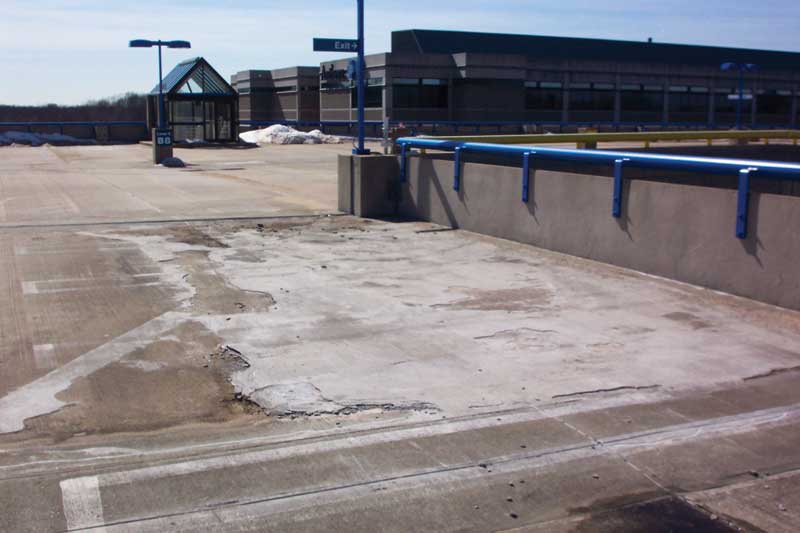
Spray-applied finishing aids or plastic sheets can be employed as vapor retarders to avoid rapid loss of surface moisture, aid in curing, and prevent plastic-shrinkage cracks and curling of the slab edges. Finishing operations should not begin until the water sheen on the surface is gone and excess bleed water has evaporated. Application of additional ‘finishing water’ must be avoided at all costs. If any excess water is worked into the concrete during finishing operations, the concrete paste at the surface will contain too much water, which will likely result in scaling.
In concrete slabs, walls, and other large members, it helps to provide contraction or control joints at reasonable intervals. When the concrete cracks, it will do so in a predetermined location, rather than randomly throughout the member. The American Concrete Institute (ACI) has published guidelines on the placement of such joints in these members.
Precautions must be taken when casting concrete in very high or low temperatures. In areas with freezing temperatures, air-entraining admixtures should be added to the mix to improve freeze-thaw resistance. Some of the mix water can be replaced by ice (on a by-weight basis) to extend the working time of the mix in hot weather. Extreme temperature changes must be avoided during the curing process.
Once the concrete is in place, it is important to ensure it is cured properly. Curing is the process of maintaining a good balance of temperature and humidity around fresh concrete for a specific amount of time, so the concrete can achieve proper strength and durability.
As concrete cures, it gains strength. The initial curing period generally lasts from seven to 28 days and is when the concrete attains most of its strength. However, the actual hardening process continues for years, albeit at a much slower rate, allowing the concrete to get stronger as it gets older.
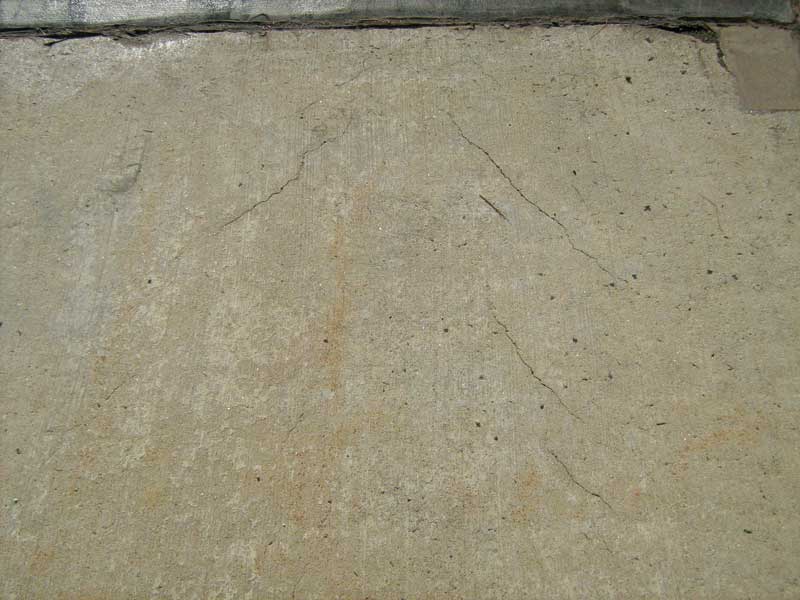
Keeping on top of things
Once the concrete is in place, there are ways to ensure it remains functional and intact for many years. To help extend the life of concrete, it is important to maintain it and keep a watchful eye for issues that might arise. Regular inspections can reveal problems still in the manageable and affordable repair stages.
Control, reduce, or prevent cracking
As noted, all concrete eventually cracks. The installation of control joints at regular intervals will cause this to occur in predetermined locations, thereby minimizing unanticipated cracking. When cracks are discovered, an analysis should be done to determine the cause prior to making any repairs. The crack can then be sealed from moisture infiltration or injected with grout or epoxy. It is important, prior to repairs, to first determine the cause of the cracking and if ongoing expansion of the cracking exists.
Prevent corrosion
When placing new concrete in locations that might experience a high rate of corrosion, such as parking garages, several methods can be used. Options include:
- placing sacrificial anodes within the concrete formwork and bonding them electrically to embedded steel items to provide a form of passive cathodic protection;
- employing epoxy-coated or galvanized rebar instead of regular rebar as an additional safeguard;
- including corrosion protection admixtures in the concrete mix;
- applying a migrating corrosion inhibitor to the surface of cured concrete to help protect embedded reinforcement; or
- applying a waterproof traffic-bearing membrane to the surface in areas where deicing salts are used. This, however, would require regular maintenance. This work should be included as part of a regular maintenance budget.