By Chris Bennett, iSCS, CDT, James Longo, iSCS, and Keith Robinson, RSW, FCSC, FCSI, LEED AP RSW, FCSC, FCSI
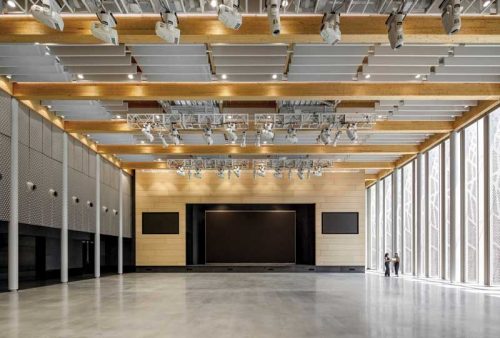
Concrete floors are used in wide-ranging facilities, such as industrial data centers, commercial high-rise buildings, and residential homes. Concrete floor quality depends on several factors, including the concrete mix design, the curing process, including consolidation and finishing. However, one of the seemingly simple, but often complex aspects of concrete floors, impacting performance and functionality, are floor flatness (FF) and floor levelness (FL).
In a world where project manuals require competing benchmarks for concrete and flooring, as well as vagueness on responsibility within the flatwork and flooring trades for ultimate responsibility for FF/FL, it is important to understand these two factors and how they affect not only the overall quality of concrete floors (and other floor finishes), but what is the best way to go about designing and specifying for the best outcome possible.
Floor flatness and floor levelness
Floor flatness refers to the smoothness and uniformity of the concrete surface. It is measured by calculating the height difference, between the highest and lowest points on the surface over a specified distance. The flatness of a concrete floor is critical in many applications, especially in commercial and industrial settings where heavy machinery and equipment are used. A flat floor ensures the equipment operates smoothly and efficiently, reduces the risk of damage to the machinery, and improves safety for workers. A non-flat floor can also cause problems with the installation of flooring materials, such as tiles or carpeting, which require a level surface (Figure 1).
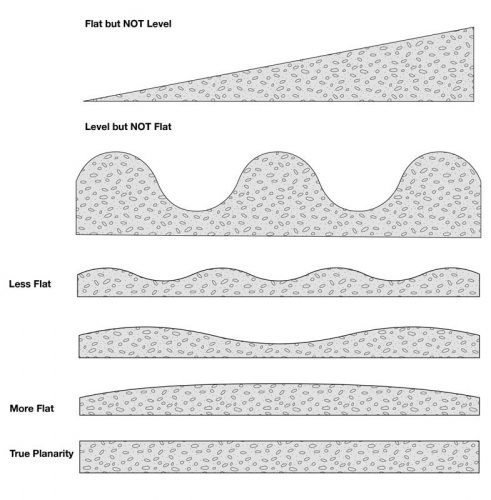
Floor levelness refers to the evenness of the concrete floor in terms of its slope and elevation. It is measured by calculating the difference in height between the floor surface and a designated reference point, such as a horizontal plane. Floor levelness is essential for various applications, such as building foundations, where a level floor ensures the load is evenly distributed and the structure remains stable. It is also critical in commercial and industrial settings where liquids are stored or transported, such as food processing plants, where a level floor ensures the liquids flow uniformly and do not accumulate in certain areas.
Levelness and flatness
To achieve the desired level of flatness and levelness in concrete floors, various techniques and tools are used. Getting consistent FF and FF on concrete slabs requires careful planning, execution, and quality control (QC) throughout the construction process (Figure 2, page 31).
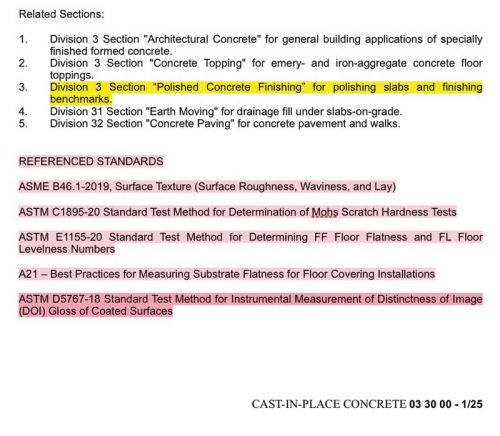
Here are some general steps that can help to achieve consistent FF and FL:
Start with a flat, compacted, and level base
Before pouring the concrete, ensure the base on which the slab will be constructed is level and flat. This can be achieved by properly grading and compacting the soil, and using a laser level or other equipment to ensure the base is within the required tolerances.
