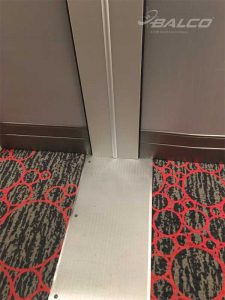
If the manufacturer says a product holds a load capacity of 907 kg (2000 lb), the question needing to be addressed is whether the 907 kg is for a contact area of 25 x 25 mm (1 x 1 in.) or 0.3 x 0.3 m (1 x 1 ft). That is a big difference in contact area and wrong calculations can cause wear, deformities, or damage. For example, if a pedestrian cover designed for foot traffic is used in a pallet jack pathway instead of one built to handle large loads such as carts, lifts, or shuttles, the cover plates of the expansion joint system can become dished or deformed, making it a bumpy ride or a tripping hazard for pedestrians.
The most common mistake made is an improper choice for traffic conditions. Expansion joint covers on floors are often thought of as pedestrian-only applications, but other unconsidered factors are heavy food, beverage carts, scissor lifts, and maintenance equipment that may also impact the joint covers and cause damage because pedestrian systems are too light-duty for these applications.
Expected placement and adjacent constructions materials
It is important to consider expected placement and the importance of adjacent construction materials, including wood, drywall, concrete, tile, concrete masonry unit (CMU), and carpeting. Adjacent materials, location, and functionality determine the mounting type. Options include surface mount, recess mount, and flush mount. The type of construction—whether new, renovation, or new-to-existing—also impacts the type of mountings used. For example, concrete blockouts are often employed in new construction to build a recessed joint for a smooth transition.
Expansion joints are placed where the building is most likely to have movement. They can be placed to join one floor to another, floor-to-wall, wall-to-wall, wall-to-ceiling, one ceiling to another, roof-to-wall, and one roof to another. Corners require due diligence in expansion joint placement because the materials are connected at multiple, intersecting points. This means adjoining building parts will move in both horizontal and vertical directions. If corner expansion joint systems are not designed and installed properly, structural damage such as vertical cracks will occur.
Expansion joints provide complete separations that frame out rooms, floor levels, building wings, or additions, as well as separation between buildings. Ideally, gaps should be minimal in size and the corresponding expansion joint system should be flexible enough to allow building parts to expand, contract, or shift while maintaining the connection. Materials differ depending on where they are used, but they must all work together to keep the building whole.
Transitions refer to the materials used adjacent to the expansion joint systems, and it is important these materials conform along with adjacent construction materials. For example, interior expansion systems must withstand foot and cart traffic, ADA compliance for slip-resistant flooring, and built-in fire, smoke, and water barriers. Flooring is a particularly important transition area. Floor finish materials like carpet, tile, marble, and finished concrete all have functional properties. One important property is their ability to deflect under maximum applied design loads. These materials can be incorporated into expansion joint floor systems for aesthetic purposes, but they must be properly specified, installed, and supported by the expansion joint system to keep the floor from cracking, spalling, or delaminating after installation.
Exterior expansion joint systems differ from interior systems as they must withstand the outside elements. Depending on the materials, exterior expansion joint systems need to withstand:
- drying out or cracking from sun and heat exposure;
- rust or deterioration from moisture, rain, snow, and condensation buildup;
- dirt and debris from strong winds; and
- weight loads on roofs.
Systems that can withstand frequent expansion and contraction without deteriorating are essential. This can be achieved with elastomeric systems in joints up to 100 mm and metal seismic systems in joints larger than 100 mm.
Several components can be built into expansion joint systems. Critical for safety and property protection, fire, smoke, and water barriers are common add-ons. Smoke blocks help isolate air leakage and keep smoke from spreading. These can be used alone or in conjunction with fire barrier and expansion joint covers.