feature a 50-mm (2-in.) urethane core. They can be installed vertically or horizontally with concealed clips and fasteners in the side-joint. The 914-mm panels provide an R-value of 14.95.
“It’s not the face of the building facing Michigan Avenue, Wacker Avenue, or the river, so honestly, it was an inexpensive way to add R-value to the back of the building,” says the installers’ Mike Underwood.
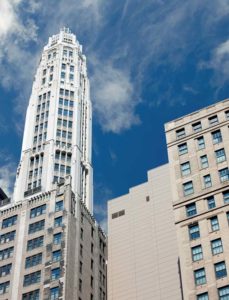
However, there were challenges with the limited space in which to work.
“We had no room to store product, so we would have a day or two’s worth of panels delivered at a time,” he says. “We were working on the back side of the building, over an alley, basically lowering panels to where we were installing and worked our way up.”
The renovated LondonHouse features 452 rooms and suites, 2325 m2 (25,000 sf) of meeting space, ballrooms, spa, unique social spaces, and restaurants, as well as the Windy City’s only tri-level rooftop venue and two floors of upscale retail space.
“The metal panels allowed us to design an enclosure to the addition that would complement the existing building and provide an economical solution that met the performance needs of the façade,” Chapple says. “The metal panels met our requirements for both weather and energy performance. They provided a complete pressure-equalized system that did not need to rely on additional components to provide a complete air, vapor, and weather barrier.”
“The aesthetics of the building for each façade was of great importance,” he continues. “Working with a manufacturer of metal panels that could assist us with the design of the façade to achieve an economical solution, while not sacrificing the performance of the façade, helped our firm achieve our goals for the project.”