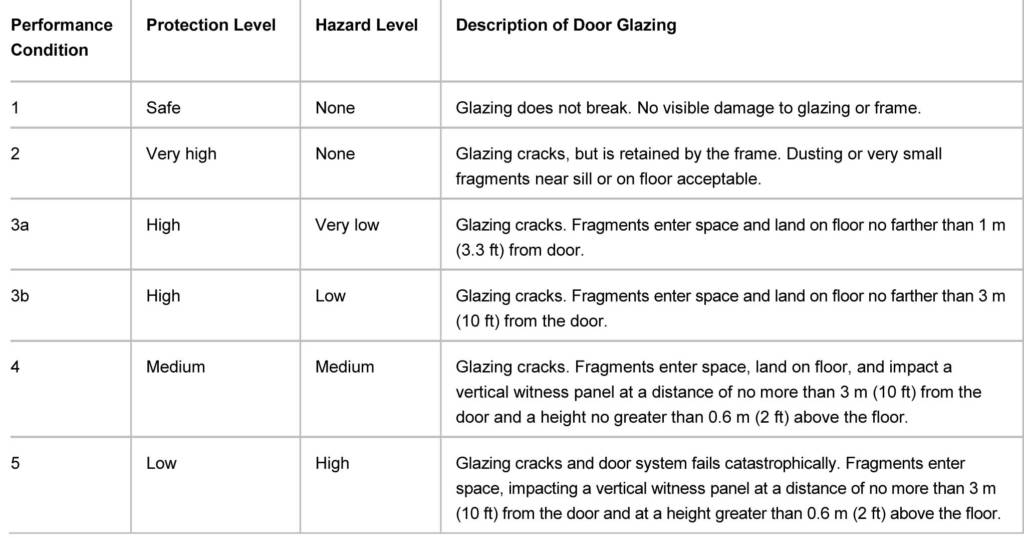
Hurricane resistance
In coastal climates prone to hurricane-force winds, building products must demonstrate their resilience to windborne debris. Testing per ASTM E1996, Standard Specification for Performance of Exterior Windows, Curtain Walls, Doors, and Impact Protective Systems Impacted by Windborne Debris in Hurricanes, consists of shooting a small or large missile at a product sample. Depending on the missile size a door can withstand, manufacturers may consider their hurricane-impact-resistant products as either modified or custom.
Blast mitigation
Like hurricane-impact-resistant doors, blast-mitigating doors may be designated as modified, but are most often considered custom, as blast load requirements are usually project-specific.
For high-security and high-risk building applications, entrance systems can be tested for compliance with:
- ASTM F1642, Standard Test Method for Glazing and Glazing Systems Subject to Airblast Loadings;
- U.S. General Services Administration/Interagency Security Committee (GSA/ISC) TS01-2003, Standard Test Method for Glazing and Window Systems Subject to Dynamic Overpressure Loadings;
- security design criteria; and
- U.S. Department of Defense Unified Facilities Criteria (DoD UFC) 4-010-01, Minimum Antiterrorism Standards for Buildings.
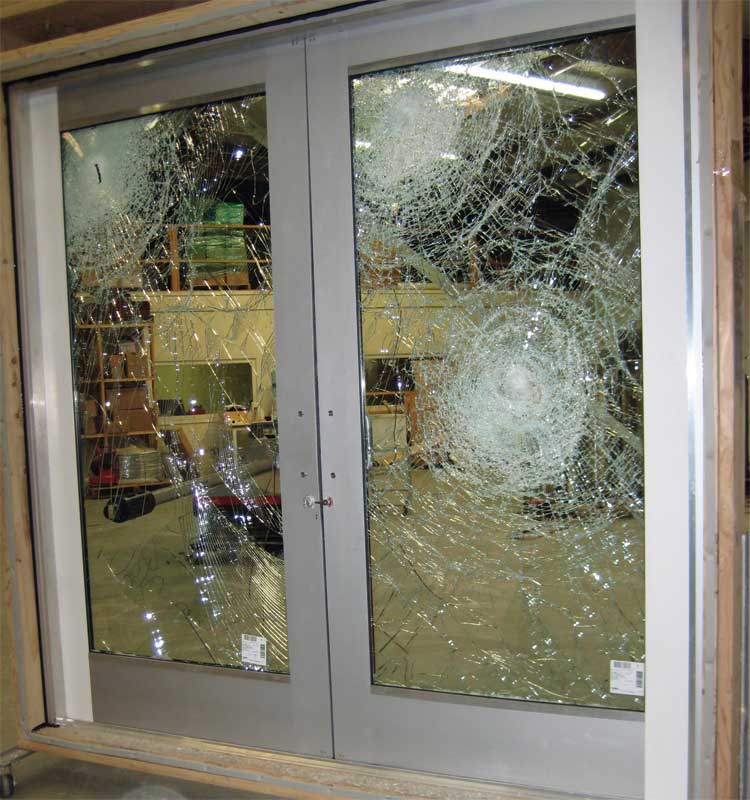
To guide door selection, GSA/ISC TS01-2003 describes performance conditions by injury hazard classifications (Figure 2).
Forced entry
For some more common security considerations, modified and custom door products may also be specified to resist forced entry. AAMA 1304-02, Voluntary Specification for Forced Entry Resistance of Side-hinged Door Systems, details test methods for applying a 136-kg (300-lb) point load on the doorframe to try to create a 152.4-mm (6-in.) gap between the door and the frame.
Finish choices
For doors that withstand rigorous use and harsh environments, one should specify either:
- the highest-performing organic paint coating meeting AAMA 2605-13, Voluntary Specification, Performance Requirements, and Test Procedures for Superior Performing Organic Coatings on Aluminum Extrusions and Panels; or
- an anodize coating meeting AAMA 611-14, Voluntary Specification for Anodized Architectural Aluminum.
For maximum durability, anodized aluminum not only highlights the natural beauty of metal in clear and bronze tones, but also provides excellent wear and abrasion resistance with minimal maintenance. Anodizing resists the ravages of time, temperature, corrosion, humidity, and warping. Most anodized finishes are offered as part of the standard product selection.
When color choice is a priority, high-performance 70-percent polyvinylidene fluoride (PVDF) coatings offer nearly any conceivable hue while also shielding against weathering, pollution, and aging. The pricing for standard paint colors varies from equal to bronze anodize to five to seven percent higher. Non-standard and custom-matched colors increase the cost. Some manufacturers are also willing to provide a different color or finish type on the exterior of the frame than the interior.
Unsurprisingly, the most economically priced entrance systems are standard doors. Modified doors are moderately priced, and custom doors are the most expensive. Accounting for the door, frame, glass, and installation, a building owner’s purchase order for a single door can range from $900 for standard to $1200 for modified, or multiple thousands for a custom entrance.
Similarly, standard doors offer quicker lead times from when the order is placed to when it arrives on the jobsite for installation. With standard components and finishes, these doors may be ready for pickup or shipping in one to three days. Modified doors with non-standard components, finishes, and hardware may have lead times of two to four weeks, while custom doors can take six to eight weeks or longer to produce as specified.
Manufacturers’ warranties for aluminum entrance systems vary greatly. Professionals should be sure to review them carefully before specifying a product. Working with a dependable manufacturer early in the project will ensure the highest quality, reliable thermal performance, adherence to budget, and on-time delivery.
Jon O’Neil is a manufacturing engineer at Tubelite Inc., providing technical support on custom and standard aluminum doors and frames for commercial applications, as well as leading new product initiatives to meet clients’ future needs. He earned a bachelor of science in engineering from Western Michigan University. O’Neil can be reached at jo’neil@tubeliteinc.com.