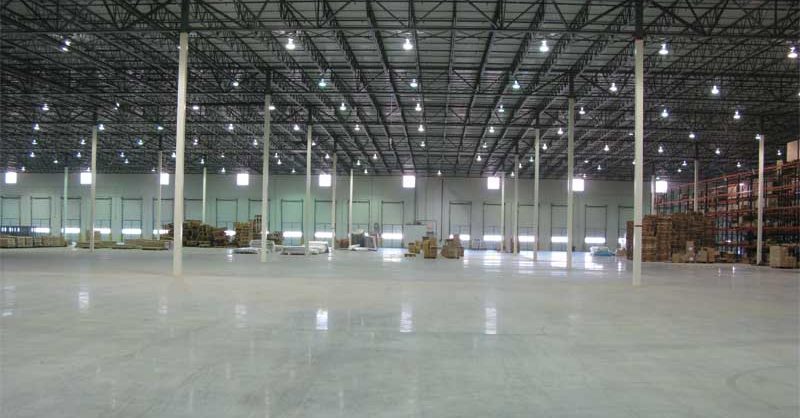
by George R. Mulholland, PE, SE, and W. Joseph Macicak, PE, SE
Concrete has long reigned as the material of choice for many structural floors, but inherent difficulties with its use continue to be a source of disputes on construction projects. Concrete cracks, shrinks, and curls, requiring careful design and skilled installers
to achieve flat and level surface profiles. Slabs incorporate joints that move and require maintenance, and
their deflections are not completely predictable. Often, it is the treatment of these inherent difficulties that makes the difference between a successful slab construction project and one plagued by defects and missed expectations.
When design and construction practices do not meet the owner’s expectations, disputes arise, often followed by legal action. It is therefore critical the entire construction team—design professionals, owners, construction managers, general contractors, and subcontractors—understand the limitations and potential pitfalls associated with concrete slab construction. This understanding is just as important to the success of the project as is adhering to proper design and construction practices. Active involvement of the entire construction team, including the owner, is strongly suggested. Highly effective communication between team members allows realistic expectations to be set and adjustments made, if necessary, to achieve desired outcomes.
Ideally, the owner and design professional will begin discussing expectations prior to designing the concrete slab. The owner typically wants an economical, worry-free slab requiring little maintenance. To meet these expectations, provisions to minimize control and construction joints, limit crack widths and number of cracks, and achieve a flat, level surface will likely be considered. For elevated slabs, minimizing deflections and vibrations must also be taken into account.
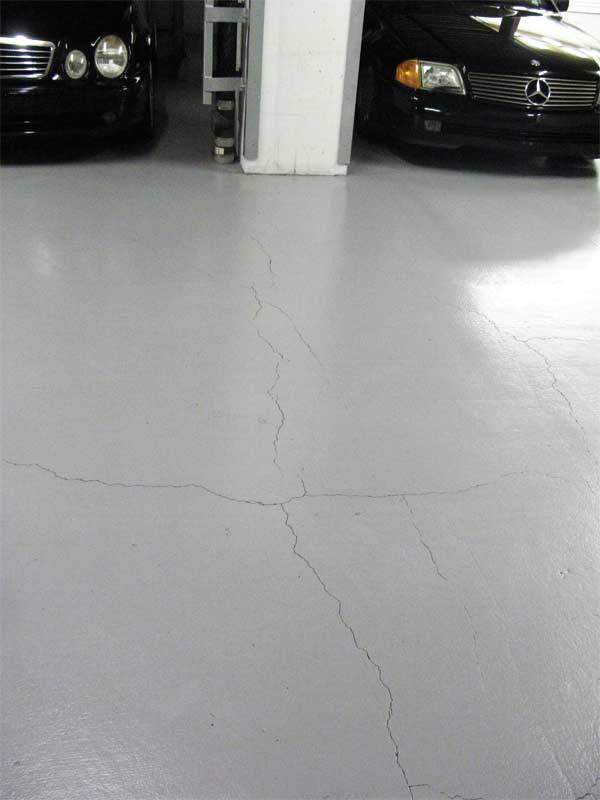
The designer can use these discussions as an opportunity to explain cost versus benefit tradeoffs, which allows owners to refine their expectations. For instance, control of crack size and spacing is largely determined by the quantity of distributed steel reinforcement within the slab and the shrinkage limits of the concrete mix. Additional distributed reinforcement provides better crack control, but increases costs; further, local availability of mix ingredients may limit the design professional’s selection of mix types. Discussions between the owner and design professional prior to design should address the slab’s anticipated use, life expectancy, and maintenance requirements, as well as any overall expectations.
Communication between the owner and design professional should be ongoing during the predesign, design, and construction phases of the project. Owners should have the opportunity to be part of discussions when critical construction decisions are being made. They should also consider attending project meetings, despite the fact this has not historically been common.
Typically, communication begins during the bidding phase. Potential slab construction issues should be discussed thoroughly with the contractor prior to the start of construction. The design professional should strive to provide a slab specification that is as complete as possible, based on the specific expectations of the owner, and ensure the contractor understands its extent and limitations. The specification should acknowledge the uncertainties associated with slab construction and provide proactive protocols, such as crack remediation procedures or the inclusion of allowances for leveling material to address flatness or deflection deficiencies.
Further, miscues can occur if the design professional is unfamiliar with local limitations, so these should be discussed during preconstruction meetings. For example, adjusting the design (e.g. revising the mix design based on the local availability of ingredients) before slab construction commences may be beneficial.