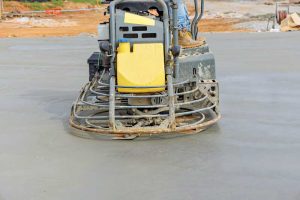
However, ASTM C1315 also states, “adhesives for other systems shall be of a type recommended for the installation of materials of interest over concrete.” Today, almost every flooring adhesive has added very specific instructions for application to a porous or non-porous substrate surface. Since 2021, ASTM F710, Standard Practice for Preparing Concrete Floors to Receive Resilient Flooring, requires all concrete slab substrate surfaces be tested for porosity, either following the manufacturer’s written instructions, or in the absence thereof, ASTM F3191, Standard Practice for Field Determination of Substrate Water Absorption (Porosity) for Substrates to Receive Resilient Flooring. An ASTM C1315 cure-and-seal product is going to render a non-porous substrate surface where a slab is finished by power troweling; this should be accounted for by ensuring proper bond tests are specified in the relevant 07 and 09 sections.
Conclusion
Proper curing means suitable temperature and moisture conditions within the freshly placed concrete, and there are a few factors which can damage the concrete more than improper curing. Most curing methods are impractical, too expensive, or too disruptive to other project trades and timelines to be properly carried out on slabs which will receive flooring, roofing, or a coating. The simple and direct “cure” is to specify an ASTM C1315 curing compound and to ensure all bond tests and subsequent installations first test the substrate surface for porosity. If the adhesive is not suitable for a non-porous substrate, there are alternatives which do not require expensive and time-consuming profiling. Knowing the standards, knowing the products, and specifying sustainably is the prescription for properly cured concrete.
Notes
1 Refer to ACI 301, Specifications for Structural Concrete, American Concrete Institute (ACI), Farmington Hills, Michigan.
2 Refer to ACI 305.1, Specification for Hot Weather Concreting, American Concrete Institute (ACI), Farmington Hills, Michigan.
3 Refer to ACI 306.1, Specification for Cold Weather Concreting, American Concrete Institute (ACI), Farmington Hills, Michigan.
4 Read the ACI 308R-16, “Guide to External Curing of Concrete,” American Concrete Institute (ACI), Farmington Hills, Michigan.
5 Refer to ACI 308.1, Specification for Curing Concrete, American Concrete Institute (ACI), Farmington Hills, Michigan.
6 Read the ACI CT-18, “ACI Concrete Terminology,” American Concrete Institute (ACI), Farmington Hills, Michigan.
7 Refer to ASTM C125-19, Standard Terminology Relating to Concrete and Concrete Aggregates.
8 Refer to ASTM C309, Standard Specification for Liquid Membrane-Forming Compounds for Curing Concrete, ASTM International, West Conshohocken, Pennsylvania, 2007.
9 Refer to ASTM C1315, Standard Specification for Liquid Membrane-Forming Compounds Having Special Properties for Curing and Sealing Concrete, ASTM International, West Conshohocken, Pennsylvania, 2007.
10 Refer to ASTM F710-21, Standard Practice for Preparing Concrete Floors to Receive Resilient Flooring, ASTM International, West Conshohocken, Pennsylvania, 2007.
11 Refer to ASTM F3191-16, Standard Practice for Field Determination of Substrate Water Absorption (Porosity) for Substrates to Receive Resilient Flooring, ASTM International, West Conshohocken, Pennsylvania, 2007.
12 Learn more by reading Hukey, John C (2008). “Specifying Conformance with ASTM C1315: What Assurance does it Really Provide?” Concrete International, V. 30, No. 3, Mar., pp. 51–53.
Author
Principal of ISE Logik Industries, manufacturer of concrete moisture products, Dean E. Craft has presented more than a thousand times on how to proactively address concrete moisture in the design phase. He is the principal author and technical chair of ASTM F319–16 Standard Practice for Field Determination of Substrate Water Absorption (Porosity) for Substrates to Receive Resilient Flooring. Craft completed his doctoral work in 2017 with a dissertation entitled, “Fallacy of Current Industry Approach to Assessing Concrete Moisture Before Flooring Installation” and is a participating member of the ASTM Committee D08 on Roofing and Waterproofing, ASTM Committee F06 on Resilient Floor Coverings, American Concrete Institute (ACI), Single Ply Roofing Systems (SPRI), National Ready-Mix Concrete Association Research (NRMCA), and Engineering & Standards Committee (ESC). He is a retired, U.S. Marine Corps Lieutenant Colonel with 23-years of total service; and graduate of the United States Naval Academy (BS), the Naval Postgraduate School (MS), and California Intercontinental University (DBA; Doctorate in Global Leadership).