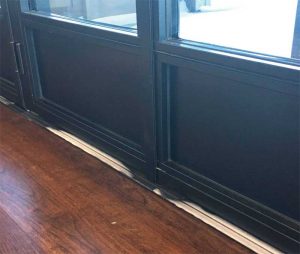
Providing supplemental heat to the fenestration in the form of warm air directed at the system can reduce, or eliminate, interior condensation by increasing local temperatures, heat delivery to the assembly via moving air, and evaporation rates of condensation that may form on the surface (again, due to moving air). Unfortunately, this approach is more appropriate for an initial design due to the difficulty of running new systems within the constraints of an existing building. Other options for supplemental heating include electric resistance heat trace and radiant heating systems. Heat trace, although effective at delivering heat directly to frame components (where it is needed the most), requires new wiring systems and periodic maintenance, although both may still be less expensive than replacing a building enclosure element. From a non-technical standpoint, however, it might be difficult to design heat trace systems capable of meeting electrical or building codes, as few products are specifically designed or certified to function in this application. Radiant heat systems may require significant input of heat to effectively warm all surfaces on the fenestration. Since radiative heat transfer requires the surfaces being heated to be ‘visible’ to the heat source, inverted or partially concealed surfaces may not receive the same level of heat as surfaces with direct line-of-sight to the heater. While similar effects may occur with warm air systems, air will tend to flow around components and can reach some (but not all) surfaces that would otherwise be ‘invisible’ to radiant heat. The space requirements for radiant panels and need for line-of-sight make radiant heating suited to very specific situations only.
If it is determined condensation occurs due to thermal bridging directly through window frame components or the surrounding assembly, replacement or in-situ modifications of these elements may be required. Given the potential cost and difficulty of this type of repair, especially in an existing building, exploring the other options discussed above should always be done as a first step.
Case studies: Too much moisture (on purpose)
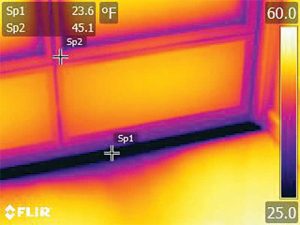
As described above, it is becoming more commonplace for residential buildings, even single-family homes, to be intentionally humidified. In some cases, the decision to humidify is not made as a team, but by only one or two parties. The authors investigated a project in northeastern United States where the disconnect between design team members resulted in significant condensation and a drawn-out legal battle over damages.
In this case, the owner requested humidification based on the amount of fine woodwork and the furniture/artwork in the house, as well as for the potential health benefits. The humidification system was designed by the mechanical engineer and clearly shown on their drawings, but not fully appreciated by the architect. The critical factor in this instance was the selection of non-thermally broken steel windows as the primary fenestration system for the building. Steel windows offer a unique, historical appearance with very narrow frame profiles, often preferred by designers to ‘bulkier’ wood or aluminum frames. However, steel is an excellent conductor of heat, resulting in low interior surface temperatures. In historic buildings, dewpoints were low due to ‘leaky’ enclosures and low interior moisture loads, allowing for these windows to be widely utilized throughout wintry climates with only minimal condensation at the coldest times of the year. In this building, low surface temperatures and high dewpoint (approximately 5 C [41 F] based on conditions of 21 C [70 F]/35 percent RH) resulted in significant condensation and finish damage in the first few winter months the building was occupied (Figure 3). At the project conditions, frame temperatures were often below freezing, resulting in ice accumulation on sills. This led to prolonged damage, as the ice would take longer to melt and dissipate than liquid water on the frame surfaces.
In this case, a simple discussion between the parties, as well as better understanding of the performance of steel windows relative to other systems, could have prevented these problems early in the design process. The authors are unaware of the results of the (ongoing) dispute, but potential remedial options would have included re-routing of ductwork to provide localized heating or, more likely given the severity of the problem, replacement of the windows with thermally efficient systems. In this case, the owner had told the authors reduction of the interior RH was not an option.
In a related case, the authors investigated a similar project several years later. In this building, a large, humidified single-family residence, the architect had specified thermally broken steel window and doors for both CR and energy efficiency. However, during the shop drawing process, they selected a non-thermally broken threshold to be used below the doors and fixed sidelights. The result of this was a primary window and door system with sufficient condensation resistance for the given interior conditions, but that experienced heavy condensation and frost on the thresholds during the winter (Figure 4). The authors performed an investigation including IR thermography and thermal analysis to evaluate the performance of the installed systems. The IR scans (Figure 5) and the measurements showed surface temperatures on the solid aluminum thresholds were up to –11 C (20 F) colder than those on the thermally broken window and door frames. Legal action had resulted in a settlement agreement, and the end-result was the installation of new, custom-fabricated (to allow for installation around mullions and other non-removable elements), thermally broken thresholds to provide similar performance to the doors and windows. A week of near-design exterior conditions provided a natural performance test for the initial mockup installation (condensation had not occurred, while other original thresholds were covered with frost) prior to the full-scale installation. This case is a good example of the importance of detailing and the use of accessory products (such as thresholds)—specifically, how these types of decisions can have very significant impacts on overall system performance if they are not fully understood.
Too much moisture (by accident)
This case study involves a new residential, multifamily building in northeastern United States that experienced significant condensation on the exterior windows during its first winter of operation (Figure 6). The authors’ firm was contacted by one of the building residents and asked to “confirm that we have thermally broken windows” in the façade. The building was recently completed and occupied, and was in the midst of its first winter season when occupants began reporting condensation, often heavy to the point where water would pool on the adjacent flooring. The building was a condominium, where occupants had purchased their individual units based on an ‘offering plan’ describing the features and the performance of the structure. It was designed and built at a time when the local energy code was undergoing significant changes, both in terms of improved thermal performance and airtightness, the latter being a relatively new concept in building design for energy efficiency (as opposed to the more well-understood concepts of increased insulation and higher performing fenestration). To achieve code compliance, all exterior walls were insulated with closed-cell spray applied foam (ccSPF) insulation to provide both high R-value and airtightness, and fenestration was well-integrated with the exterior wall system using perimeter membrane flashing.
Am building home in norther Ontario, presently framing basement. Exterior walls, roof , etc are done however apart from ICF in basement upstairs not yet insulated.
Outside temperatures are now dipping well below freezing. For the next month or so am I better to have no heat at all in basement as we work or is it ok to maintain a temp just above freezing? Which will minimize condensation until we can fully insulate? Thank you.