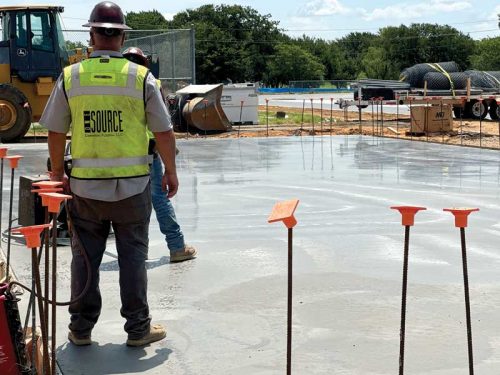
Use the right mix design and curing techniques
Brian Earl, principal at ZGF notes, “While the concrete mix is an important factor in the overall appearance of the concrete, greater attention to curing is critical to avoid undulation, curling, and other factors that affect flatness. This is particularly true for exposed concrete in representational spaces like the Event Center at HQ2.”
Moreover, proper curing techniques can help to prevent cracking and warping of the concrete, which can affect its flatness and levelness. The latter is especially true with newer low-carbon mix designs where older methods of curing (i.e. topical spray applications, membranes, etc.) may not cure sufficiently to reduce undulation, curling, and other manifestations of reduced FF and FL Internally cured concrete (ICC) approaches can dramatically reduce volume change through better curing.
Control the placement and finishing process
During the concrete placement and finishing process, it is important to control the rate of placement, use the appropriate tools, and properly consolidate and level the concrete to prevent the formation of air pockets or voids.
The use of a power trowel, laser screed, or other finishing equipment should be carefully controlled to prevent trowel marks or other irregularities that can affect FF and FL. Trowel harmonics, vibrations, and resonances that occur when a power trowel is used to finish new concrete, can play an important part in missing or achieving one’s benchmarks. Different blades as well as the speed and angle of troweling will affect the plastic concrete differently.
Perform QC testing
Throughout the construction process, it is important to perform regular QC testing, such as using a laser screed or other equipment to measure FF and FL. This can help to identify and correct any issues that may arise during the construction process, and ensure the finished slab meets the required standards.
By following these steps and working with experienced concrete professionals, it is possible to achieve consistent FF and FL on concrete slabs.
Measuring FF and FL of concrete
FF and FL are measured in accordance with ASTM E1155 for slabs on grade. For elevated slabs, FL is only valid at placement and before shoring is pulled, but the FF factor will remain important. Standardized measurements are employed at regular intervals, uniformly distributed across the test section, properly distanced from slab boundaries, construction joints, and other breaks in plane
(e.g. block-outs or penetrations). Testing must be conducted within 72 hours of concrete placement and prior to removal of any shoring to comply with the test standard.
The adoption of the standardization of FF/FL testing in Division 03 allows for uniform testing of concrete slabs during the threshold inspection, delivering results to the architecture and engineering team, showing compliance to or failure in meeting design specification requirements.
The ASTM E1155 measurement standard was developed for use with concrete finishing and confirming structural tolerances at the fixed point in time described above. Although referenced for use by other trades affected by FF/FL, its use is limited because data are made along defined lines of measurement and do not provide an overall evaluation of smoothness and evenness, which is better evaluated using straight edge measurements as described below.
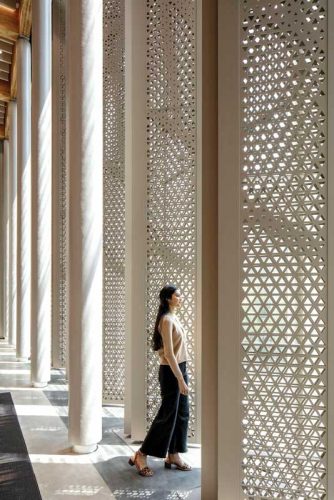
Measuring flatness for flooring
In contrast to FF/FL testing for the concrete, the flooring industry employs the straight edge method for floor flatness. Straight edge measurements are indicated in the allowable deviation in plane over a specific distance, such as 6 mm (0.2 in.) deviation in 3 m (10 ft) span represented as 6 mm in 3 m (0.2 in. in 10 ft).
