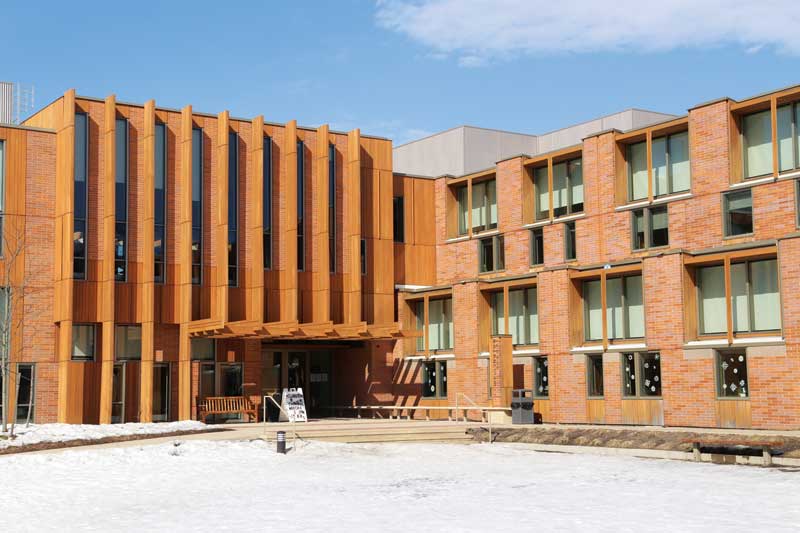
Published by the State of California Department of Health Services’ Environmental Health Division, the table provides guidelines for land use compatibility, dividing into four categories: normally acceptable, conditionally acceptable, normally unacceptable, and clearly unacceptable.
Normally acceptable
Specified land use is satisfactory, based on the assumption any buildings involved are of normal conventional construction without any special noise insulation requirements.
Conditionally acceptable
New construction or development should be undertaken only after an extremely detailed analysis of the noise reduction requirements is made and needed noise insulation features have been included in the design. Conventional construction with closed windows and fresh-air-supply systems or air-conditioning normally suffices.
Normally unacceptable
New construction or development should be discouraged. If new construction or development does proceed, a detailed analysis of the noise reduction requirements must then be made and any needed noise insulation features included in the design.
Clearly unacceptable
New construction or development should generally not be undertaken.
Acoustical mitigation for specific mechanical equipment
Just as in real estate, the most important factor to consider in mitigating HVAC noise is location. Prior to construction, noisier building systems components should be located away from more noise-sensitive properties. Ideally, noisy components like chillers and pumps are located inside mechanical rooms or in a central plant. At a minimum, portions of the structure would be used to block the line of sight to noise-sensitive receptors. Using a central plant, rather than packaged units, allows the noisier components to be inside, helping contain the sound and reduce the impact to
the community.
With a central plant system, cooling towers are often the major offender to the community noise level. Sound generated by a cooling tower comes from the fan, the motor, cascading water, and the gear boxes.
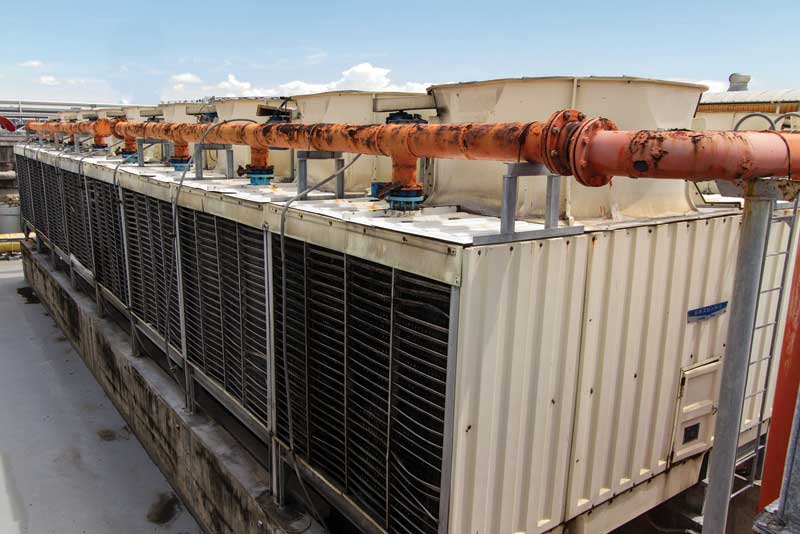
Two common cooling tower types are forced draft and induced draft cooling towers. Forced draft towers usually have centrifugal blower fans on the side of the air stream entering the tower. These towers are usually a little louder compared to induced draft cooling towers. However, they are more contained with fewer components directly exposed to the exterior, and some can be operated indoors. Since their fans are capable of additional static pressure, forced draft towers are able to include ductwork, and sound attenuators can be applied on the inlet and outlet if necessary for noise control.
Induced draft towers have the fan on the exit of the air stream, pulling the air through the tower. Their fans generally cannot handle the additional static pressure that sound attenuators cause. Consequently, beyond selecting cooling towers with efficient and quiet fans, the typical mitigation options for induced draft cooling towers are location, oversizing the tower so the fans run at a slow speed, and sound barrier walls. To limit the noise generated by cooling towers, the project specification should include sound limits for the specific tower based on measurements conducted using Cooling Technology Institute (CTI) 128, Acceptance Test Code for Measurement of Sound from Water-cooling Towers.
Mechanical chillers—which can be another important source of environmental noise—are classified by their compressor type. These include reciprocating, rotary screw, frictionless centrifugal, and absorption.
A reciprocating chiller is similar to an automotive engine. An electric motor turns a crankshaft that causes pistons to compress a gas. As the piston compresses the gas, it heats up and is exhausted into the condenser. Capacity in a reciprocating chiller is typically controlled by keeping specific exhaust and inlet pistons open; consequently, the electrical motor turns at the same rate regardless of the required capacity.
Rotary screw chillers use two mating helically-grooved rotors. Gas is compressed by rotating the screws. Capacity of a rotary screw chiller is controlled by variable-speed drives. While all chillers have a tonal aspect to the noise, the tonal characteristic of screw chillers is significantly more pronounced.
Thanks so much for sharing this information on controlling noise coming from different systems. I had no idea that a hard surface on the opposite side of the acoustical wall could eliminate the benefits of the acoustics in the first place. It sounds like if you plan on renovating a building with acoustics, you should probably make sure that you get consultation services before building or tearing down any walls. After all, you definitely don’t want an accidental “canyon effect” on your hands!
Thank you for this information! What is the best type of testing to be sure to have all octave bands from the system mitigated and having no more complaints about the system running? I understand that there may be low frequencies that can cause vibrations, that cannot be detected with a sound decibel meter. The higher pitched tones a decibel reader would reveal. So, if the receiving property is getting 60 dBA from the decibel meter, from the higher tones, what about the lower hz vibrations? How do you read those? Thank you, again.