by Sean D. Browne
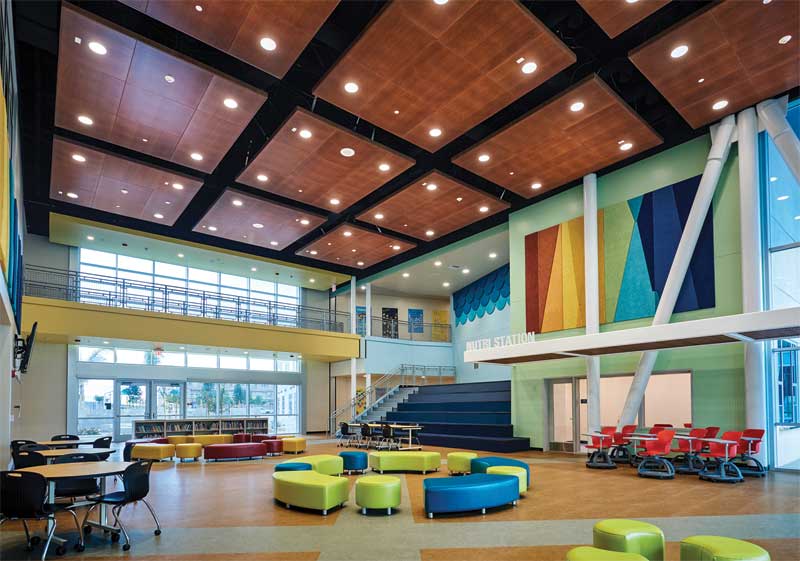
Current design trends often call for exposed structure spaces where there is no ceiling plenum and building service elements such as ductwork and piping are visible overhead.
Sometimes called the “warehouse look,” exposed structure spaces often experience acoustical problems due to excessive sound reflection off the hard roof deck surface and the added volume of the space. Conversations, activity sounds, and HVAC operations will all contribute to excessive noise and reverberation. Reflections off the deck between cubicles in open plan office environments can cause distractions for nearby occupants. As a result, exposed structure spaces usually need some type of sound absorbing elements to control noise and reverberation.
Many noise issues related to exposed structure designs can be addressed through the use of acoustical ceiling clouds, canopies, and shapes. These three types of “free-floating” options absorb sound on both their front and back surfaces. Direct-to-deck panels, vertical panels, and acoustical roof decks can also provide much-needed acoustical absorption in these reverberant spaces.
Acoustical clouds
Created for use in either new construction or retrofit applications, acoustical clouds are an ideal way to define spaces in an exposed structure and enhance acoustics without sacrificing design flexibility. When suspended above work areas, acoustical clouds provide a type of interrupted ceiling plane. As such, they help control both reflections between cubicles and distant reverberation, thereby reducing occupant annoyance and distractions.
Acoustical ceiling clouds are available in a variety of standard sizes, ranging from 2 x 2 m (6 x 6 ft) to 4 x 4 m (14 x 14 ft). Standard shapes range from squares, circles, and rectangles to hexagons, trapezoids, and convex or concave panels. Custom sizes and shapes are also available.
A typical cloud system consists of 0.6 x 0.6 m (2 x 2 ft) ceiling panels with factory finished, pre-cut corners and a separate kit containing all the pre-cut-to-length, ready-to-assemble suspension system and perimeter trim components required to create the cloud. The choice of ceiling panel in the cloud includes mineral fiber, fiberglass, wood fiber, or perforated metal panels.
Acoustical clouds are normally installed in a standard 25-mm (15/16 in.) grid system. Today, installation systems reduce the number of hanger wires and recess them from the perimeter edges, making the hangers less visible and producing a more dramatic, “free-floating” look for the cloud. Building services such as HVAC, lighting, sound masking, and sprinklers can be cut into the acoustical clouds just like a traditional wall-to-wall ceiling system. However, due to the discontinuous nature of acoustical clouds, existing building service elements can often be installed in between the clouds, allowing for easier retrofit capability.