There are three primary challenges that result from the “inches and feet” straight edge method and the FF/FL method:
- This is no correlation between the FF/FL values and the inches in feet values.
- The straight edge method does not require specific placement techniques for evaluation, leaving an unlimited amount of variability dictated solely by the tester.
- The time between Division 03 FF/FL testing and floor flatness straight edge testing are typically several months, up to a year apart.
- This means natural variations in flatness and levelness that occur as concrete cures and desiccates, decreases the initial values obtained within 72 hours obsolete.
- The initial values can change between 20 to 40 percent as a minimum expectation or as much as 50 to 70 percent, depending on how the concrete was cured, the FF/FL value specified, the weather conditions concrete experienced during construction, the type of concrete mix used, or the early application of loads on the finished concrete surfaces.
- An initial value of FF25/FL20 may decrease to FF15/FL17 in a worst-case scenario, making the concrete substrate unacceptable for most floor covering manufacturer’s straight edge measurement requirements.
When floors are measured for flatness, concrete has substantially cured. That curing alters the flatness profile of the concrete. While there is too much variability to define specific or typical values in flatness change over time, it is not uncommon for concrete to undergo these changes over a period of six to 12 months after placement. When the floor covering installer contractor initiates straight edge testing, the concrete flatness may not be indicative of the slab delivered by the concrete contractor within 72 hours after placement and will likely require some degree of wet or dry mechanical grinding to correct the natural decrease in floor flatness and levelness tolerances before they are called to site.
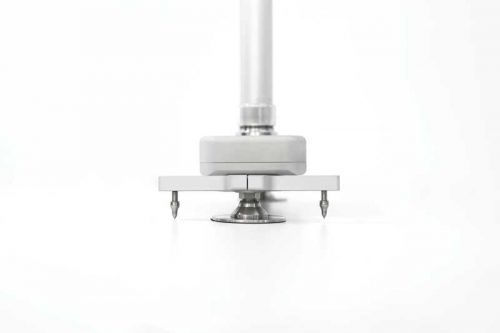
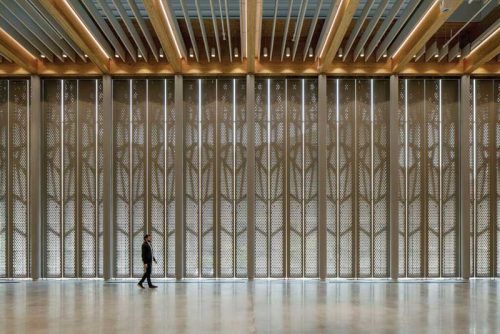
Uncommon ground
The use of two separate and incongruent measurement protocols in Division 03 and Division 09 often necessitates additional work to bridge the gap between them. This work generally results in change orders to grind or fill (lower and raise) elevations to an acceptable and uniform plane that meets the flooring specification requirements. Assigning the “fault” is difficult and unforeseen costs and scope durations escalate as a result.
- “Fault” is the word commonly used during construction when there is a perceived defect in the work, as stated above, the progress of change to the FF/FL is a natural process that needs to be accounted for within the project documents.
- As indicated above, deviation from the measured tolerance on day three until the floor covering is installed eight, nine, or 12 months later is a natural part of aging concrete, meaning that pointing to an at “fault” trade is inappropriate and unjustifiable unless there were specific defects identified during the ASTM E 1155 measurements.
- “Correction” is a better word and can be used to describe the grinding and filling operations typically required to address requirements for straight edge tolerances required by floor covering manufacturers in the form of a cash allowance as recommended by the American Concrete Institute (ACI) and American Society of Concrete Contractors (ASCC) for more than 20 years.
- Correction of concrete services form a part of Division 03 scope of deliverables and are described by most concrete finishing training and apprenticeship programs, and do not form a part of the traditional deliverables forming Division 09.
