Phase one in three parts
Lee Lawrence, WJE principal, describes three distinct parts of phase 1 of the research project. The first was the conceptual design side or creating different prototypes of structural members to work with this new type of concrete and its unique attributes. The second was the materials aspect, or helping the contributing producers develop UHPC with local materials. The third part involved the structural evaluation of small-scale specimens that were developed.
This extremely dense material with enhanced mechanical properties lends itself to slender and more durable structures. Concrete is known to be weak in tension and this enhanced version also takes advantage of pre-stressing. Steel fibers are often added to resist the applied shear forces without help from steel reinforcing bars. This eliminates time spent ensuring bars are designed and detailed properly and placed within clear cover requirements.
“The precast concrete is not only thinner and lighter, but we can realize labor savings by removing secondary reinforcing steel,” said Force. That may prove to be a critical factor, given the uncertain future of the labor force in some areas of the country.
With fewer internal reinforcement needed, UHPC cross sections have less volume, therefore, less weight, while providing the same capacity as conventionally reinforced concrete. Multiple pieces stacked on a truck would reduce transportation costs.
Plant perspective
“The challenges inherent in the complex mixing procedures are the same qualities making it well-suited for use in a precast concrete setting,” said John Lawler, WJE principal. “The precast concrete producer has more control over their production processes, and the time required to handle and place the concrete is limited in that setting.”
However, precast concrete production facilities need to determine their ability to handle the different types of materials in appropriate quantities.
“You cannot just dump a bag of fibers into the mixer and call it UHPC,” said Lawler.
Phase 1 developed information to support implementing UHPC at the precast concrete plant, which is intended as a how-to guide for precast concrete producers. It outlines ways to develop UHPC mixture proportions, how to use and select locally available materials, and ways to use existing equipment or consider investing in new equipment.
“The guide was written with the idea of smoothing the transition from conventional concrete manufacturer to one using UHPC,” said Lawler.
For production adopting UHPC is similar to what happened more than 20 years ago with self-consolidating concrete (SCC). SCC was a means to improve production processes and reduce labor. Some producers embraced the technology, mobilized quickly, trained personnel, and positioned themselves to make efficient use of SCC. With the new guidelines from this project, precast concrete producers can gear up quickly to produce UHPC.
“I feel like we have made significant headway; all six participating producers were able to reproduce a mix with local materials, no matter where they were located in the United States or Canada,” said Lawler.
New concepts
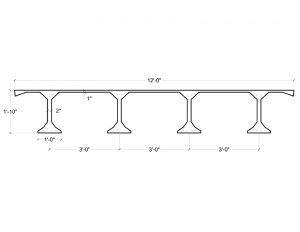
“The mix design aspect is critical,” said Lawrence. “However, it was also important the team does not get bogged down with traditional components and what had been done in the past. Given the high tensile strength of UHPC, we wanted to take advantage of these unique mechanical properties.”
“Rather than falling prey to the old mindset of using stemmed members, we challenged the flat floor concept,” said Force. “There has been pushback regarding the weight and depth of double tees.”
Rather than consider a variation on that theme, one concept emulates a double-slab system.
“If these flat-deck products can incorporate other trades offsite to meet the needs of owners and constructors, that will be a game changer. That will bring added value as precast concrete producers embrace true modular construction and evolve into systems builders rather than just manufacturers,” said Force.
Long-span precast concrete components were designed, produced, and tested by the project team in conjunction with volunteer producers across the country. Despite the higher cost of the raw materials, the optimized designs and reduced cross sections will make these UHPC products competitive with steel and other similar materials, and eventually with conventional concrete products.
Optimized space
Traditionally, precast concrete cladding for a multistory building was 152 mm (6 in.) thick or more. Now 51 mm (2 in.) is achievable with UHPC. In terms of cladding, glass-fiber-reinforced concrete (GFRC) has long been less than 51 mm but UHPC may be able to carry loads GFRC cannot. Removing the weight from the building also impacts the foundation. A residential project with parking underneath can have 18 m of column-free space, which enhances the efficient use of the space. Double-tees could be another option, if needed.
“The clear spans in the garage and throughout the structure are revolutionary by themselves,” said Tadros.
A promising concept for floors allows for a 18 m length with a depth of 560 mm (22 in.). The relatively shallow structural depth incorporating the mechanical, electrical, and plumbing (MEP) systems provides a cost-effective story height. Tadros has not seen a product like this voided slab system spanning 18 m, with the top and bottom of the product only 25 mm (1 in.) thick.
The research team completed phase 1 and “early results are fantastic,” said Tadros. “The outcomes show this can be done without huge capital investment.”