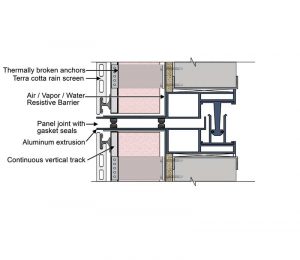
Membrane
Continuous membrane, such as self-adhered or silicone membrane with bellows, provides a more reliable and durable water and air barrier in the long-term and overcomes many limitations inherent with field-applied sealant joints (Figure 3). The membrane, when properly adhered and sealed to both panels, provides continuity of the water/air/vapor-resistive barrier with the same durability and life-expectancy as the field of the wall. Membrane joints require access to the panel sheathing or membrane after the latter is installed on the building. The exterior cladding and insulation adjacent to joints must be left off the walls until after the membrane transition is installed in the field, thus increasing the installation time. As such, this joint detailing may not be feasible for all types of exterior wall claddings or aesthetic designs.
Expandable foam tapes
Expandable foam tapes are a time-efficient way to detail the joints between prefabricated panels during panel erection, as the tape is adhered to the panel edges before the adjacent one is installed. Once the adjacent panels are installed, the foam tape can be released to slowly expand to fill the joint and form a compression seal (Figure 4). As it expands, force is exerted onto the panel return edges, which must be solid, continuous without abrupt plane changes, and parallel.
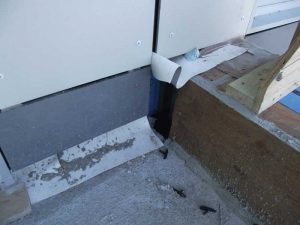
Some foam tape manufacturer installation instructions neither require the sealing of tape edges to the panels nor sealing the butt joints at the ends of the tape with sealant, so the additional requirements to seal all edges and joints between tape rolls should be clearly specified. This is particularly important at the panel corners, as the foam tape cannot bend 90 degrees and instead must be cut, providing another vulnerability at a critical transition. The installation of the foam tape is installer dependent and it is beneficial to inspect 100 percent of the foam tape for gaps, foam defects, or unsealed cut edges if the tape is the primary WRB.
Rubber gaskets and interlocking joints
Rubber gaskets offer another time-efficient way to provide water/air/vapor-resistive barrier continuity at panel joints (Figure 5). Gaskets are applied to panels in the shop and provide a weathertight enclosure as the panel is installed. Rubber gaskets rely on the compression of the gasket against an adjacent hard substrate or another gasket to fill the joint and typically require the panel perimeters to be constructed with a metal extrusion to which the gaskets are attached. It can be challenging to achieve continuity of rubber gaskets at the four-way panel joint intersections, which has four separate gaskets with 90-degree corners coming together. Even with perfect compression and alignment of panels, a small gap remains between the gaskets. The gap requires sealing to ensure a continuous water/air/vapor-resistive barrier at the gasket intersection. Gaskets can become hard and brittle in the long run, making them less effective as the panels continue to move and deflect. Further, it is impractical to replace the gasket without deconstructing the panels.