by Aali R. Alizadeh, PhD, P.Eng.
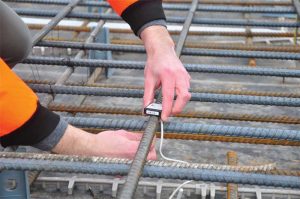
Testing concrete’s strength is essential, but is also messy and expensive. One needs to create test cylinders, cure them properly, transport them to the lab for more curing (or field cure them), and then break them in a compression machine just to throw the broken concrete into a dumpster. Though it seems like a waste of time and resources, it is necessary to know concrete’s early age-strength for construction operations or the mix’s long-term strength to ensure the specified concrete strength is achieved.
So, one makes the cylinders and waits several days before breaking the first set only to get a strength value at a single point in time. That value does not necessarily indicate the actual in-place strength of the concrete, even if it was field cured, but is rather an idealized value of what the given mix can achieve under ideal conditions. There are a limited number of cylinders so a new data point cannot be generated every day. Construction then waits for a strength value that allows the contractor to move forward with stripping the forms, tensioning post-tensioning cables, or opening the work to traffic.
However, is this testing process necessary? The concrete producer has already developed the mix to meet the specified strength, made and tested his/her own cylinders, and sent in the submittals. If the concrete delivered is the same then the chances are extremely high the mix will achieve the specified long-term strength in the structure. When cylinder breaks point to low strength, the most likely cause is usually mishandling of the equipment in the field or in the lab.
The process seems antiquated. Luckily, another way called concrete maturity can indicate the strength in real time, and in the structure.
Maturity matures
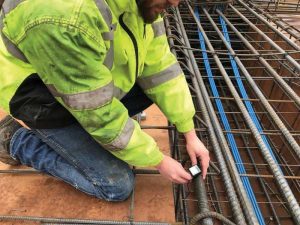
The original research that lead to the concept of concrete maturity dates back to the 1940s. Two significant construction failures in the 1970s pointed to an urgent need to be able to estimate the in-place concrete strength during construction. In 1973, a failure traced to early removal of formwork led to the death of 14 workers. In 1978, 51 workers were killed during construction of a cooling tower with the cause pinpointed as insufficient concrete strength to fully support the applied construction loads. These disasters led to research by Nick Carino and H.S. Lew at the National Bureau of Standards (NBS) (now the National Institute of Standards and Technology [NIST]), which began to change the theory into something practical that could be used in construction.
Over the years since, maturity has increasingly been used as the best way to estimate the in-place strength of concrete, especially at early ages. Transportation departments use maturity to indicate when pavement can be put back into service. Armed with maturity data, contractors can pinpoint the optimum safe time to remove forms or apply post-tensioning forces, regardless of the curing temperature. Designers utilize maturity and temperature data to assure themselves and their client’s construction is being performed properly, thereby reducing the potential of cracks from overloads and liability from accidents related to unexpectedly low strength.
How it works
Concrete’s maturity is the extent of the cement’s hydration. One of the methods used to calculate the maturity index of concrete is to determine the area that is under the time-temperature curve—the differential of the curve where the X-axis is at 0 C (32 F), the commonly used datum temperature. The value of the maturity index correlates directly with the concrete strength regardless of how long it takes to get there. So a warm concrete will reach a given maturity index (strength) sooner than a cooler concrete, since the rate of the concrete hydration reaction approximately doubles with each 11 C (20 F) temperature change. With maturity data, it is known, regardless of how long it takes to get to a given maturity index, whether it is six hours or six days, it will have the same strength.
In practice, this means a correlation must be developed between the maturity index and the concrete’s compressive strength. Unfortunately, the maturity curve is a little different for each mix. Things such as cement source, aggregate type, and water-cement (w/c) ratio changes from one load to another can result in maturity strength variations among mixes of as much as plus or minus 15 percent. Therefore, a maturity calibration needs to be produced for each mix design and validated over time. This is accomplished according to the provisions of ASTM C1074, Standard Practice for Estimating Concrete Strength by the Maturity Method.
To develop calibration data for a given mix, the concrete producer makes a minimum of 17 cylinders (under standard curing conditions). Two of them will be used for temperature monitoring by embedding a sensor, and the others will be employed for compressive strength breaks. A minimum of five break times (e.g. one, three, seven, 14, and 28 days) are selected. At the appropriate times, two cylinders are tested to determine the compressive strength. A third cylinder is tested if the results vary more than 10 percent from the average.
At the time of the break, the maturity index is determined from the two cylinders used for temperature monitoring. This provides five data points with a compressive strength associated with the maturity value. Plotting those data points result in a calibration curve for the specific concrete mix. The producer will then validate the curve by making a couple of additional cylinders on its next pour, and comparing the calculated strength obtained from maturity with the cylinder strength determined in the lab.
The maturity can also be used to estimate the long-term strength of concrete, although a slightly different model, called the equivalent age method, is more accurate for it.