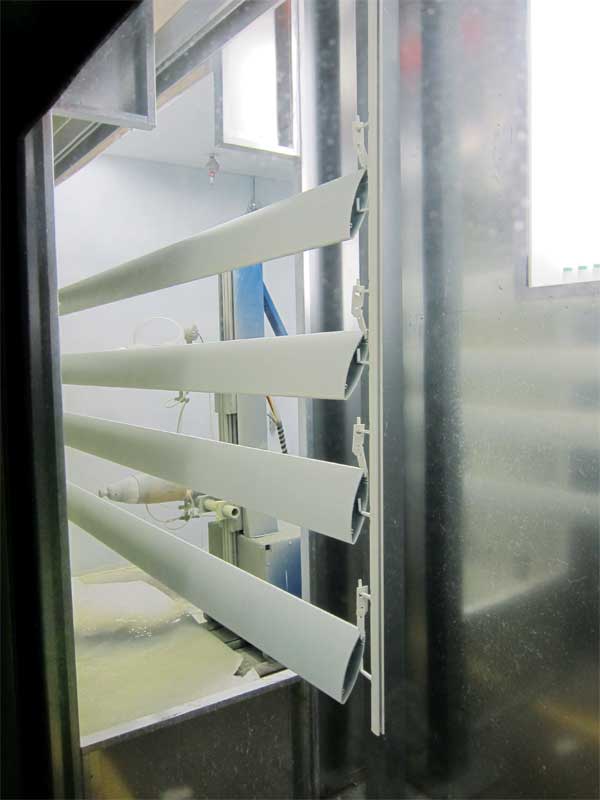
Fighting physics
While electrostatic coating processes rely on the laws of physics, certain forces can impede product transfer and evenness of coating coverage. For example, negatively charged particles are attracted to the closest grounded surface, which has the benefit of both attracting the coating to a part’s edges and reducing overspray. However, this same tendency can make it difficult to achieve even coverage in the deep, recessed areas commonly seen in aluminum extrusion profiles. Particles are attracted to the prominent edges of the profile, experiencing what is known as the Faraday cage effect, and can create a thick layer of coating prone to blisters.
Reducing the fan pattern of the spray can direct the ionization field toward the recessed area. If a part is being hand sprayed, the technician can move closer to the workpiece. Gun target distance should be kept within 203 to 305 mm (8 to 12 in.) from the part being coated. As distance decreases, the operator needs to reduce the fluid or air pressure—or in some cases, both—to avoid applying too much coating. Further reducing a gun’s voltage allows more of the coating to pass by the sharp edges of the extrusion and penetrate its recessed areas. To achieve optimum performance, gun voltage must be between 50 and 70 kV for powder coatings. Liquid coatings are often applied at 60 to 80 kV. For both liquid and powder formulations, manual adjustment during the coating process accomplishes better coverage in areas of extrusions experiencing the Faraday cage effect.
Another consideration is the size of a coating’s particles. The amount of charge a particle carries is directly related to its surface area. If a large droplet of liquid paint breaks into smaller droplets during the application process, those smaller droplets will have a combined surface area that is greater than the surface area of the original, larger drop. Having a greater total surface area for the same volume means the coating is carrying a greater electric charge and will be affected more by the attractive forces created between positive and negative charges. This means smaller droplets have a greater affinity for edges
and sharp corners and have less ability to penetrate recesses. Equipment operators can reduce fluid and air pressures to create larger droplets. Reducing the voltage on the coating gun also produces larger droplet sizes and enables the momentum generated by equipment to drive the coating into the recessed corners. It is not uncommon to adjust both voltage and atomization to provide the best coverage.
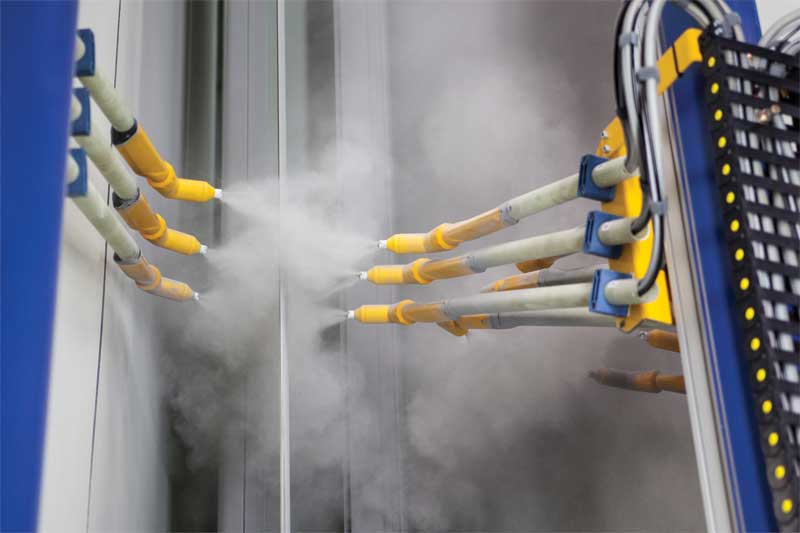
Every liquid coating needs a balance of true active solvents and diluents. Solvents commonly reduce the raw coating by 25 to 30 percent. Additionally, the solvents employed must be both polar and nonpolar and also have a range of evaporation rates. Varying solvents’ evaporation rates and their conductivity manipulates the way in which particles charge and discharge as they travel along the path to their target. (Typically, for proper transfer, the coating should have resistivity that ranges anywhere between 0.5 to 1.5 megaohms.) It is critical the tail solvent—the last solvent to evaporate out of the coating—be an active one for the resin system being used, because it must perform the function of dissolving the ‘skin’ (the partially crosslinked coating surface). If an inactive solvent is the last to evaporate out of a coating, blisters or ‘solvent pops’ will form. Temperature and humidity should also inform the ratio of fast- and slow-evaporating solvents being used. Additionally, volatile organic compound (VOC) restrictions or caps in the location where a material is being coated may influence solvent selection and volume.
Powder coatings must have the correct average of large and small particles for optimal transfer efficiency. If over-sprayed powder is being reclaimed and reused, virgin powder needs to be added to the hopper at a rate calculated to maintain the specified particle size average balance. Monitoring this balance during the application process is key.
Temperature and humidity can also affect powder particles. The optimal temperature range is 20 to 27 C (68 to 80 F)—too much heat causes particles to prematurely cure or fuse. Humidity should range between 47 and 55 percent. High humidity can cause clumping of particles. To correct this, airflow into the hopper can be increased or a prep stage can be added to the process to break up the clumps.