Case studies
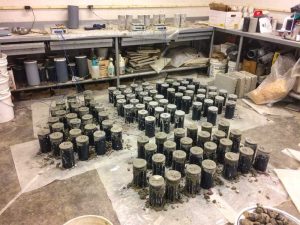
PCL, a North American general contractor (GC), has successfully embraced innovation.
“We are always looking at new methods that will save us time, and our clients’ money, on projects while differentiating ourselves from other contractors,” says April Smith, PCL field coordinator.
During construction of a 55-story building in Edmonton, Alberta, one operation in need of a new approach was concrete testing. Smith noted that by the time one gets lab results from the first cylinder break, they could have already met strength without knowing it.
“You still need to wait another three hours or more before getting lab confirmation,” she says. “Although that might not sound like much, saving three hours on every cycle of a 55-story building adds up quickly.”
The GC was faced with an aggressive schedule that needed the crews to work on weekends. Using traditional techniques to determine the in-place concrete strength would have required field-cured cylinders to be made and cured under conditions as close as possible to the in-place concrete—which can be difficult. Afterwards, the cylinders would be taken to the laboratory and broken to determine the concrete strength—if the testing lab personnel are working on the weekend.
Smith looked at several technologies and decided on a nondestructive wireless maturity system that gave multiple team members access to a continuous flow of information.
Using maturity testing, the GC was able to know the in-place concrete strength directly at all times and could then strip the forms and move forward with construction on the next floor level as soon as strength was attained. This also cut out their dependency on the testing lab to get personnel to the jobsite and take cylinders to the lab and then report back with the results.
“If a job is poured on Friday, my foreman looks at the screen on Saturday morning, and sends me a text message to say the strength is good and we can strip the formwork,” said Shawn Kitt, PCL superintendent. “We have eliminated the need to coordinate with three people to get the information needed; you get results instantly, and it saves so much time.”
Kitt also points out that results can be checked anytime at no cost and there is no destruction of materials.
“For me personally,” Kitt said, “the next project I go to, whether it is a bridge, a low-rise construction, or a high-rise building, if I am pouring concrete, I am going to seriously think about using this technology rather than field cures because I have seen the advantages first hand.”
An unusual application of maturity testing was recently used on a bridge project in Alexandria, Louisiana, by Gilchrist Construction.
Although bridge work started in March 2017, they were able to open it to traffic by October of the same year, “[which is] an extremely fast time to build a bridge and open it to traffic,” said Frank Maury, project manager.
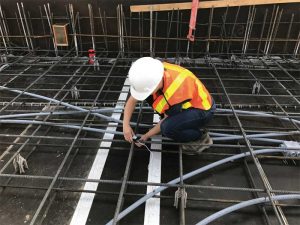
Gilchrist was required to pour very wide bridge deck sections within four hours to assure no cold joints would form. In some cases though, they exceeded the four-hour window. Using maturity testing, they were able to prove strength had not yet developed and the deck section was still a monopour.
A ready-mixed concrete producer in Seattle, Washington, has taken the maturity method to the next level. They started using the method in 2000 for commercial projects. The wireless method, with being able to get the data in an app or on a phone, reinvigorated the market for the younger generation of workers. They workers found it provides more transparent and quicker reporting. Customers also like it.
The company has maturity curves on 82 different mixes. This allows them to avoid creating new maturity calibrations on their mixes. They established the curve on the job and then took cylinders and put some of them in a curing box at 32 C (90 F) and some in a refrigerator at 4 C (40 F) and broke them. Both sets fit the curve.
Minimizing cylinders
Maturity methods provide many advantages for early age concrete strength estimates. This is especially true with wireless sensors and when specific concrete mixes have been calibrated in advance. Research is currently taking place on the use of maturity methods for long-term strength estimates with the hope that maturity will be used. Some physical concrete testing will always be necessary for verification and calibration but eventually one should be able to greatly reduce the use of concrete test cylinders for purposes of strength determination.
Aali R. Alizadeh, PhD, P.Eng., is the chief product officer at Giatec and an adjunct professor at the University of Ottawa, Canada. He received his PhD in civil engineering in 2009 from the same university. His research on concrete materials science and cement nanotechnology resulted in more than 70 journal and conference publications, and was awarded the Governor General’s Academic Gold Medal. He co-founded Giatec in 2010 with the vision to revolutionize the construction industry. With exports to more than 70 countries, Giatec is a leading player in smart concrete testing technologies, nondestructive (NDT) tools, and construction-related Internet of Thing (IoT) solutions. Alizadeh serves on various committees of the American Concrete Institute (ACI), ASTM, and the Canadian Standards Association (CSA). He is also a recipient of Ottawa’s 2017 Forty Under 40 Award. Alizadeh can be reached via e-mail at aali@giatec.ca.