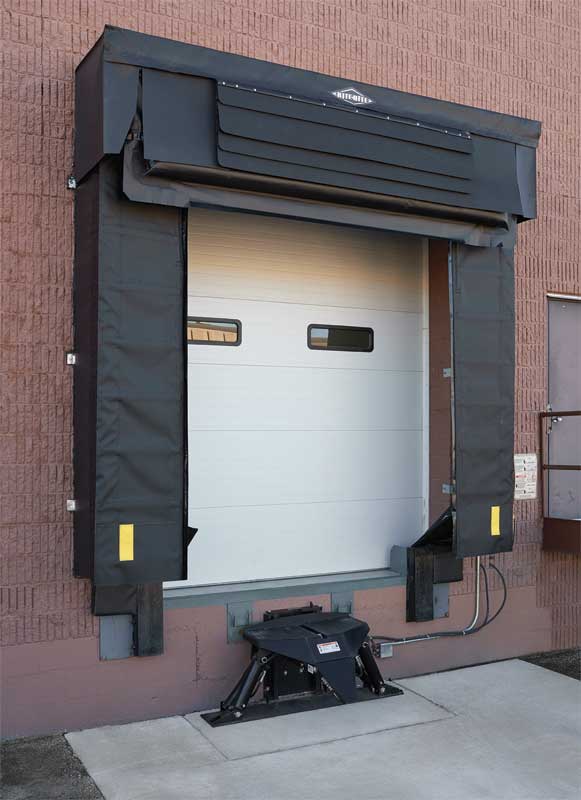
Even when trucks and trailers have been secured to the facility, conditioned air can still escape and outside air may enter, translating into hundreds of dollars of energy costs streaming out through gaps. Moreover, gaps around the perimeter of a dock opening allow outside contaminants like rain, dust, or insects to infiltrate the facility. When trailers are at the loading dock, 250 to 500-mm (1 to 2-in.) gaps often exist between a swing-open trailer and the edges of the opening. The bottom of the dock door (where the leveler, trailer, and dock seal/shelter all meet) is another notorious gap in the building’s perimeter.
Sealing gaps around the perimeter is essential to maintaining the microclimate. This can be achieved with dock seals or shelters. For drive-through applications, shelters compatible with vertical levelers must be used. Through special design features, these shelters ensure tight sealing against trailer sides, across the full width of the trailer top and at the corners, without interfering with the vehicle doors being opened and closed after it has been parked at the dock. Exposure to the outside environment is nearly eliminated.
Many factors must be considered when choosing the right dock seal or shelter. It is crucial to know the number of trailers received each day and the different types (e.g. over-the-road, lift-gate, reefer, or intermodal trailers). Each loading dock position also needs to be surveyed to understand the door size, dock height, bumper projection, and whether there is an incline or decline drive approach.
Partitioning space with curtain walls
Similar to the loading dock, the inside of a facility requires various partitions with tight seals in order to create the desired microclimates for temperature-sensitive products. Industrial curtain walls are a simple, cost-effective way to develop such an infrastructure and strengthen quality controls.
By using fabric curtain walls, facility managers can easily create compartmentalized, microclimate spaces for raw material or ingredient protection, specific processes, or employee comfort and safety. Creating temperature-controlled zones makes it possible to be much more efficient with HVAC expenditures, instead of unnecessarily heating or cooling large areas.
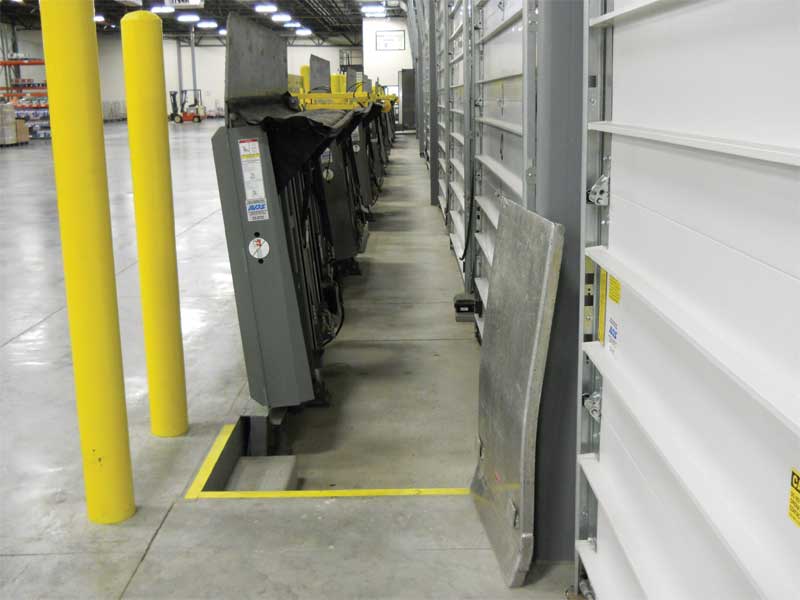
Because of their modular design, industrial curtain walls can easily be reconfigured if a space needs to be enlarged or reduced, or the shape of the footprint must change. They are also durable enough to withstand contact from machinery and can provide up to 22 C (40 F) of temperature separation with the right blend of fire-resistant polyester batting.