- Division 09 is only responsible for minimal skim coating, average roughness (Ra), or concrete surface profile (CSP) range, and light abrasion to create a surface that will be compatible with floor covering adhesives and to minimize telegraphing of surface irregularities through resilient materials that will show on the final surface finish.
- Most corrections typically require minimal correction, usually in the range of a few millimeters or 1.5 mm (0.0625 in.), which can be achieved by bump grinding or planning, and minimal filling. Finishing aids incorporating colloidal silica or nano modified cements (NMC) can help fill voids and surface imperfections during the refinishing process without the potential for bond inhibiting side effects often from silicate or membrane forming curing compounds or surface treatments.
- Floors at the higher range of deviation may require installation of self-leveling underlayments or other topping materials.
The current method used by architects, engineers, and specifiers for specifying concrete placement to higher FF/FL values to account for natural changes to smoothness and evenness is misguided, since the statistical nature of the ASTM E1155 measurement procedure results in greater deviation when higher values are specified. A concrete surface specified to FF50/FL35 will decrease in uniformity to a greater percent difference than a floor specified to FF25/FL20, which is considered as standard achievable concrete finishing without using special installation techniques.
While it is possible to improve concrete FF stability through design, curing improvement, and laser screeding, secondary FF testing timing would be required closer to the time of floor placement to assess deviation over time. The measurement at threshold (within 72 hours of concrete placement) and again via local FF testing (within seven to 14 days of flooring installation) would identify variability over time and allow for future design alterations based on stability performance. However, as long as the FF is measured in Division 03 at the time of placement and the straight edge method is employed at the time of floor covering installation, the industry will continue to search in the dark for solutions. Decades have proven it is difficult to solve for X when speaking in two incompatible languages.
Conclusion
Concrete floors, found in a myriad of structures with varying performance requirements, epitomize a realm where meticulous design and craftsmanship intersect. Conducting this symphony of elements, the concrete mix, the often-overlooked curing process, and the precision of finishing orchestrate the creation of not just floors, but functional canvases. Yet, in this complex dance, FF and FL, harmonizing performance and esthetics provide something to hold on to. In a world laden with benchmarks and blurred responsibilities, these factors become the silent architects of quality and contingency protections. FF, ensuring the smooth operation of machinery, and FL, dictating stability and fluidity, demand a choreography of planning and execution.
Picture a canvas: the base is level, the mix design a carefully chosen palette, and the curing process an artful stroke. This, coupled with meticulous control in placement and finishing, forms the symphony. However, the challenge lies in the discord between measurement methods. Until a unified language emerges, the pursuit of overcoming these challenges continues—a quest for simplicity in the intricate work of concrete construction.
Authors
Chris Bennett, iSCS, CDT, is the founder of Bennett Build, an industry-recognized leader in concrete consulting and owner representation. His portfolio includes the longest history of helping project teams in commercial internal curing in North America. Bennett has also helped improve continuing education in concrete by facilitating such programs as The National Concrete and Corrosion Symposium (NCCS), Concrete North, and various hands-on reality labs with institutions such as University of Alberta, the University of Akron NCERCAMP, the Construction Specifications Institute (CSI), and the International Society for Construction Sciences. His work has been featured at Dreamforce, Construct, Praxis!, World of Concrete, and more. He can be reached at chris@bennettbuild.us.
James Longo, iSCS, is the principle of Specified Surfaces, a U.S. based specialty distributor in the flooring and concrete industry. With more than 30 years industry experience spanning installation, manufacturing, consulting, distribution and sales, Longo brings a 360-degree view of the challenges and solutions to delivering consistent, warranted flooring installation systems. Specified Surfaces works directly with professional flooring contractors, owners, A/D teams, and general contractors in the U.S. and Canada. He can be reached at jlongo@specifiedsurfaces.com.
Keith Robinson, RSW, FCSC, FCSI, is a retired architectural technologist and specifier based in Edmonton, Alta. Robinson also instructs courses for the University of Alberta, acts as an advisor to several construction groups, and sits on many standards review committees for ASTM and the National Fire Protection Association (NFPA), and the A21–Best Practices for Measuring Substrate Flatness for Floor Covering Installations. He can be reached at krobinson@dialogdesign.ca.