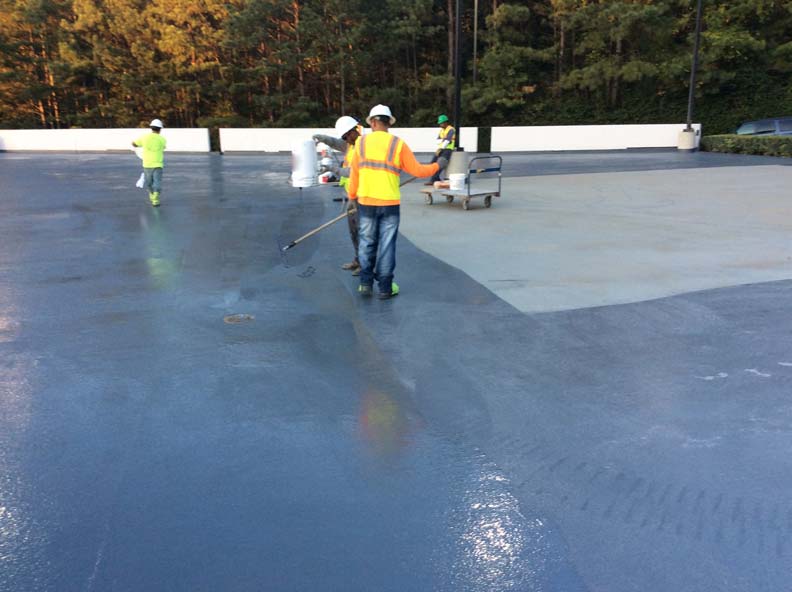
Photo courtesy Western Specialty Contractors
Applying a clear penetrating sealer and urethane sealant are just two of the steps that went into restoring Nalley Ford’s three-level concrete parking garage.
Based in Sandy Springs, Georgia, the dealership’s garage required repair, restoration, and protection of its surfaces—each of the levels with their own specific damage.
Exposed to the elements, the garage’s top level required cleaning using a high-pressure 20,684-kPA (3000-psi) water-blaster. Once the pressure washing was complete, crews saturated the concrete surfaces with a clear penetrating sealer. Next, they routed and sealed approximately 1700 m (5580 ft) of existing cracks and control joints using a urethane sealant. Additionally, workers removed 97 m (318 ft) of existing sealant around the perimeter joint, then lightly grinded the joint edges to remove any loose residual sealant. A new urethane sealant was then applied. To allow for expansion/contraction of the concrete intersections, 121 m2 (1300 sf) of new pour strips were installed.
At the exterior wall joints, approximately 168 m (550 ft) of existing sealant was removed, ground down, and replaced with a new urethane sealant. Workers also removed oxidation at the exterior wall weld plates, and applied an epoxy chromate primer and urethane topcoat. To complete the top-level restoration, crews applied two coats of elastomeric coating to approximately 758 m2 (8160 sf) of wall substrate, as well as a traffic-deck coating system.
On the intermediate level, all concrete surfaces were cleaned using a high-pressure water-blaster, before approximately 1700 m (5580 ft) of existing cracks and control joints were routed and sealed with a urethane sealant.
Crews also removed about 164 m (540 ft) of existing sealant around the perimeter joints and replaced it with a urethane sealant. Oxidation on corbal bearing plates and double-tee bearing plates was removed and refinished with an alphatic urethane top coat. The precast wall perimeter was also resealed and repairs were made to damaged columns, which were resealed with two coats of an anti-corrosion bond inhibitor. Workers saw-cut and chipped out damaged concrete on the slab floor and replaced it with new concrete.
The parking garage’s lower level also required restoration and repair. Specifically, crews removed oxidation on the gusseted steel corbels, spanning plates, and double-tee bearing plates; they then applied an alphatic urethane topcoat. Next, the crew removed deteriorated concrete around the beams, replacing damaged steel and patching the beams with new concrete.
On areas where steel web was showing as a result of deteriorating concrete, the surrounding concrete was removed, the damaged steel was replaced, and the area patched with new concrete.