Humidity, which is closely linked to air temperature, is often another microclimate concern that can be addressed by insulated curtain walls. Separating a higher humidity space from and area of lower humidity generally requires mechanical chilling equipment and a barrier. This situation could occur in a food warehouse, for example, with a high humidity environment for short-term storage of vegetables.
Insulated curtain walls with vinyl-covered surfaces work well in this application as a barrier between two different humidity zones. Their surface is waterproof and the insulation inhibits the transfer of heat away from the outer surface, keeping the surface temperature above the dewpoint of the exterior air so that there is no condensation.
Fabric curtain walls can be easily installed, trimmed to fit around conduit, piping, or ductwork, and anchored to the floor to withstand a pressure differential. Depending on the application, a curtain wall can be suspended from the room ceiling, or it can hang from a standalone framework. The most common insulated curtain wall panels weigh approximately 2.5 kg/m2 (0.51 lb/sf), so construction considerations are minimal. They are available as stationary and sliding applications and can be fitted with strip curtains, personnel doors, or high-speed industrial doors.
Minimizing energy loss with high-speed doors
Whether it is taking processed product from one zone to another, or transporting food from a freezer to a loading dock, moving materials between work cells can trigger a massive energy loss. Traditionally, plants with hard, permanent walls employed solid-core doors with high R-values, which minimize heat transfer. In recent years, however, high-speed, fabric roll-up doors have become a common choice, particularly when connecting microclimate zones separated by curtain walls.
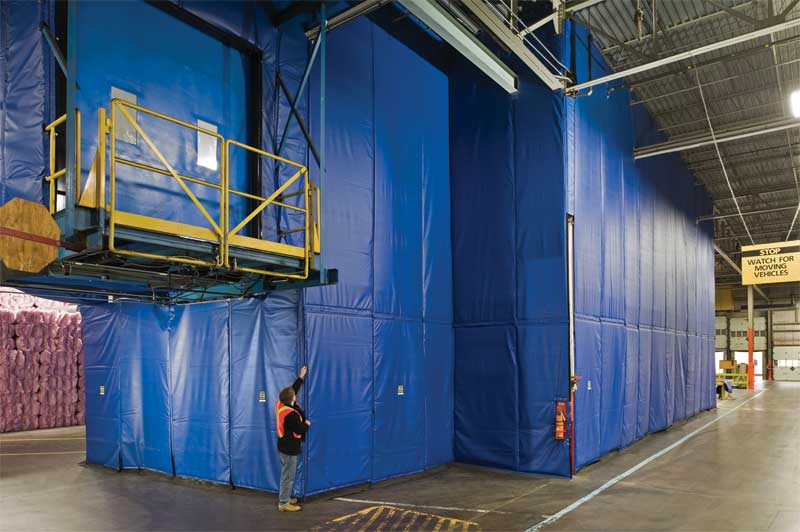
Since traditional rigid doors are typically heavy and slow moving, they are often impractical or unfeasible to integrate with non-permanent walls (e.g. curtain walls). Additionally, the high-cycle processes in food and pharmaceutical plants, which can demand hundreds of openings and closings a day, often lead workers to simply leave doors open—thus negating the doors’ effectiveness as an energy loss barrier.
Upgrades in high-speed door technology provide options delivering R-value high enough to minimize conduction of heat, while still delivering quick operational speeds. The most advanced high-speed, roll-up doors operate up to 2.54 m (8 ft) per second, which helps minimize air infiltration and maintain temperature and humidity levels in microclimates.
Additionally, advanced high-speed doors can absorb impact from a forklift and automatically re-align in their tracks, unlike traditional, solid-core doors. Solid doors are also susceptible to impact damage and the subsequent air penetration. Further, the most advanced roll-up doors will incorporate a one-piece radial header and non-corrosive side frames that can be removed for regular cleaning and are compliant with the U.S. Food and Drug Administration current good manufacturing practices (cGMP) guidelines. Made from a smooth polypropylene fabric with the ability to handle acids and bases well, these high-speed doors are ideal for food industry operations.