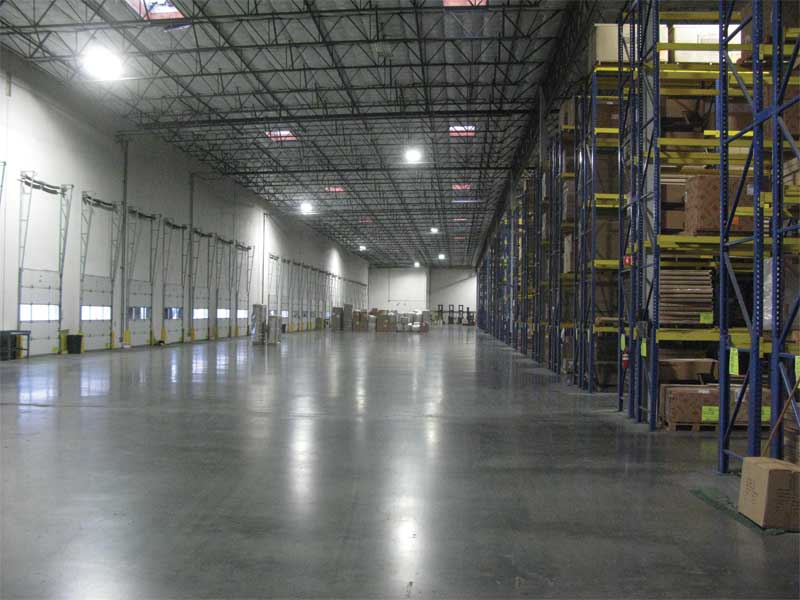
When disputes occur
Despite the availability of numerous highly skilled and experienced concrete slab designers and contractors, there is still frequently defective construction, missed expectations, and legal disputes, often arising from paying inadequate attention to the aforementioned limitations and difficulties prior to construction. These authors have come across several projects illustrating how disputes—and sometimes legal actions—arise when owner expectations are not properly understood or repair actions are not clearly defined. The following are a few examples of aspects that should have been addressed before construction.
Crack control
A large warehouse incorporated a lightly reinforced slab-on-grade by a design professional from another part of the country. Prior to design, the owner expressed its desire
for minimal cracking within the slab. Although several discussions regarding the likelihood of cracking and the proposed slab joint spacing took place between the design professional and the local contractor, they disagreed over whether the slab, as designed, could be constructed to meet the owner’s expectations for crack control. Ultimately,
the design professional elected to dismiss the contractor’s concerns, and left the original design intact with regard to slab reinforcement, shrinkage limit on
the concrete mix, and joint spacing
(which exceeded industry standard recommendations). Additionally, the project documents contained no specific slab repair guidelines addressing the number and size of cracks, slab curling limits, or control joint width limits.
When the finished slab exhibited excessive cracking, curling, and control joint widths unacceptable to the owner, investigation and legal action resulted. During subsequent floor slab investigations, reinforcement placement was found to be inconsistent, some slab areas appeared to have been improperly cured, and the subbase was not consistently level. As a result of the inadequacies of the original design and poorly executed construction, the finished slab could not support the intended loads, and its anticipated life cycle was diminished. These defects may have been avoided had the construction team members understood the importance of achieving mutual understanding and consensus prior to construction.
Even if the design professionals and contractors disagreed on specific portions of the design or construction methodology, the establishment of repair guidelines with acceptable limits for slab cracking, crack size, curling, and joint widths could have been used to provide a protocol for resolving issues without resorting to legal proceedings. These repair guidelines acknowledge uncertainties exist, help the owner manage expectations, and emphasize the importance of maintaining proper construction techniques.
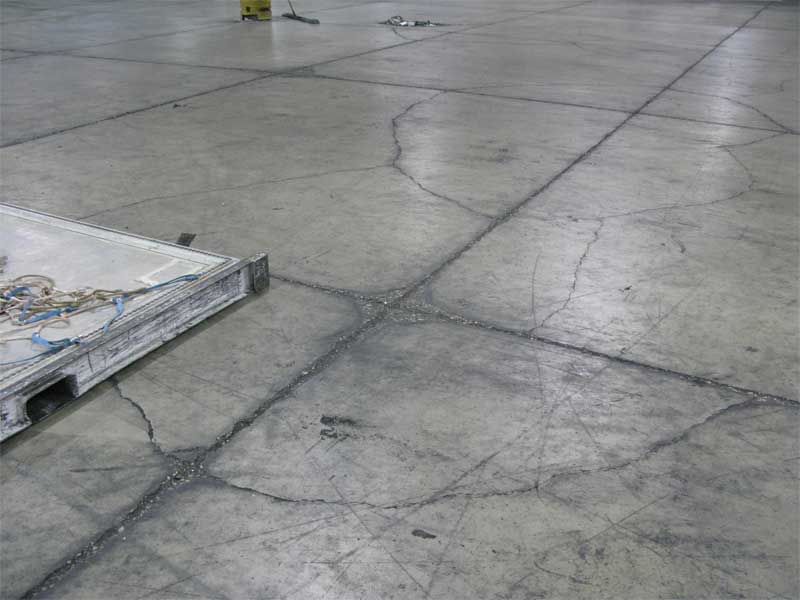
Usage intensity
Another large warehouse incorporated
a 152-mm (6-in.) thick concrete slab-on-grade, lightly reinforced with welded-wire fabric and originally designed for light-to medium-duty usage. After approximately 10 years of light-duty use, the slab exhibited little to no signs of distress. At that time, the property was leased to a new tenant, who planned to change the usage within the warehouse to heavy-duty, but did not convey the intended use to the owner.
A design professional was engaged to detail several large-capacity in-slab scales for the existing slab-on-grade, but apparently did not realize the new scales were designed for loads far exceeding the capacity of the adjacent existing slab. The contractor, which cut and removed portions of the existing slab to install the large scales, did not recognize the lightly reinforced slab was incompatible with a large-capacity scale.
Following installation of the scales, the existing slabs experienced severe joint raveling and spalling due to excessive loading by the new tenant’s large forklift trucks. During a subsequent dispute between the owner and the new tenant, analysis showed a slab more than twice the thickness of the existing one was needed to properly support the new forklift loads. Had the proposed new usage of the facility been thoroughly discussed by the owner, the new tenant, and the design professional prior to design, it is likely the existing slab’s capacity limitations would have been obvious, and other building lease options for the tenant—or slab replacement—could have been considered.