
Photos © Francis Dzikowski/Esto. Photo courtesy Museum of Moving Image
Additional attachment options
The cladding attachment system is another key factor when it comes to choosing ci. Mineral wool ci may be attached with simple, inexpensive fasteners such as impaling pins, screws with washers, or even adhesives. It can also be secured between masonry ties or girt assemblies. Impaling pins can be installed prior to the air and water barrier (AWB), adhered to the AWB, or screwed through it. Mineral wool also works with clip and rail systems. Some ci offers its own hanger system as well, which is designed to simplify and streamline installation.
The high compressive strength of mineral wool ci enables the use of additional attachment options such as girt systems completely outboard of the insulation due to its ability to resist deformation.
Responsible use of resources
Whether the design and specification team are looking to meet a Leadership in Energy and Environmental Design (LEED) certification, or simply maximize the sustainability efforts of the materials used, mineral wool insulation is a responsible choice for ci and other insulating purposes. With its 70 to 75 percent slag content—one of the highest recycled contents among all ci products—mineral wool can help contribute points to various certifications. Mineral wool is also inorganic and does utilize blowing agents. Mineral wool can also resist exposure on a jobsite in the presence of extreme temperatures and ultraviolet (UV) light.
Better vapor permeability and moisture control
A building must be able to manage vapor flow as well as drain any liquid moisture out of the building. While many foam-based board insulations slow the transfer of vapor through the wall, mineral wool ci is exponentially more vapor permeable, so designers are given maximum freedom in selecting where or even if a vapor barrier is placed in the wall assembly. This makes mineral wool a versatile choice across various climate zones.
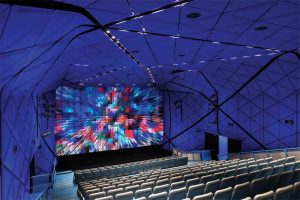
Ci must also be able to withstand exposure to moisture, without retaining any incidental moisture that may reach the exterior wall cavity. Advances in technology allow mineral wool to be engineered to be hydrophobic and repel water as it reaches the insulation. Any moisture that is collected drains and the insulation dries completely. Once dry, the mineral wool’s R-value returns to previous levels.
Robust performance in harsh conditions
The Museum of the Modern Image (MOMI) in New York is a good example of a building project that illustrates mineral wool as a ci. The innovative open-joint system features mineral wool securely installed behind the cladding. Not only do these materials need to perform every day in the building assembly, but they were also exposed to jobsite challenges while the project was being completed. Over a nine-month period, the materials stood up to water, snow, ice, and plenty of UV light. While it is always important to protect materials on a jobsite, the reality of Mother Nature and the nuances of production schedules mean materials can be left exposed. In the case of the MOMI project, only a few minor pieces of mineral wool needed to be replaced, even after three seasons of exposure. Mineral wool proved to be robust, able to withstand a heavy load and the conditions on the jobsite.
Better acoustics
Lower-density insulation does not have to mean a noisier environment. As noted earlier, mineral wool has an impressive sound attenuation profile even at a minimal thickness. While this is often seen as an advantage with interior walls and floors, when used in ci, mineral wool helps impede noise transmission. Today’s thinner, more conductive claddings increase opportunity for sound to transfer from outside to inside (or vice versa). Mineral wool can uniquely help these buildings achieve that elusive inner peace.
Specifying for strength
It is time to re-think the perception that a correlation always exists between higher weight and higher strength. As specifiers look to match cladding to ci, they should consider compressive strength separately from density. Research has demonstrated a lighter weight material, such as mineral wool, can certainly meet, and even exceed, mechanical and thermal performance expectations, while offering ancillary benefits to support fire resistance, sound attenuation, vapor and moisture management, green building goals, and ease of use on the jobsite. With new, light, strong options now available, specifiers may find an insulating material’s high density weighs a lot less heavily in their ci decision-making.
Is slag -wool considered “friable” and therefore, Respirable? Its not a carcinogen, is it?