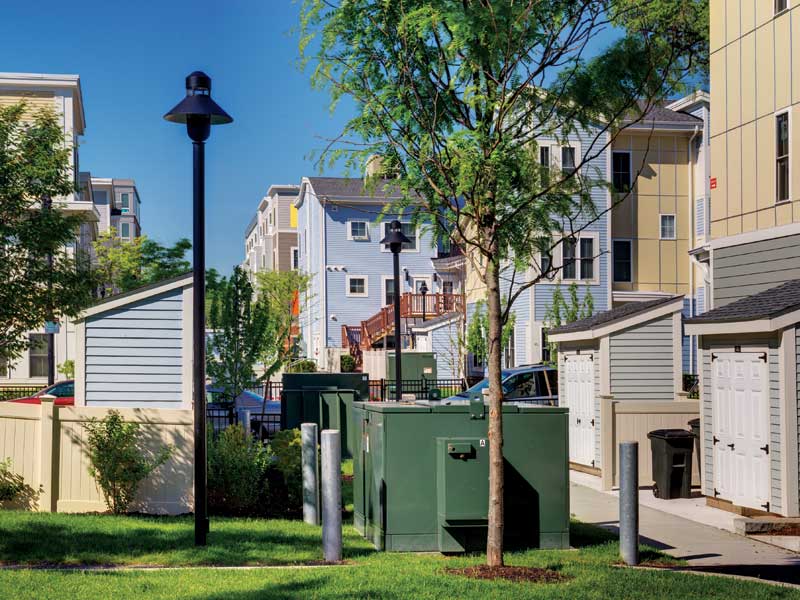
Less common in the United States, the frictionless centrifugal compressor is similar to a centrifugal water pump or fan—the impellor spins to compress the refrigerant. They use magnetic bearing technology for the shaft. Thanks to the magnetic bearing, these chillers can be significantly less noisy compared to the other chiller types. They use a variable-speed direct-current (DC) motor with a direct drive. Absorption chillers, on the other hand, do not use mechanical compression; instead they use a heat source such as steam or natural gas.
Most chillers are capable of being enclosed and consequently the best method of mitigating chiller noise is enclosing them inside the building with high mass walls such as grouted concrete masonry units (CMUs) and acoustical door assemblies. The noise generated by chillers should be limited using specifications referencing sound measurements that are conducted in accordance with Air-conditioning, Heating, and Refrigeration Institute (AHRI) 1280, Sound Power Rating of Water-cooled Chillers.
Air-cooled chillers contain both the chiller and an induced draft cooling tower in a single system. It is sometimes best to avoid using this style of system when directly adjacent to noise-sensitive receptors because the mitigation options are limited. The tonal characteristic of a chiller can be prevalent, but because this system includes a cooling tower, it is not possible to enclose these chillers.
Some air-cooled chillers can include an acoustical package that wraps components of the chiller in mass-loaded vinyl. While these acoustical packages help reduce the noise, the reduction is modest. As this equipment needs to operate outdoors, the noise mitigation options are limited to careful space planning (location) and the design of acoustical barrier walls.
There are more options for acoustical mitigation for other rooftop equipment like exhaust fans and air-handling units (AHUs). In extremely sensitive cases, this equipment can be located inside the structure. If the fan is selected to be able to operate under higher static pressures, air inlet and outlets can include sound attenuators.
There are two types of exhaust fans that due to code typically cannot use sound attenuators. Kitchen exhaust and laboratory exhaust have particles in the exhaust air that can cause corrosion or collect in the sound trap—consequently, sound attenuators often cannot be used. In the case of kitchen exhaust, the mitigation options are very limited. Location of a kitchen exhaust, careful selection of a quieter exhaust fan, and providing acoustical barriers between the exhaust opening and noise-sensitive receptors are the main options when addressing kitchen exhaust noise.
In addition to exhausting caustic particles, laboratory exhaust fans require fast velocities at the exhaust opening to expel the exhaust into the atmosphere, diluting the caustic particles. Increased exit velocities cause additional noise, beyond what is generated by the exhaust fan. Some high-plume exhaust openings are acoustically more efficient than others, but as with kitchen exhaust these fans should be located further away from noise-sensitive receptors and, in some cases, require acoustical barriers to provide additional attenuation.
Typical acoustical mitigation
Beyond locating noisy equipment as far from noise-sensitive abutters as possible, control of mechanical noise in the environment is typically achieved by enclosing the equipment, designing an acoustical barrier, or including sound attenuators or splitters at the inlet or outlet of the system.
Fully enclosing the mechanical equipment is the most effective option, provided it is indeed an option. At times, it may not be possible to enclose the equipment entirely, because some equipment needs access to outside air in order to function properly. In these cases, where air inlet and outlets are necessary, a sound attenuator, acoustical louver, or splitter can be used.
Sound attenuators are essentially ducts constructed of heavy-gauge sheet metal and perforated sheet metal baffles typically filled with an acoustically absorptive material such as mineral wool or fiberglass. In the cases where the air is caustic or needs to have higher levels of purity, the acoustical material in the baffles can be enclosed in Mylar bags, or removed from the sound attenuator completely (i.e. ‘packless attenuators’). Without an acoustical fill, the sound reduction provided by the attenuator is limited.
Acoustical louvers are similar to sound attenuators in that they have perforated sheet metal baffles with an acoustically absorptive fill, but are much shorter in length. When more attenuation is required, a louver can be replaced with a sound attenuator (as space allows), or filled with acoustical ‘splitters,’ which are perforated sheet metal baffles without the encapsulating ductwork.
Acoustical barriers and walls provide attenuation by redirecting the noise. Walls are most effective when they are located either close to the source or close to the receptor. In the case of addressing community noise, it is generally better to build the wall near the source, since there are usually a number of receptors at various distances. That said, when designing the barrier, sufficient clearance must be maintained between the wall and the equipment to allow for proper airflow and for maintenance access.
Thanks so much for sharing this information on controlling noise coming from different systems. I had no idea that a hard surface on the opposite side of the acoustical wall could eliminate the benefits of the acoustics in the first place. It sounds like if you plan on renovating a building with acoustics, you should probably make sure that you get consultation services before building or tearing down any walls. After all, you definitely don’t want an accidental “canyon effect” on your hands!
Thank you for this information! What is the best type of testing to be sure to have all octave bands from the system mitigated and having no more complaints about the system running? I understand that there may be low frequencies that can cause vibrations, that cannot be detected with a sound decibel meter. The higher pitched tones a decibel reader would reveal. So, if the receiving property is getting 60 dBA from the decibel meter, from the higher tones, what about the lower hz vibrations? How do you read those? Thank you, again.