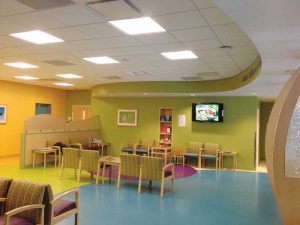
Photos courtesy Owens Corning
Sound strategy #2: Block
Blocking sound involves creating a physical barrier to acoustic energy. Typically, this is a layered approach to a wall design that includes insulating a wall or floor assembly. Architects have many insulating options to choose from. For walls with STC values lesser than 50, there is no significant difference in acoustic performance between mineral wool and fiberglass insulation. In selecting an insulation material, both fiberglass and mineral wool offer similar levels of sound reduction. This frees up designers to select an insulating material based on other performance needs. For example, a designer might choose mineral wool to achieve a higher hourly rated fire wall and to help support life-safety objectives. Other properties, such as a material’s ability to manage vapor and liquid moisture or its resiliency or compressive strength can drive the choice of insulating material used in an assembly. Although fiberglass insulation performs well in all acoustic applications, in high-performing walls mineral wool insulation can provide a slightly higher level of STC performance.
Sound Strategy #3: Break
Breaking sound is achieved by creating a physical disconnect between vibrating components, so the sound wave cannot travel between them. Breaking strategies are often used in multi-family structures, where it is important to reduce the amount of noise that can be heard between units. An example of this approach can be seen in double-wall construction, where each wall covering has its own studs instead of sharing them. This approach eliminates the opportunity for sound energy to use the studs as conductors of noise from one space into another. Installing insulation in the cavity between two stud walls further reduces the flow of sound energy by absorbing it, reducing energy flow from the source space into the adjacent space.
Sound strategy #4: Isolate
A fourth strategy to reduce flanking noise is isolation. It is commonly used to manage mechanical vibration such as rooftop HVAC equipment or to improve sound transmission through walls and floors. Isolation enables one area to vibrate without that energy traveling to the adjacent rooms. In the case of HVAC equipment placed atop a roof, vibration-absorbing curbs help prevent the vibration and sound energy from transmitting to the building structure where it can then pass into the spaces below. A similar strategy can be used in floor assemblies where soundproofing clips absorb the vibration from walking and impact on the story above. In walls, isolation can be achieved by using resilient channels, changing the flow of sound energy to a path with higher resistance, such as an insulated cavity, rather than along the stud path where sound is more easily conducted.
Design best practices
While flanking noise can be managed with the four strategies described above, some considerations during the design stage can help avoid noise issues from arising once construction is complete. Following are four best practices to consider at the design stage.
1. Consider the space’s purpose
What function does the space provide? Will noisy equipment be in the space that might disrupt conversations? Will private conversations, such as those between a healthcare provider and patient, occur in the space? Isolating areas with heavier traffic away from consulting or meeting areas can protect privacy.
2. Look for cost-effective strategies
Identify interventions that are easy to introduce into the design and economical to implement. As an example, installing solid doors and drop-down door seals reduces the ability of sound to infiltrate. Adding insulation batts above walls that do not extend to the ceiling deck can improve privacy at a lower cost compared to retrofitting the walls or ducts. Adding caulking around the wall perimeter and specifying outlets in different cavities supports privacy measures.
3. Spec full-height walls
Specifying walls that extend up to the ceiling deck defends against flanking noise that travels from space-to-space via a ceiling plenum. If a full-height wall is not practical (this is more of a concern with modular environments), adding a row of insulation 150-mm (6-in.) thick and 610-mm (24-in.) wide will help reduce flanking noise.
Other design options for reducing ceiling plenum flanking include installing caulking around the wall perimeter and adding crown molding at the intersection of the wall and ceiling. Lining HVAC ducts also supports speech privacy.
4. Consider mechanical systems
Adding pipe insulation with mass-loaded vinyl cladding and isolating the pipe from the structure can defend against noise from a building’s mechanical pipes while also providing thermal insulation. Of course, insulation installed in the wall assembly of the mechanical room and surrounding areas can further reduce the mechanical system noise. While good design typically locates these spaces away from more occupied areas of the building, the noise from mechanical pipes has led to a common observation in mechanical spaces with steam-powered operations, “The pipes are coming up.”
Even the most sophisticated industrial or commercial insulation specified for an enclosure will not deliver if it is not properly installed. A range of resources, including materials published by the National Insulation Association (NIA), can help contractors ensure materials are installed to deliver optimal performance.
However, at the end of the day, sound performance begins with setting the spec. Specifying the right insulating materials for the job during the design stage can help owners and occupants achieve the most desirable result in a chaotic world—quiet, comfortable spaces. In this light, sound acoustic performance is priceless.
Kevin Herreman is a member of the senior technical leadership at Owens Corning with over 30 years of experience in acoustics. His technical expertise includes design, modeling, and testing of materials and systems for acoustics and noise control. Herreman holds multiple patents for noise control materials and systems. Herreman is chair of the Institute of Noise Control Engineering (INCE) Technical Activities Committee for Product Noise Emission.