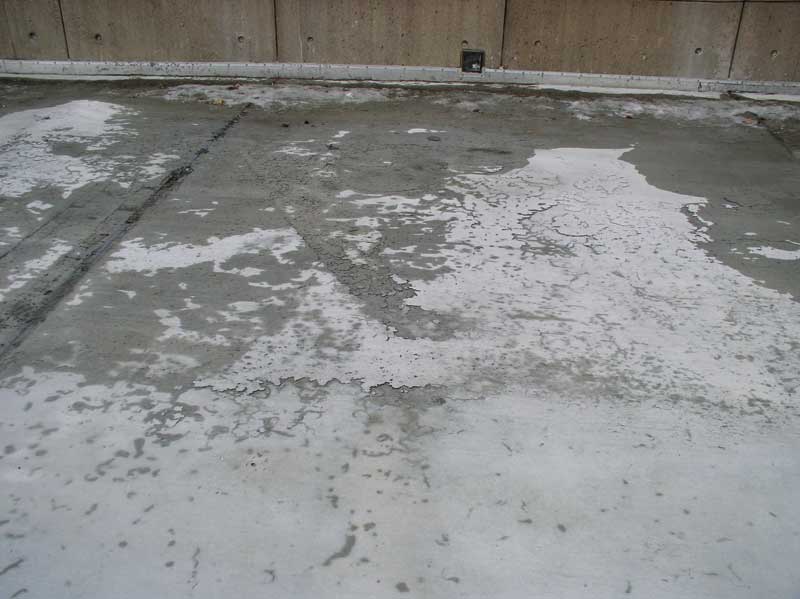
Drying shrinkage
Drying shrinkage is a common issue in concrete. As almost all concrete is mixed with more water than needed to hydrate the cement, much of the remaining water evaporates, causing the concrete to shrink. Restraint to shrinkage, provided by the subgrade, reinforcement, or another part of the structure, causes tensile stresses to develop in the cured concrete. In many applications, drying shrinkage cracking is inevitable. Therefore, contraction (control) joints are placed in concrete to predetermine the site of drying shrinkage cracks.
D-cracking
A form of freeze-thaw deterioration, D-cracking is observed in some pavements after three or more years of service. Due to the natural accumulation of water in the base and sub-base of pavements, the aggregate may eventually become saturated. Then with freezing and thawing cycles, cracking of the concrete starts in the saturated aggregate at the bottom of the slab and progresses upward until it reaches the wearing surface. D-cracking usually starts near pavement joints.
Thermal cracks
Thermal cracks are formed when the heat of hydration of cementitious materials leads to rising temperatures. Thermal cracks are commonly found in mass concrete placements, such as deep footings or bridge abutments, as opposed to thin slabs or beams. As the interior concrete increases in temperature and expands, the surface concrete may be cooling and contracting. This causes tensile stresses, resulting in surface thermal cracks if the temperature differential between the surface and center is too great. The width and depth of cracks depend on the temperature differential, physical properties of the concrete, and configuration of the reinforcing steel.
Loss of support beneath concrete structures
Settling or washout of soils and sub-base materials can cause various problems in concrete structures—from cracking and performance problems to structural failure. Loss of support can also occur during construction due to inadequate formwork support or premature removal of forms or shores.
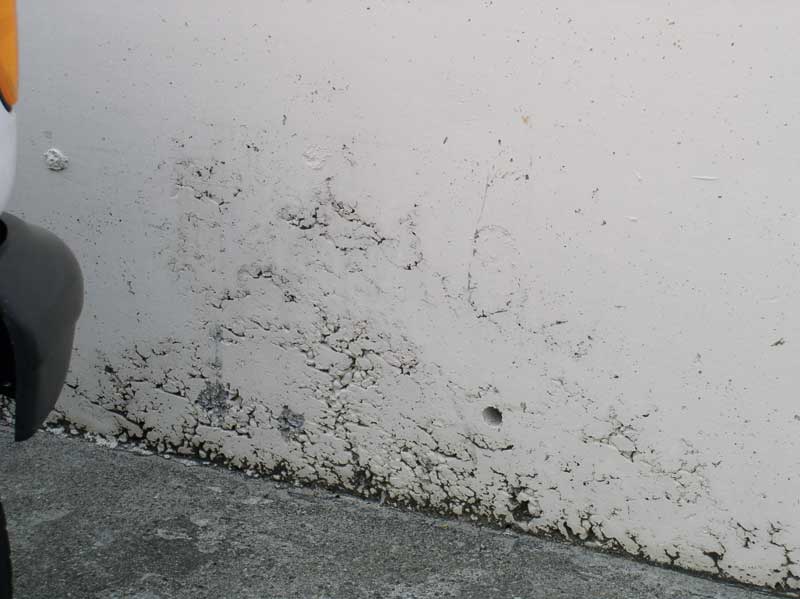
Alkali-aggregate reaction
This type of reaction occurs when the active minerals in some aggregates react with the alkali hydroxides in the concrete. Cracks are characterized by crazing—fine cracks forming a pattern similar to an alligator skin. These cracks allow more moisture to enter the concrete, further exacerbating the situation. Alkali-aggregate reactivity occurs in two forms: alkali-silica reaction (ASR) and alkali-carbonate reaction (ACR).
ASR occurs when certain siliceous aggregates react with the alkali hydroxides to form a silica gel. In turn, this absorbs water and expands, imparting great pressures within the concrete, eventually causing cracks. ACR is a result of a reaction between alkali hydroxides and carbonate rock particles.
Alkali aggregate reaction is very difficult to stop once it has begun. The best way to guard against this failure is to ensure non-reactive aggregates are used.
An ounce of prevention
Concrete failure can be kept at bay by taking proper precautions during the construction phase. If the concrete is correctly placed, consolidated, finished, and cured, it has a good start to a prolonged life and delayed deterioration.
One must always select the proper materials for the concrete mix as well as ensure the coarse aggregate is properly sized for the particular application. A chemical analysis should be performed to ensure it is not alkali-reactive. Water for the mix should be potable and free of any chlorides or other deleterious chemicals.
When it is time to mix the concrete, one must use the lowest amount of mix water needed for workability because overly wet consistencies can reduce concrete’s strength and durability. To minimize the amount of mix water, the largest size aggregate suitable for the project must be employed. Water-reducing agents (WRAs), or superplasticizers, can be added to the mix to help increase the workability of fresh concrete without adding water.
The most important aspect of a concrete mix design is the water-to-cement ratio. This is defined as the ratio between the total weight of water in the mix and the total weight of cement. This ratio determines the overall quality of the concrete mixture and to a great extent, its strength. Generally speaking, a lower water-to-cement (w/c) ratio will result in higher quality concrete. However, one must not sacrifice the workability (i.e. the ability to pour, place, and finish) of the fresh concrete by making it too dry.
When casting concrete against the earth, it is extremely important to properly prepare and compact the subgrade. Choosing the proper sub-base material helps provide uniform support to the slab, reducing the chance of settlement cracks.