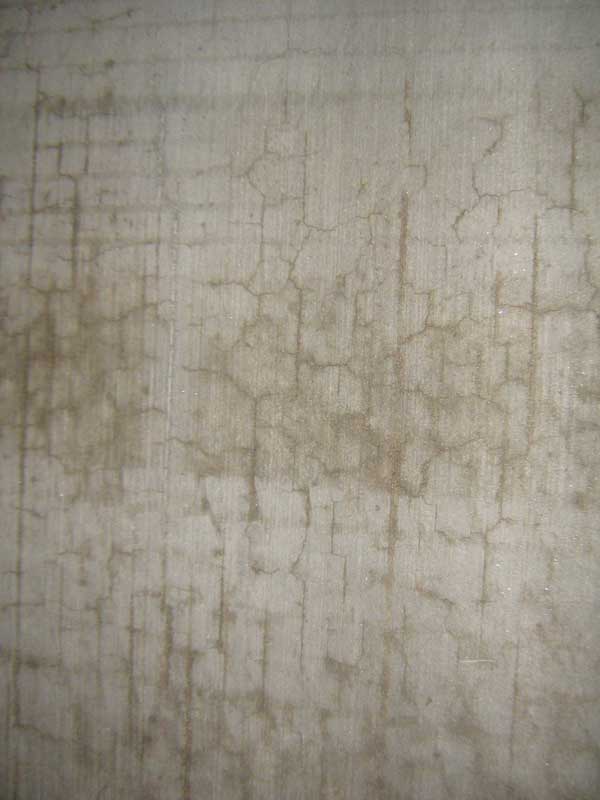
Carbonation
Hardened concrete is a highly alkaline substance, typically with a pH above 12.5. This environment is created by high levels of calcium hydroxide in the concrete and helps protect embedded steel from corrosive forces. Essentially, a passivating film is created around embedded steel reinforcement. Since steel corrosion needs a neutral or acidic environment to flourish, the steel is effectively protected from corrosive forces.
Rainwater combines with carbon dioxide in the air to form carbonic acid. Over time, this carbonic acid infiltrates the concrete and, through a process called carbonation, combines with the calcium hydroxide to create calcium carbonate. This calcium carbonate has the effect of lowering the pH of the concrete, thereby eliminating the protective passivating layer around the steel. While carbonation itself is not a significant cause of corrosion, it allows a corrosive environment to develop at the surface of the steel. It does not take much to encourage corrosion—simply introducing moisture and air and a sprinkling of chlorides from road salts can do the trick.
In situations where concrete has deteriorated, carbonation is one of the usual culprits. Chemical analysis of damaged concrete helps measure the severity of the carbonation issue. One way to help combat the effects of carbonation and slow its progress is to apply water repellant to the concrete surface. In more severe situations, an elastomeric waterproofing coating can be applied. These precautions, preferably taken before the deterioration has occurred, limit future carbonation by restricting the entry of carbonic acid into the concrete.
Corrosion
Corrosion of embedded steel items is both a cause and a symptom of deterioration in concrete. Several different mechanisms can work alone or together to cause steel corrosion. However, for steel corrosion to occur, three ingredients must be present: moisture, oxygen, and an electrolyte. Since moisture and oxygen are found nearly everywhere, the only thing missing is an electrolyte. This can come in the form of de-icing salts entering the concrete through water infiltration.
As steel corrodes, iron oxide is formed. This rust occupies a much greater amount of space than the steel from which it was created. When embedded in concrete, corroding steel imparts great internal pressure into the cement matrix. This eventually results in the formation of a subsurface crack. As the crack grows, it reaches the surface of the concrete and creates a spall.
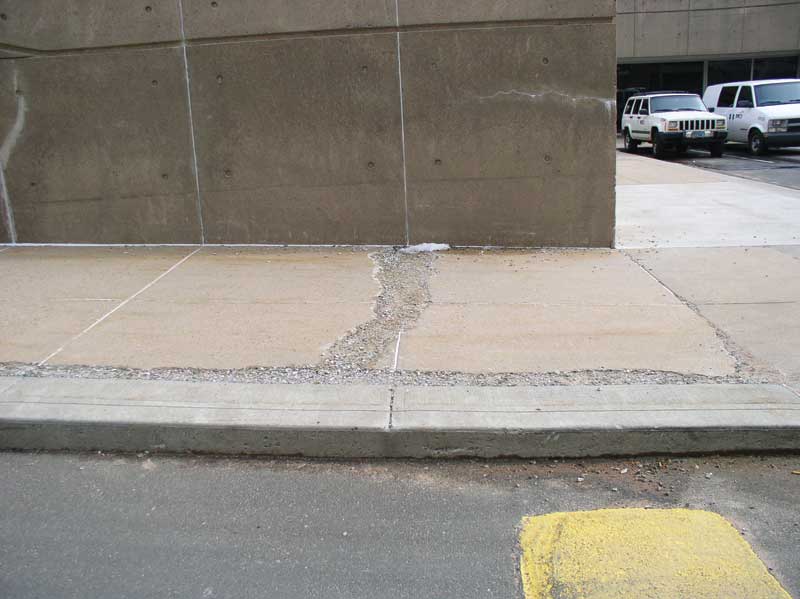
The result of the spalled concrete is a reduction in the protective cover over the rebar. This allows corrosive elements like moisture and oxygen to easily infiltrate the concrete to the depth of the reinforcement, further exacerbating the ongoing corrosion. As this occurs, the cycle repeats itself at a continually increasing rate. In addition to the damage imparted to the concrete, this cumulative process eventually reduces the effective cross-sectional area of the reinforcing steel, ultimately, compromising the structural integrity of the concrete member.
Corrosion of embedded reinforcing steel is a serious issue that needs to be addressed in a timely manner to avoid costly repairs in the future. If not caught quickly, corrosion results in irreparable damage to the concrete. Early detection can mean relatively easy repairs.
Cracking
All concrete crack eventually, but problems arise only when it cracks unexpectedly and in unanticipated locations. Cracking can be the result of one or a combination of factors, such as drying, shrinkage, thermal contraction, poor placement, restraint (external or internal) to shortening, subgrade settlement, and applied loads. Problems with cracking can be significantly reduced by examining the causes and taking preventative steps.
Crazing
Crazing is a pattern of fine cracks that do not penetrate much below the surface and generally pose only a cosmetic problem. They are barely visible, except when the concrete is drying after the surface has been wet.
Plastic shrinkage cracking
A result of improper curing, plastic shrinkage cracking occurs when water evaporates from the surface of freshly placed concrete faster than it is replaced by bleed water (i.e. excess water in the mix that works its way to the surface during the initial stages of curing), causing the surface concrete to shrink. Due to the restraint provided by the concrete below the drying surface layer, tensile stresses develop in the hardening concrete, resulting in shallow cracks of varying depth. Usually appearing within two days of placement, this type of cracking is often fairly wide at the surface.