FAILURES
Deborah Slaton, David S. Patterson, AIA, and Jeffrey N. Sutterlin, PE
In the southeastern United States, a 12-story office building, constructed in the early 1930s, experienced uncontrolled water leakage through its mass masonry exterior wall. As this was attributed to weathering of the existing mortar joints in the brick and terra cotta façade, the joints were specified to be repointed with a 1:1:6 mortar mix (Type N per ASTM C270, Standard Specification for Mortar for Unit Masonry). The work was performed during the summer.
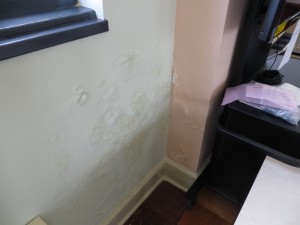
To match the original joint profile and aesthetic, the relatively wide (25-mm [1-in.]) mortar joints were struck flush with the brick face. Soon after repointing, water damage to the interior plaster wall finish was observed in localized areas adjacent the existing steel-framed punched windows. Leakage (and subsequent plaster damage) occurred primarily on the building’s north elevation, which is vulnerable to wind-driven rain. While diagnostic water testing of the window system did not result in leakage to the building interior, testing of the repointed masonry wall did.
Close-up examination of the exterior masonry revealed widespread bond line separations at the interface of the mortar and adjacent masonry in the vicinity of the interior water damage. Although many of these separations were very narrow (hairline), some were wider than 0.51 mm (0.02 in.). Even minor bond separations can represent potential leak sources—water can pass through gaps as narrow as 0.3 mm (0.012 in.).
Mortar-bond-line separations in exterior masonry are of particular concern in mass walls due to the network of inherent voids in the back-up masonry, which is typically in contact with the exterior assembly. During testing, water entered the exterior wall construction through mortar-bond-line separations and traveled inboard via voids in the terra cotta tile and brick backup wall, wetting its interior surface to which the plaster finish was applied.
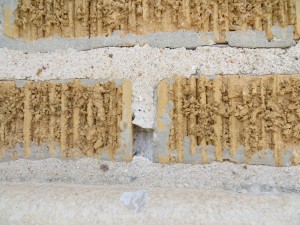
While many factors can affect mortar bond, in this example installation and curing during hot weather without following proper procedures likely contributed to lower mortar bond strength and increased drying shrinkage, and thus to bond separations. American Concrete Institute (ACI) 530/530.1, Building Code Requirements and Specification for Masonry Structures, a joint publication with the Structural Engineering Institute of the American Society of Civil Engineers (SEI/ASCE), and The Masonry Society (TMS), provides code requirements and specifications for hot weather practices for masonry construction, and is referenced in the International Building Code (IBC). A concise summary of the mandatory code practices required by IBC and ACI 530 with additional commentary is also provided in the Brick Industry Association (BIA) Technical Note 1, Cold and Hot Weather Construction, which serves as a good refresher for specifiers.
The opinions expressed in Failures are based on the authors’ experiences and do not necessarily reflect those of the CSI or The Construction Specifier.
Deborah Slaton is an architectural conservator and principal with Wiss, Janney, Elstner Associates, Inc. (WJE) in Northbrook, Illinois, specializing in historic preservation and materials conservation. She can be reached at dslaton@wje.com.
David S. Patterson, AIA, is an architect and senior principal with WJE’s Princeton, New Jersey, office, specializing in investigation and repair of the building envelope. He can be e-mailed at dpatterson@wje.com.
Jeffrey N. Sutterlin is an architectural engineer and senior associate with WJE’s Princeton office, specializing in investigation and repair of the building envelope. He can be contacted via e-mail at jsutterlin@wje.com.