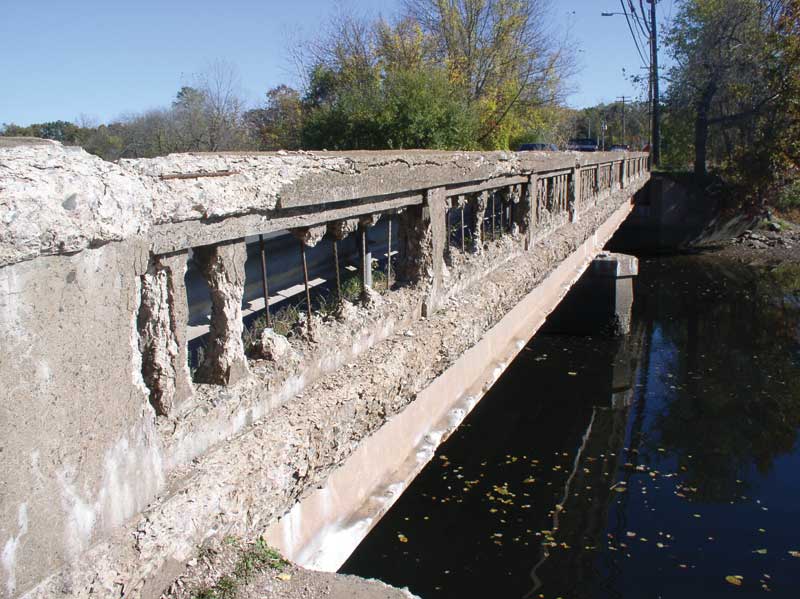
All images courtesy Hoffmann Architects
by Steven J. Susca, PE
Shrinking, creeping, cracking—they sound like things that happen in a grade-B horror flick, yet hit the nail on the head when describing problems with concrete.
Concrete’s versatility, durability, and economy have made it the world’s most highly used construction material. It is crush- and fire-resistant, while providing insulation against sound and heat. The material is also durable, and long-lasting, even in extreme temperatures. Americans pour about 260 million m3 (340 million cy) of ready-mixed concrete each year. It is used in highways, streets, parking lots and garages, bridges, buildings, dams, homes, floors, stairways, sidewalks, driveways, countertops, and even artwork.
Not only is concrete ubiquitous, it has a long history. In ancient times, the Assyrians and Babylonians employed clay as a bonding substance; Egyptians used lime and gypsum. Modern concrete came into play in 1756 when British engineer John Smeaton added pebbles as a coarse aggregate, mixing powdered brick into the cement. In 1824, England’s Joseph Aspdin invented Portland cement, which became the dominant cement used in concrete production. (Many people incorrectly use the words ‘cement’ and ‘concrete’ interchangeably. It is critical to understand the difference between the two. Think about comparing flour to a chocolate chip cookie; the flour is simply one ingredient used to bake a cookie. Similarly, cement is only one component of concrete; when mixed with water it forms a paste in a process called hydration. This paste coats the surfaces of the fine aggregate [sand] and coarse aggregate [gravel or crushed stone], binding them together and forming concrete.)
It has been said concrete is one of the world’s most important materials. There is certainly no denying it is one of the simplest—a mixture of cement, sand, gravel, and water. Typically, concrete comprises 60 to 70 percent sand and gravel or crushed stone, 15 to 20 percent water, and 10 to 15 percent cement by volume. Additionally, admixtures can also be added to concrete to improve on certain requirements of the specific mixture.
Nothing lasts forever, and concrete is no exception. There are many internal and external forces leading to deterioration and premature failure of cured concrete. Some common causes of concrete failure can include water infiltration, carbonation, corrosion of reinforcing steel, shrinkage, drying, thermal contraction, inadequate design, and poor placement practices.
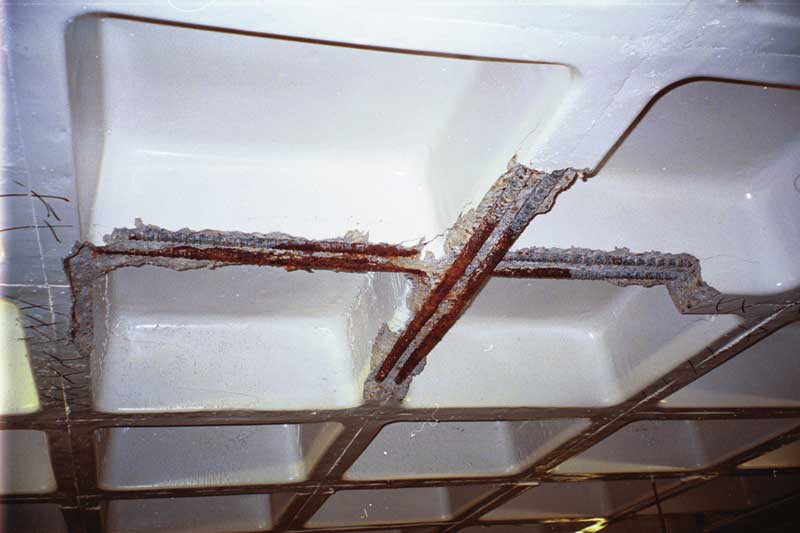
Water—friend and foe
Although water is a necessary component of concrete, it is possible to have too much of a good thing. Either directly or indirectly, water is one of the leading causes of concrete deterioration. While the combination of water and favorable temperatures can generally help increase the strength of concrete throughout its life cycle, it can also prove fatal, serving as a mechanism for deterioration.
Porous, water-saturated concrete without adequate strength and entrained air is prone to scaling—a form of deterioration caused by freezing of water in concrete. Water expands as it freezes, which can impart great internal pressure into concrete. Over time, as these freeze-thaw cycles continue, the concrete eventually weakens and fails. This type of deterioration is easy to recognize—concrete subjected to freeze-thaw damage has the appearance of being pulverized or crushed.
Water can carry into the concrete aggressive chemicals such as acids, sulfates, or chlorides that then cause corrosion of reinforcing steel. Concrete containing alkali-reactive aggregates—discussed later in this article—is also subject to subtle and harmful expansion forces caused by a reaction between the aggregate and the alkali hydroxides, formed during the hydration process. High moisture content within the concrete while in service facilitates this reaction.