by Tiffany Coppock, AIA, NCARB, CDT, ASTM, RCI, EDAC, LEED AP
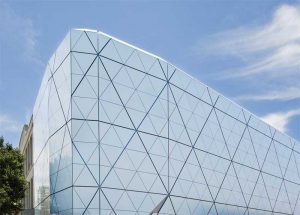
Open, light, and airy. Repurposed for a new life. So much of a building’s design comes down to the feeling one hopes to inspire in the inhabitants and the confidence underlying the facility’s performance. Some insulating materials, such as rigid cellular glass insulation described in the August 2019 issue of The Construction Specifier, are designed to support that confidence by providing a level of redundancy to safeguard against water infiltration on the roof in mission critical buildings. The feeling of a building can also be supported by the insulating material in the cladding. Today’s building designers look to continuous insulation (ci) options to deliver a breadth of performance attributes including thermal, moisture, acoustic, and environmental benefits.
Viewed through this broader lens of performance attributes, compressive strength becomes an important selection criterion. However, the decision on what material to specify often comes down to weight, or at least it used to. Many architects and specifiers are finding reasons to rethink the weight factor in light of new research suggesting weight does not always equal strength.
Density does not always mean strength
Compressive strength in ci is a critical consideration as it reduces risks of deflection and contributes to the ability of the wall assembly to resist higher loads, whether from the weight of the cladding itself or wind movement across walls. Higher compressive strength can even translate into less product damage during installation.
For decades, specifiers have relied on material density as an indicator of compressive strength, equating a higher density or weight with a material’s strength. Thus, the denser the material, the more compressive strength it was assumed to have. While there is some truth in this observation for both foam plastics and mineral wool, the two are not directly related as it was once thought. It is important to keep in mind, according to ASTM C578, Standard Specification for Rigid, Cellular Polystyrene Thermal Insulation, Type V polystyrene insulations at a density of 3 PCF exhibit a compressive resistance of 100 psi (690 kPa). Conversely, a typical high density 8 PCF mineral wool ci touts a 439 psf (21 kPa) of compressive resistance. While the test methods for the two materials vary (ASTM D6122, Standard Practice for Validation of the Performance of Multivariate Online, At-Line, and Laboratory Infrared Spectrophotometer Based Analyzer Systems, for extruded polystyrene [XPS] versus ASTM C165, Standard Test Method for Measuring Compressive Properties of Thermal Insulations, for mineral wool), simply holding the two materials by hand reveals the density difference between them. Advances in mineral wool production, including patent-pending processes, are improving this strength-to-weight ratio even further. Lighter, stronger materials enable more flexible design options to create the building architects envision.
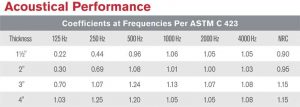
Image courtesy ASTM
Manufacturing advances
Among insulation materials, mineral wool insulation is made by spinning molten rock or slag into fibers that are then bound together to create insulating material. Mineral wool was one of the earliest forms of insulation to be produced, originating in Germany in the 1870s, and has been manufactured in the United States since the 1930s. Today, mineral wool is perhaps best known for its fire resistance, and increasingly, for its sustainability attributes (like recycled content), which can contribute to green building certifications. However, as the building science community learns more about the ‘chameleon-like’ properties of mineral wool, research has focused on how to deliver higher levels of compressive strength.
Studies have shown, at a microscopic level, the random arrangement of fibers resulting from the spinning process that creates mineral wool could impact its strength, depending on the direction of forces applied to the insulation (read The compressive strength properties of mineral wool slabs: Influence of structure anisotropy and methodical factors by Andrius Buska and Romualdas Mačiulaitis, published in the Journal of Civil Engineering and Management). New, proprietary processes are optimizing binder content and fiber orientation to maximize the compressive strength of mineral wool without adding to its weight. For example, newly engineered automated processes create a highly uniform base layer of material that is fed through specialized equipment, enabling manipulation of the fibers and overall product structure. The benefit of this technology is a high level of control over the mechanical and thermal performances of the finished product.
In tests of mineral wool ci manufactured using these new patent-pending techniques, high compressive mineral wool outperformed a heavier insulation and resulted in a weight reduction of 25 percent. Applied across a full-scale commercial project, such as a mixed-use building or high-rise structure, that could mean a significant reduction in overall weight and stress on the cladding. While every project is different, reduction in weight is likely to lead to a decrease in attachment system material, whether that is fasteners or the amount of metal needed in girts. This could translate to lower material and labor costs.
Beyond strength, chameleon-like properties
Many specifiers are already familiar with mineral wool for its fire resistance and high R-values, but the total profile of this material has made it an increasingly popular choice. The following are some of the benefits mineral wool delivers throughout the enclosure.
Thermal performance
Mineral wool provides an R-value of up to 4.3 per inch per ASTM C518, Standard Test Method for Steady-State Thermal Transmission Properties by Means of the Heat Flow Meter Apparatus. Mineral wool can be used to support performance goals such as mitigating thermal bridging risk, particularly when used in applications requiring high compressive strength where the cladding attachment is completely outside the ci, and only a small amount of screws penetrate the insulation to the wall below.
Moisture resistance
Mineral wool ci is engineered to absorb only 0.03 percent moisture by volume in testing simulating application in an exterior wall cavity. This is more than adequate for the intended application in an above-grade wall behind cladding. If it does get wet, mineral wool returns to its thermal properties after drying out.
Fire resistance
Mineral wool is fire resistant to temperatures above 1093 C (2000 F). Designed to prevent the spread of fire and smoke, mineral wool helps contribute to fire-resistant assemblies, protecting buildings and its occupants.
Acoustics
Mineral wool absorbs sound and per ASTM C423, Standard Test Method for Sound Absorption and Sound Absorption Coefficients by the Reverberation Room Method, rates above 1 (perfectly absorptive) at frequencies over 1000 hertz, at as little as 38-mm (1.5-in.) thickness (Figure 1).
Is slag -wool considered “friable” and therefore, Respirable? Its not a carcinogen, is it?