Loads and other safety equipment
PV panels add weight to a rooftop—an important factor in design and installation. Existing structures should be analyzed by a structural engineer to determine if this additional weight is acceptable.
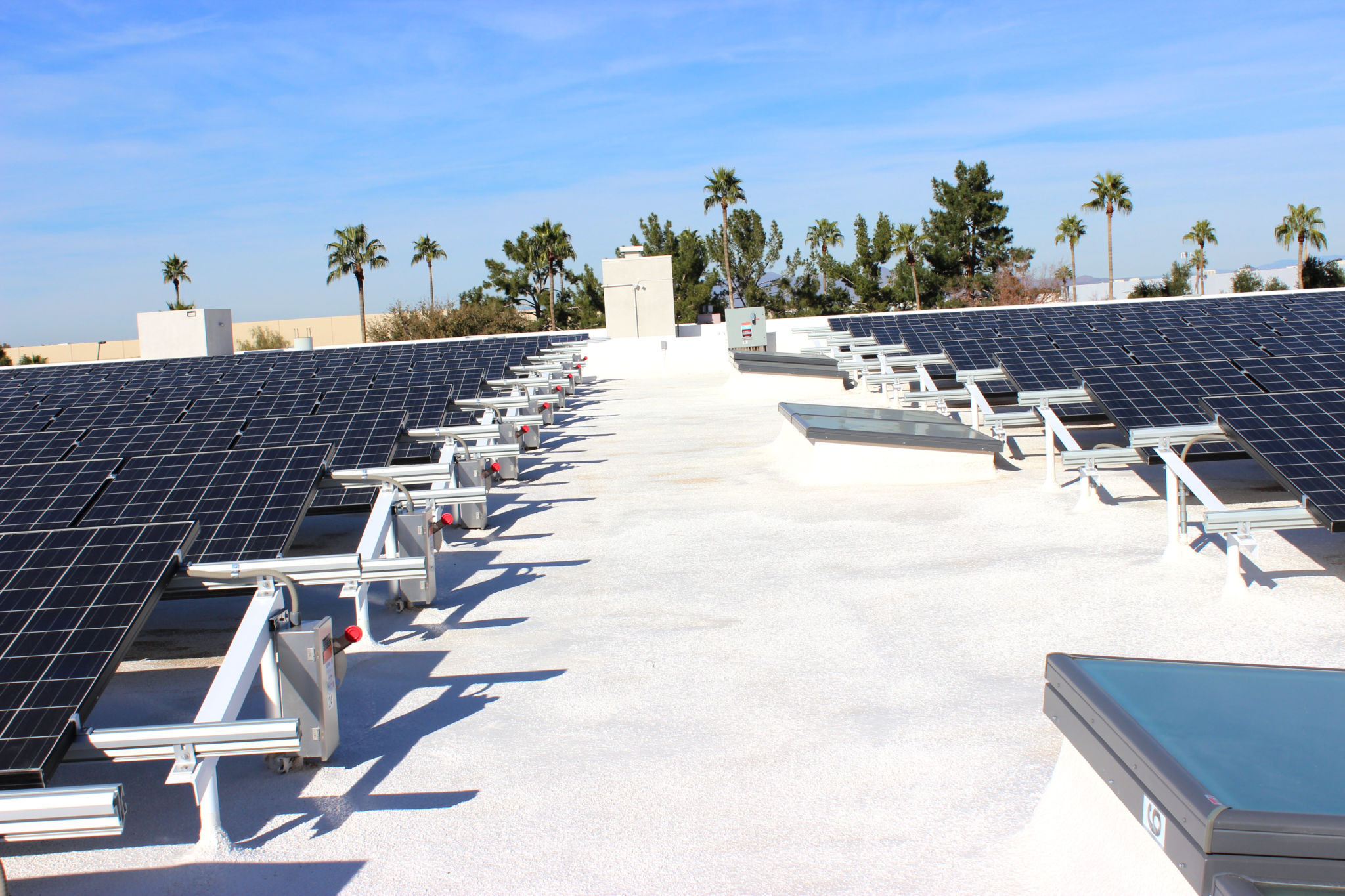
Rack-mounted arrays with penetrating attachments are fairly lightweight, at 0.9 to 1.3 kg/m2 (2 to 3 lb/sf). Ballasted arrays add 1.8 to 2.7 kg/m2 (4 to 6 lb/sf). With the latter, more ballast is utilized at the PV array’s perimeters and corners. Thus, localized loading from ballast may reach as high as 5.4 to 7.7 kg/m2 (12 to 17 lb/sf). Most SPF roofing systems have a compressive strength of 40 to 60 psi (275 to 413 kPa).
Additionally, roofs are required by codes to provide ‘live-load’ capacity—a measurement that allows for people, snow, and other weight-bearing temporary scenarios. PV system weight is typically below the live-load capacity. However, in the absence of structural analysis, this capacity will be reduced by the addition of the PV system.
A final consideration is whether a PV installation will create new locations for drifting snow to land, which may add considerable weight to a roof.
When determining key considerations for wind load and fire safety, best practices require deferral to the PV supplier.
Equivalent service life and maintenance needs
Ideally, the expected service life of the roof and PV systems should align. Removal and reinstallation of a PV system is costly, and should be weighed against the residual service life of the existing roof and cost of roof replacement at the time of PV installation.
Ballasted, rack-mounted PV systems are difficult, if not impossible, to reroof (or recoat) under and around. Elevated racks with adequate space beneath may be able to be left in place when reroofing. For example, a PV system covering 10 percent of the rooftop is easier to relocate during reroofing than one that covers 75 percent. Building owners should be advised of future reroofing and maintenance costs that may come with roof-mounted PV systems.
Other considerations
All roof-mounted PV systems should be inspected and maintained at least twice a year. Wiring, attachment points, and flashings should be inspected. Cleaning of the top surface of PV panels may be required.
Workers must be able to access both the roof and PV systems. PV systems should not block access to drains, penetrations, flashings, mechanical units, or other rooftop equipment. They should be installed so maintenance workers can access wiring, inspect panel-to-racking connections, and properly clean surfaces without stepping on PV panels.
Installation of PV systems on SPF roofing will create foot traffic. In these trafficked areas, additional coating and granules or walk pads can be used for protection.
Drainage on rooftops is important for safety of the structure and longevity of the roof. PV arrays often have many points of contact with a roof—possible locations for will blocking or slowing drainage. PV racking should be positioned to minimize water ponding or use methods such as notched pads to allow drainage under points of contact, especially for ballasted systems.
Roof systems used as platforms for PV panels must be tough and durable. Generally speaking, SPF has greater compressive strength as density increases. Thus, higher-density SPF systems may be preferred, particularly when ballasted support systems are used.
The SPF system will be stressed during the PV installation. Coatings and granules can help protect the roof during installation and scheduled maintenance. Given that roof surfaces below PV panels will likely not dry as fast as non-covered portions, it is best to select coatings that can weather standing water and biological growth.
Conclusion
While there are many considerations to be weighed in the integration of photovoltaic systems with sprayfoam roofs, the energy generation and conservation provided by the combined solution is well worth the effort.
Rick Duncan, PhD, PE, is the technical director of the Spray Polyurethane Foam Alliance (SPFA), an organization representing contractors, material and equipment manufacturers, distributors, and industry consultants. SPFA promotes best practices in the installation of sprayfoam and offers a Professional Certification Program to all those involved in the installation of the product. Duncan can be reached at rickduncan@sprayfoam.org.