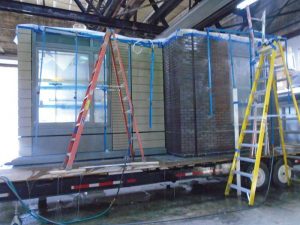
Conversely, a significant benefit of prefabricated wall panels is an accelerated onsite construction schedule. The installation of exterior enclosure materials, such as waterproofing, sealants, or mortar, is limited by weather restrictions, often requiring temperatures above 4 C (40 F) without wet or humid conditions. Prefabricated panelized wall systems can allow for a year-round construction season, thus limiting lost workdays due to weather. The wall panels can be assembled in the shop at the same time as the building structure is being constructed. The duration of the exterior panel installation can be drastically shortened. As an example, a traditionally built façade system with metal panel cladding can take up to eight months to complete, from studs to cladding, but, in the authors’ experiences, the prefabricated panels can be lifted and installed in just two months, thus resulting in a net six-month gain in the overall construction schedule.
The reduction in construction schedule can be added to the benefits of year-round construction, which could result in lowering project cost.
Aesthetics
The exterior wall cladding with prefabricated wall panels can vary, though they typically incorporate a lightweight rainscreen cladding such as metal panels, terra cotta, thin-brick, and/or glass fiber reinforced concrete (GFRC) panels.
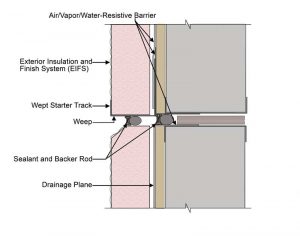
Overall panel dimensions are limited due to travel size restrictions, such as bridge clearance or width of roads or tollbooths, and the maximum panel width will vary. As a result, the panel sizes and joint spacing may not be aesthetically desirable. The joint spacing may be more obvious with some cladding types such as brick masonry, and less apparent with rainscreen metal panels, as they tend to hide the joints. Further, the panel joints are larger than a traditional one. Most construction joints are sized for building deflection, long-term creep, thermal movement, etc., but prefabricated panels require a larger joint size to accommodate construction tolerances.
Structural design
The manufacturer will need to design the panels for gravity, lateral, and hoisting loads, their attachment back to the base building structure, as well as the joint size to accommodate the anticipated movement. The panels will be attached to the structural steel or floor slab edges of the building. The panel loads and anchor locations must be provided to the structural engineer of record designing the base building structure to ensure it can support the panels and associated loads—another reason for the panels to be designed early in the design phase.
Workmanship and quality control
A benefit of the panelized wall systems is the improved quality control (QC) when constructing panels in the shop. The window penetrations, which are often the cause of exterior wall leakage in conventional construction, are installed in a controlled setting, and the installation can be regulated so the same crew installs all windows and flashing, thus leading to better and more consistent installation. Panel construction is inspected by a designated QC manager as the components of the façade are installed, and a good QC program tracks individual panels with progress sheets to confirm each step in the installation. Also, it is easy for an outside third party, such as the architect or a building enclosure consultant, to review multiple panels in a short period of time by visiting the shop without needing special access. Third-party inspections are more effective because the inspector can review conditions up close, as compared to the limited site inspections from the ground.