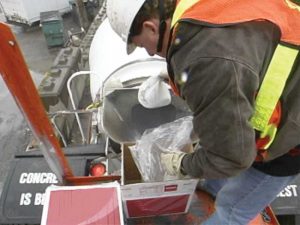
Crystalline waterproofing coating
As mentioned earlier, when applied to clean, bare, and previously saturated substrate as a slurry mixture, the reactive chemical ingredients in crystalline waterproofing can penetrate up to 300-mm deep inside the concrete by using water as the migrating solution. As these chemicals penetrate through the capillaries and pores, the reaction with the mineral byproducts of cement hydration creates the crystalline formation that fills the cracks and pores.
Crystalline waterproofing can be applied by a brush or with spray-on equipment. To ensure the success of the application, care must be taken to ensure correct surface preparation, substrate saturation, coverage rate, and curing time.
Since the crystalline waterproofing coating system has a unique chemical diffusing characteristic, proper surface preparation of the concrete is critical to the performance of the treatment. Concrete surfaces need to have an open pore texture to allow the transfer of the reactive crystalline chemicals from the coating into the concrete substrate. The surface also needs to be clean and free of form oil, laitance, and other foreign matter to ensure proper adhesion of the coating.
Crystalline waterproofing admixture
When used as an admixture the same chemical reactions take place, but cost is lowered by eliminating the labor associated with the application of a surface treatment. Additionally, the utilization of crystalline waterproofing as an admixture moves labor offsite, eliminating scheduling and delays.
Since the admixture is added to the concrete mix at the batch plant or a ready-mix truck, it ensures the crystalline formation occurs uniformly throughout the structure rather than penetrating from the surface as would be the case with a surface application. In addition to waterproofing, crystalline admixture can reduce shrinkage cracking as well as increase compressive strengths. This may be because the water is taken up into the crystalline structure, leading to a longer, internal moist cure that is beneficial for shrinkage reduction and compressive strength development. For most mix designs, the dosage rate is two to three per cent based on the Portland cement content.
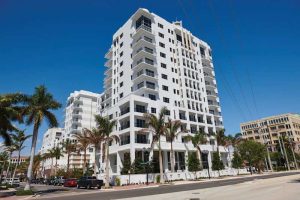
While crystalline waterproofing admixture is compatible with super plasticizers, air-entraining agents, water reducers, fly ash, pozzolans, and other ingredients used to improve the performance of modern concrete mixes, it is best to check with the manufacturer to ensure there is no incompatibility with other elements of the concrete mix, particularly concrete set retarders.
Negative-side waterproofing
Where existing underground structures are experiencing water seepage because of failed exterior membrane or coating systems, the problem can be remedied by the application of crystalline waterproofing on the negative side (inside) of the structure. Under these conditions, surface coatings—depending on the adhesion—blister and peel when moisture seeping through the concrete from the exterior dissolves soluble minerals and deposits them under the coating in the form of efflorescence. Since crystalline waterproofing penetrates into the concrete and plugs the pores beneath the surface, it stops water seepage in the concrete before it reaches the inside surface. This does not depend on its adhesion to the surface and will not blister and peel off like surface barriers.
Vapor transmission through basement floors and walls is also a common problem leading to unpleasant damp, musty odors. Testing in Japan and countries in Europe has shown the application of crystalline technology can reduce vapor flows as much as 50 percent by reducing the size of the capillary tracts in the concrete as well as making some of them discontinuous, which, in most cases, provide a drier, more pleasant atmosphere.
Crystalline waterproofing materials also have the ability to self-heal micro-cracks (<30 μm [1181 μin]) in the concrete substrate as well as macro-cracks up to 0.4 mm (16 mils) in width. The rate of self-healing depends on the size and nature of the crack (static or moving) and the hydrostatic pressure the crack may be subjected to. Self-healing could be evident in only a few days or as long as a few months depending on the ambient conditions.
When cracking takes place over a longer period of time water penetration activates the crystalline chemicals and the self-healing process will take place. Testing conducted in Japan on a cracked bridge deck 10 months after being treated with reactive crystalline waterproofing demonstrated cracks self-healed very quickly compared to control samples.
Real-world examples
Several examples of how crystalline waterproofing technology products were employed in real-world construction applications situations are illustrated
by the following projects.
May Bank Headquarters
The triple tower development designed as a new headquarter building for May Bank in Kuala Lumpur, Malaysia, involved diaphragm wall construction incorporating a nine-level underground parking garage. A crystalline technology admix was selected for the project to assist with controlling hydration heat, reduce shrinkage cracking, give the slab the capacity to ‘self-heal,’ and waterproof the concrete as well as increase its strength and durability.
The basement slab required approximately 24,000 m3 (31,391 cy) of crystalline admix-dosed mass concrete. Commencing on September 26, 1997, the initial pour of approximately 13,200 m3 (17,265 cy) was conducted over a 60-hour period; it was then and remains today the third largest continuous pour conducted in the world and the largest in Southeast Asia.
Very cleared position of concrete waterproofing.must be read
HOW DO YOU TREAT A LEAKING ROOF?