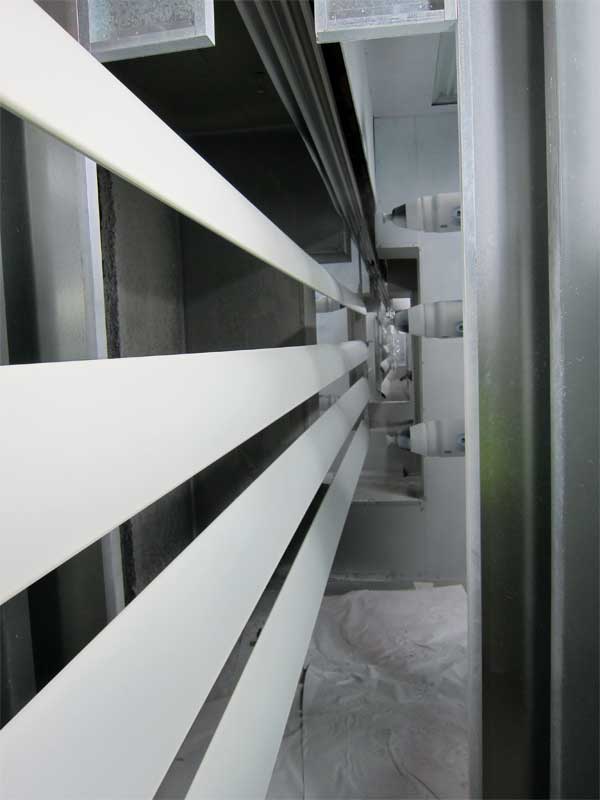
Photos courtesy Tellkamp Systems Inc.
The needs of state-of-the-art coatings
Many of today’s popular coating colors are grays or silvers, which lend a natural metal appearance to the substrate. These coatings contain embedded mica or metallic flakes. Metallic flakes reflect light according to the physics of specular reflection (i.e. light striking the flake reflects at the same angle as the incident) and have been commonly used in the industry for many years. Since metallic coatings need a clear spread in order to protect the aluminum flakes from moisture and ultraviolet (UV) light, mica particles have become a more popular choice. Mica flakes bend light, refracting it like a prism. They do not degrade when exposed to moisture and therefore do not require a clear coat, resulting in savings in product and application costs.
The multitude of angles at which light is reflected from a surface that contains mica flakes results in a scintillating, sparkling effect. Thus, a coating’s percentage of mica flakes, as well as the orientation of those flakes, makes a difference in how the color and sparkle of a finished surface are perceived. This means matching mica coatings on panels, extrusions, and other components can prove challenging.
Favorable results can be achieved, however, by following the proper order of production. There are differences in feasibility of color adjustment between powder, liquid, and coil applications. Adjusting the color is easier when working with liquid coatings because they can hold a greater percentage of mica flakes. Therefore, architectural components requiring powder coating should be produced first, and then matched in liquid. Additional variables are introduced in the coil coating process, which involves high line speeds and a lower film thickness than that of extrusions. This makes coil-coated metal more limited when using translucent pigments requiring higher film thicknesses. Further, when using a coating with mica flakes, the velocity of the coil coating process imparts a horizontal orientation to the flakes, which makes the final composition more directional and less random than it is in other applications. Like the powder-coated components, coil components should be produced before liquid-coated ones to take advantage of liquid’s adaptability.
Mica flakes are susceptible to breakage in certain types of guns. While some spray guns have an electrode at the tip to generate negative ions, others use an electrostatic rotary bell, also called a rotary atomizer. A key component of the rotary bell gun is the bell cup (a funnel-shaped attachment located at the end of a turbine). Coating material is fed into the rear of the bell and centrifugal forces then pull it toward the bell’s wider, open end. A mechanical shearing action breaks the coating into atomized droplets.
Traditional liquid paints perform well when applied using a rotary bell; they break into droplets of similar size and produce uniform coverage on the coated surface. However, coatings containing mica or metallic flakes do not fare as well. The breakage—a normal part of a bell’s atomizing process—fragments the flakes and alters the way they are oriented in the final finish. This, in turn, disrupts the flakes’ ability to reflect light, resulting in a perceived lightening (or darkening) of the finished surface.
Intermediary steps of color matching between components is the solution to this issue, just as it is when matching powder-, liquid-, and coil-applied coatings. Coating manufacturers should avoid running large, single batches to fulfill an order. Instead, their batches should be coater-specific or coil manufacturer-specific.