by Danielle A. DiDomizio and Sean M. O’Brien, PE
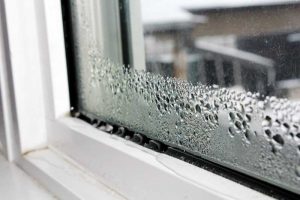
Condensation has confused and frustrated the construction industry for decades. It can occur on visible surfaces or within concealed assemblies, such as wall or roof cavities, and on just about any type of building material.
The issues associated with condensation vary and, if concealed, may go unnoticed until a ‘musty’ smell leads to removal of interior finishes, and the discovery of organic growth, wood decay, and/or corroded metals. Modern fenestration products made of moisture-resistant materials such as aluminum or painted steel may not corrode or decay, but adjacent ones, such as wood trim and paper-faced gypsum wallboard, are susceptible to moisture and will continue to deteriorate if condensation is unaddressed.
Condensation causes
Condensation describes the phase change process by which water vapor turns into a liquid. A given volume of moist air will begin to undergo this process at a temperature known as the dewpoint. The dewpoint is a function of the absolute moisture content of the air, as opposed to relative humidity (RH), which is a result of both moisture content and temperature (i.e. warmer air can hold more moisture than colder air). Thus, a higher dewpoint equates to greater moisture levels regardless of interior temperature. Figure 1 shows this graphically. The sample of moist air at 10 C (50 F) and 50 percent RH (i.e. 50 percent saturation) has a dewpoint of 0 C (32 F). Raising the temperature of the sample increases the amount of moisture it can hold, so the RH goes down even though the dewpoint remains the same for the 21 C (70 F) and 29 C (85 F) samples. This is an important point, as many designers tend to think in terms of RH and do not at all consider the effects of temperature. The dewpoint of a set of temperature/RH conditions can be obtained easily from reference tables (psychrometric charts) or calculated using software, online tools, and mobile applications. The advantage of understanding the dewpoint of a built environment is very simple: In buildings, condensation occurs on surfaces colder than the dewpoint temperature. This provides a clear point of design guidance—susceptible surfaces must be maintained above the dewpoint to remain dry in-service.
Interior moisture sources
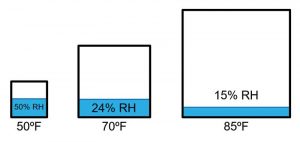
Images courtesy Simpson Gumpertz & Heger, Inc.
The dewpoint in a building depends on a range of factors, some of which are better understood than others. In a typical building, occupant-generated moisture is the primary source of moist air. Respiration, handwashing, and in residential buildings, showering/bathing and cooking, all increase the amount of moisture in the air. The majority of commercial spaces are mechanically ventilated with outside air. This acts to dilute interior moisture levels with drier air from the exterior during cold weather, keeping RH levels fairly low (20 to 25 percent) at code-minimum ventilation rates. The RH in residential buildings is more difficult to predict, as many of these structures (both single- and multi-family) rely on operable windows for natural ventilation, as opposed to fixed mechanical systems. Depending on the airtightness of the building enclosure, the rate of moisture dilution can vary significantly, resulting in a range of interior RH levels. Special-use buildings such as data centers, hospitals, and museums/archives will often maintain specific temperature and RH levels for various purposes, including static discharge control, patient comfort or wellness, and preservation of artwork and artifacts. Buildings housing indoor swimming pools will have a high RH (at elevated temperature) due to the use of the facility. Lastly, many previously non-humidified buildings such as offices and residential spaces are now being humidified for various reasons, including comfort, potential benefits for people with conditions such as asthma, and stability of interior finishes and furnishings. In these cases, the design dewpoint is simple to obtain by discussing interior condition setpoints for both temperature and RH with the project’s mechanical engineer.
Susceptible surfaces
Low-temperature surfaces can occur in buildings for a variety of reasons. As the elements of the building typically made from the highest conductivity materials such as steel and aluminum and have low thermal resistance relative to insulated elements such as walls and roofs, fenestration products typically have the highest potential for condensation. In recognition of this risk, industry organizations such as the American Architectural Manufacturers Association (AAMA) and the National Fenestration Rating Council (NFRC) have developed guidelines and simple rating systems (condensation resistance factor [CRF] and condensation resistance [CR] respectively) for evaluating the relative condensation resistance of these elements. The same is not true for opaque wall assemblies. They are less susceptible due to the higher insulation values and the use of materials with low conductivity. Condensation on opaque wall elements is typically caused by thermal bridging, where a high-conductivity element allows heat flow to bypass a lower-conductivity element such as thermal insulation.
Designing against thermal bridging has become more of an issue in recent years due to the increased stringency of energy codes and regulations. These standards aim to eliminate thermal bridging for the purpose of reducing heat losses/gains through the building enclosure. However, this is still a common problem due to the also-increasing complexity of buildings and demands of designers and owners. Where fenestration meets opaque walls, thermal bridging is of greater concern, as conductive materials (often needed for structural attachment of the assembly) can lead to increased heat losses and reduced overall performance from the system(s). The authors have seen cases where owners have spent extra on high-performance fenestration systems only to have the overall effect reduced to ‘typical’ levels by poor thermal detailing at the perimeters and attachments.
Am building home in norther Ontario, presently framing basement. Exterior walls, roof , etc are done however apart from ICF in basement upstairs not yet insulated.
Outside temperatures are now dipping well below freezing. For the next month or so am I better to have no heat at all in basement as we work or is it ok to maintain a temp just above freezing? Which will minimize condensation until we can fully insulate? Thank you.