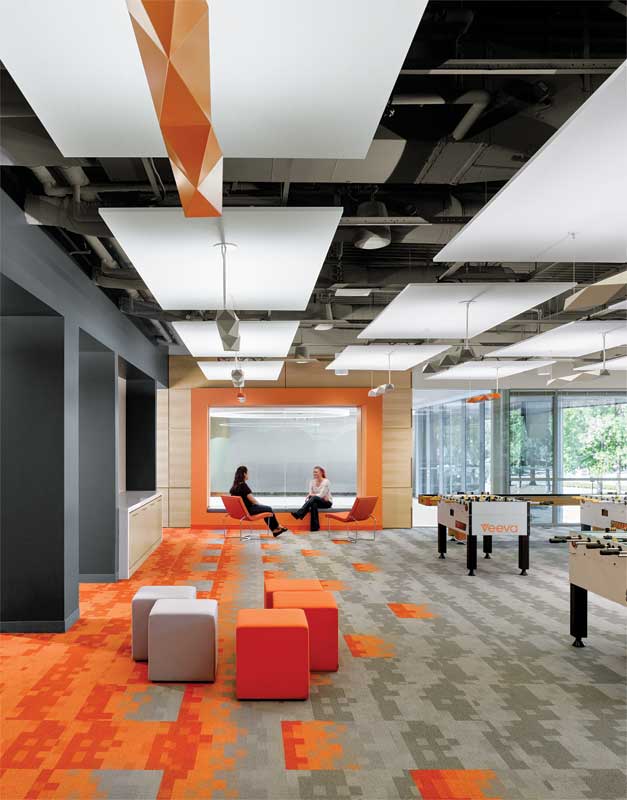
Case study
The Customer Experience Center (CEC) at the GE Advanced Manufacturing Works in Greenville, South Carolina, not only showcases GE manufacturing advancements but also hosts a multitude of corporate events. As a result, the design team at MCA Architecture in Greenville looked to create a multifunctional, exposed structure space that was both dynamic and energetic.
To meet the design intention, the team selected acoustical clouds. According to project architect, Michael Kissam, clouds were selected for several reasons.
“First,” he says, “we were looking for a ceiling treatment that was not static or overbearing but evoked a sense of movement, dynamism, and progression. Second, we were under an extremely aggressive schedule that had to be completed in nine months from design to client occupancy. The cloud kits provided a unique advantage because the clouds could be fabricated at ground level and raised to their finish elevations at the last moment. This installation sequence allowed for the overhead utility work to be completed while mitigating the ceiling grid and tile damage that is a reoccurring problem for typical project close-outs.”
He also reports acoustics was a key consideration because the CEC is designed to accommodate a variety of different functions.
“The majority of the surfaces are glass walls and ceramic tile, so the ceiling was our only opportunity to control the acoustics,” he explains. “By layering and overlapping the clouds, the ceiling created a baffling effect that proved to be highly effective.”
In total, 53 circular clouds ranging in diameter from 2 to 4 m (6 to 14 ft) were installed in the CEC.
“The finished product and function of the acoustical clouds exceeded our design intention and, more importantly, the client’s expectations,” he says.
Wood fiber roof decks offer acoustic control |
Acoustical clouds, shapes, baffles, and blades made from cementitious wood fiber help control noise in exposed structure spaces. Structural acoustical roof decks made from cementitious wood fiber can do the same.Cementitious wood fiber roof decks are available in a variety of composite and non-composite panels in plank or tile configurations to address a building’s design requirements. Both types of panels are usually made of rapidly renewable aspen wood fiber bonded with an inorganic hydraulic cement. They offer a noise reduction coefficient (NRC) up to 0.80 to provide predictable acoustical performance, often eliminating the need for additional noise reducing materials. Both feature a textured interior finish.The panels are a potential noise reduction solution for large, high traffic, exposed structure spaces such as auditoriums, gymnasiums, arenas, pools, and multi-use facilities. They also help meet the Leadership in Energy and Environmental Design (LEED) and the American Society of Heating, Refrigerating and Air-conditioning Engineers (ASHRAE) requirements for spaces such as gymnasiums and auditoriums.Non-composite panels are typically used in low-slope applications, are compatible with virtually all roofing materials, and provide a thermal barrier for field-applied foam plastics. They also meet stringent sustainability criteria, including environmental product declaration (EPD), health product declaration (HPD), and Declare. Composite roof deck panels are typically used in sloped applications where acoustics, insulation (R values up to 44), a nailable surface, and structural integrity are all required. By providing all these features in one panel, wood fiber composite roof decks are faster and easier to install than the multistep installation of steel deck systems. |