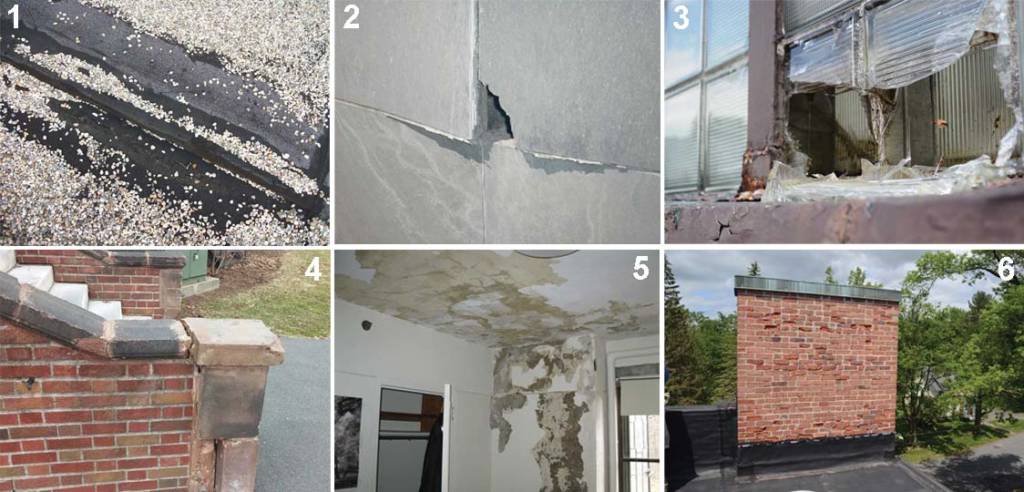
Material sampling and analysis
Testing of building materials assists in planning for ongoing rehabilitation projects.
Mortar analysis
If large-scale mortar joint repointing is recommended, knowing the components of the existing mortar will aid in specifying new mortar. The test method described in ASTM C1324, Standard Test Method for Examination and Analysis of Hardened Masonry Mortar, breaks down mortar samples and identifies proportions of sand, cement, and hydrated lime, which assists in determining the mortar type. A sieve analysis may be used to determine the grain size and colors of the aggregate. Given these characteristics, close approximation of existing mortar is possible, and is especially important for historic structures.
Concrete core sampling
Concrete structures, including parking garages, can benefit from sample analysis and testing to determine conditions that could lead to cracks and spalls. Cylindrical cores may be extracted from existing concrete slabs and evaluated for chloride ion content (a marker for accelerated corrosion of embedded steel), as well as strength and general composition. By analyzing factors that could potentially contribute to premature deterioration, this testing can provide building owners and facility managers with necessary information to anticipate concrete lifespan and guide long-range planning for rehabilitation.
Roof cuts
While it may seem counter-intuitive to cut holes in an existing roof as part of an assessment, roof cuts provide vital information that not only determines the remaining roof lifespan, but also influences the design for eventual replacement. Besides providing samples for hazardous materials testing, invasive probes through a roof at select locations allow the design professional to understand the depth of the system, as well as the deck condition and configuration. Probes can provide critical information otherwise unknown by the building owner and architect/engineer. For example, a roof deck assumed to be concrete may actually be gypsum, wood, or metal. Each of these materials may require different anchorage methods for a new roof.
Water infiltration testing
Implementing a water test, via a spray rack or even via a garden hose, helps identify where and why an assembly or system leaks. Facilities personnel often deal with recurrent leaks in a particular building over a lengthy period. With a controlled water test, the source of those persistent problems may be identified within a few hours. Further, if indicated, the standardized procedures can measure the rate at which water and air infiltrate an assembly such as a window.
Invasive probing
To examine concealed conditions, it may be advisable to create a probe into the building façade. A brick wall surface, for example, may be but one of a number of wythes of solid masonry, or it might be a single layer of brick anchored across a drainage cavity, a veneer of very thin brick adhered to a metal panel, or perhaps some other construction type altogether. While typical straightforward visual observation offers some clues, certain types of wall construction are indistinguishable until the inside of the wall can be examined. Knowing the wall type also aids in diagnosing deteriorated conditions.
Even in cases where original documents and drawings illustrate the composition of the exterior wall assembly, as-built construction can differ markedly from the design. Invasive probes can also reveal construction defects or design deficiencies that can lead to problems, from leaks to displacement to structural failure. For the purposes of a complete and comprehensive condition survey, removal of a section of the wall area may seem unnecessarily destructive. However, the small patch needed to restore the façade might be worth it if the investigation uncovers problems that might have been catastrophic had they been missed.