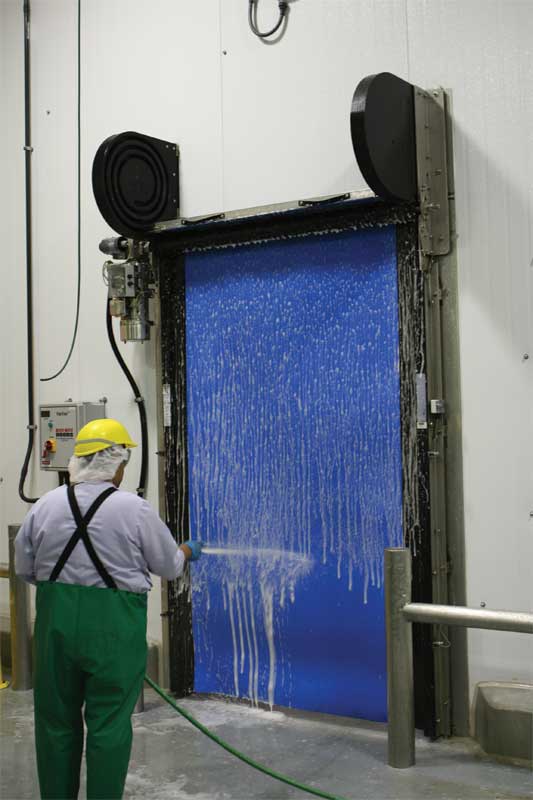
HVLS fans provide air quality consistency
Within microclimate zones, high-volume, low-speed (HVLS) fans can provide benefits beyond lowering the perceived temperature. Through a process called destratification, HVLS fans can help stabilize temperatures from floor to ceiling, allowing the thermostat set point to be more accurate. In the food industry, creating a uniform temperature throughout a cooler can help minimize the chance of product spoilage, and translates into energy savings since the cooler does not have to work as hard to maintain the desired temperature.
HVLS fans mitigate the rising heat effect by destratifying layers of heated air as they gently circulate warm air from the ceiling back toward employees at the floor level. Thus, facilities equipped with HVLS fans reduce the burden on their heating and cooling system and are able to realize the true thermostat setting at virtually any height in the building.
For maximum environmental and energy control, multiple HVLS fans can be linked into a single network managed by one control station. Networking can greatly increase fan efficiency and overall HVAC performance by setting fan speeds to meet the needs of specific areas of a facility experiencing temperature variations due to interior factors, such as production equipment, or external factors like ambient sunlight or open loading dock doors.
The controller allows for independent speed adjustments, scheduled start/stop times and the ability to start/stop based on preset temperature settings—a feature that can be very helpful in food operations such as produce, cheese, or wine storage. It also ensures fans are only running when they need to, thereby reducing energy use.
Fabric ductwork provides uniform air dispersion
While metal duct systems have been used to distribute air in buildings for decades, this author has seen fabric air dispersion systems becoming more prevalent in industries demanding precisely controlled environments. There are several reasons for this, ranging from their effectiveness in evenly distributing air to manufacturing costs associated with the ducting materials.
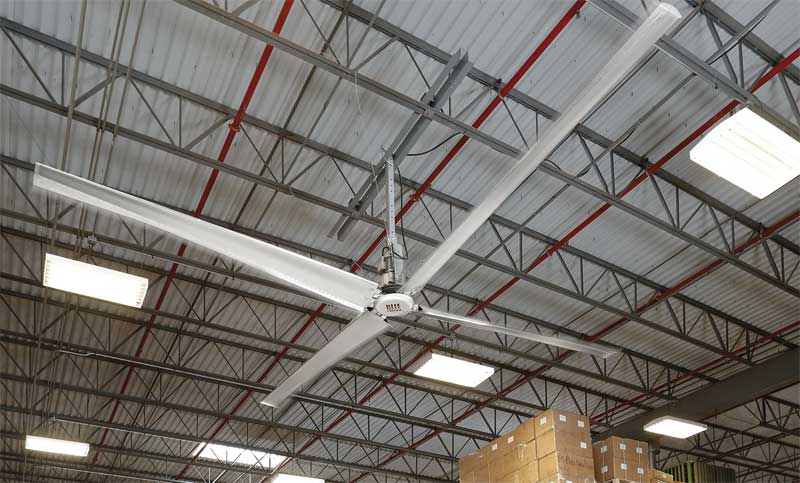
Fabric ducts provide targeted, precise, and efficient air dispersion throughout the length of their run. In contrast, standard metal ductwork using localized diffusers spaced many feet apart can create hot and cold spots along the length of the system. Fabric ducts use various methods to achieve this uniformity, including: air porous fabrics, linear vents, nozzles, and orifices. Providing versatility similar to that of curtain walls, fabric ducts are easier than their metal counterparts to customize and reconfigure as needs change.
The various types of fabric air dispersion products allow facility managers to specify the performance requirements that will best serve their environments. One of the benefits of fabric ducts is ease of customization for each application. Whether the facility handles produce or pharmaceuticals, fabric ducts help ensure that every product is in the same environment from the front of a conditioned zone to the back.
Fabric ducts are also fairly easy to install when creating microclimates within a larger facility. Since they are significantly lighter than their metal counterparts, installation is usually faster, there is less of a load on the ceiling structure, and setup costs are lower.
Conclusion
Maintaining multiple microclimates within facilities can be done with the right combination of products working together as a system. From loading dock to plant floor, designers and specifiers should consider the following methods to ensure the supply chain is protected:
- complete the seal at the loading dock with a drive-through set-up;
- implement fabric curtain walls to create separate microclimate zones;
- use high-speed doors to provide access between these zones;
- install HVLS fans to ensure consistent temperatures within microclimates; and
- invest in fabric ducts to spread conditioned air.
Proper implementation of these steps can help industrial facilities save on energy costs while ensuring product integrity and bolstering employee efficiency.
Walt Swietlik has more than 35 years of experience in the material handling industry, and is currently director of customer relations and sales support for Rite-Hite. For the past 22 years, Swietlik has managed Rite-Hite’s customer fly-in program, where he works closely with a variety of customers to address the challenges associated with shipping and receiving areas. Swietlik’s experience has put him in close contact with customers from many industries with unique safety and loading dock challenges. As a result, he has become an expert on issues related to shipping and receiving, and ensuring safe and efficient material flow. Swietlik has spoken at a variety of local, regional, and national forums, including the ProMat and MODEX trade shows. He can be reached at wswietlik@ritehite.com.