In the field
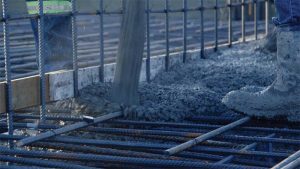
Contractors use sensors to monitor the in-place temperature of the concrete in their structures for a variety of reasons. In cold weather, they need to be careful to not freeze exposed corners of the concrete. With mass concrete, a temperature differential is specified between the center of the member and the nearest exterior surface to prevent thermal cracking.
When maturity is being used to determine the in-place concrete strength, temperature should be monitored at critical locations. Typically this would be the center of the cross section of a structural element, which would be the location of the highest moment. For larger pours, the temperature sensors are placed in the area of the last pour since it will have the lowest strength, especially at early ages. In cold weather, sensors are placed in the area most exposed to colder ambient temperatures, such as the corners of a concrete floor. When these locations have achieved the required maturity (i.e. strength), forms can be safely removed or post-tensioning cables can be stressed.
Temperature sensors (typically thermocouples) for maturity determination have been, and still are, embedded into concrete with a wire protruding to the surface or inserted into the concrete through an embedded plastic sleeve. A technician then goes around on a set schedule with a data logger and connects to each of the sensors and records the time, location, and temperature. This means, the concrete workers must be careful with the sensors and the wire when placing concrete to make sure it does not get buried in the mix or gets cut off. The technician then downloads or transfers the data to a computer for analysis.
Recently, new wireless sensors have come to the market. An expendable wireless sensor is attached to reinforcing steel and is completely embedded during concrete placement. Installation is much simpler with no protruding wires. Data is collected via Bluetooth on a mobile phone or tablet, eliminating the need for a data logger (it is built into the sensor). The data collected by the sensors is updated every 15 minutes and uploaded to an app. This data, as well as the measurements provided during mix calibration is used to determine the maturity/strength of the concrete in real-time—no additional calculations are needed. Since the data is on a smart phone, it can be easily shared with team members, helping them make decisions on the go.
Specifying maturity
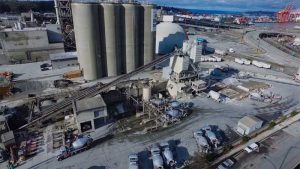
Section 6.2, “Removal of forms, shores, and reshoring,” of the American Concrete Institute (ACI) 318, Building Code Requirements for Structural Concrete, deals with the removal of forms, shores, and reshoring. It requires forms to be removed “in such a manner as not to impair safety and serviceability of the structure.” This section further requires the contractor to develop a procedure for form and shore removal, and to provide the engineer and building official with concrete strength data. It also allows the data to be based on field-cured cylinders “or, when approved by the building official, on other procedures to evaluate concrete strength.” One of the permissible methods to accomplish this, as indicated in the commentary, is “maturity index measurements and correlation in accordance with ASTM C1074.”
Field-cured cylinders, though, are notoriously difficult to cure in such a way as to reflect the actual in-place strength of concrete. Curing boxes must be heated or refrigerated to mimic ambient conditions until the testing takes place at the laboratory. For those reasons, many engineers today are specifying the use of maturity temperature sensors to replace or reduce cylinders for early-age strength estimates. A model specification language for wireless sensors is as follows:
The sensor data must be downloadable in real time and wirelessly using mobile apps. Contractor is to provide Engineer direct, real-time access usable on devices with an Internet connection for all measuring results prior to the beginning of measuring proceedings.
Contractor shall provide quality reports, including sensor measurement results, for compressive strength and concrete temperature on a weekly basis (if not agreed upon differently prior to project start). The quality reports must include graphic format for temperature history (from start of pour till end of measurement) and nonstop compressive strength evolution.
The sensors can replace test cylinders for early age concrete (one to seven days) and can be used to define the correct timing for stripping formwork, pre- and post-tensioning operations, and applying load to the concrete structure. The contractor shall produce and test cylinders for 28-day compressive strength as specified herein and as per the applicable standards.