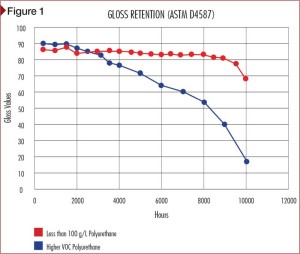
Images courtesy Tnemec Company
Water-based epoxy technologies have zero HAP per gallon and are low-VOC, which makes them suited for steel fabricators and OEMs. The coating technology has been successfully applied on:
- the interior and exterior of steel and concrete tanks;
- masonry;
- floors;
- both the structural and miscellaneous steel components; and
- interior wall applications.
New-generation low-VOC hybrid polyurethanes have demonstrated superior durability and toughness while outperforming standard aliphatic polyurethanes in architectural and industrial exposures (Figure 1). The high-solids, polyurethane technology resists ultraviolet (UV) light degradation and weathering, while retaining color and gloss; they are often used on industrial equipment, tanks, and structural steel. With less than 100-g/L VOC content, these formulations can be applied using brushes, rollers, or spray equipment.
Enhancing color and gloss retention in both interior and exterior exposures can still be achieved with water-based, low-VOC acrylic technology (Figure 2). With VOC content of less than 100 g/L, the single component coating has a fast curing time, which is important in coastal exposures subject to high humidity and salt fog.
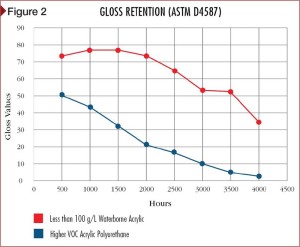
Low-VOC fluoropolymer technology is also being specified for exterior exposures requiring an ultra-durable finish, with color and gloss retention. With less than 100-g/L VOC content, the high-solids fluoropolymer resin is more stable than acrylic or conventional polyurethane resin and is more resistant to the damaging effects of UV light. Available in gloss, semi-gloss, satin, and metallic finishes, low-VOC fluoropolymer formulations offer the same performance of other fluoropolymer coatings containing much higher VOC levels.
Regulatory drivers
The growing list of low-VOC products enables specifiers to meet the challenge posed by myriad national, regional, state, and local rules—each with their own different coating categories and VOC content limitations. As shown in Figure 3, the regulatory rule-makers include:
- EPA;
- Ozone Transport Commission (OTC);
- Lake Michigan Air Directors Consortium (LADCO);
- California Air Resources Board (CARB); and
- South Coast Air Quality Management District (SCAQMD).
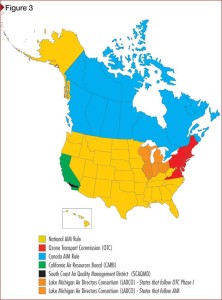
Covering most of the country, EPA’s National Volatile Organic Compound Emission Standards for Architectural Coatings (also known as the AIM Rule) creates minimum requirements for VOC content limits for 61 coating categories and sub-categories, while allowing individual states flexibility to adopt stricter policies within their jurisdictions. The national AIM Rule employs 450 g/L as the limit for industrial maintenance coatings.
OTC is more stringent than the AIM Rule when it comes to VOC restrictions on high-performance coatings. For example, the Ozone Transport Commission AIM Model Rule uses 340 g/L as the VOC content limit for industrial maintenance coatings.
California has had a major influence on the development of VOC coatings regulations since CARB was established in 1967. As part of the California Environmental Protection Agency, CARB’s model rule limits VOC content in industrial maintenance coatings to 250 g/L; this is enforced as required by the 2010 California Green Building Standards Code (CALGreen).
The most restrictive VOC coatings regulation is SCAQMD’s Rule 1113, which applies to the seven southern counties in and around the Los Angeles metropolitan area. VOC limits of 50 g/L for coating classifications such as “flat” and “non-flat” are not uncommon under Rule 1113. Many of the high-performance coatings sold in these counties are specifically formulated to meet SCAQMD’s 100-g/L limit for its industrial maintenance category.
Going ‘green’
Demand for low-VOC coatings that offer high performance is also being driven by private standard-setting organizations such as the U.S. Green Building Council (USGBC), Green Seal, and American National Standards Institute (ANSI).