By John A. Jackson, AIA
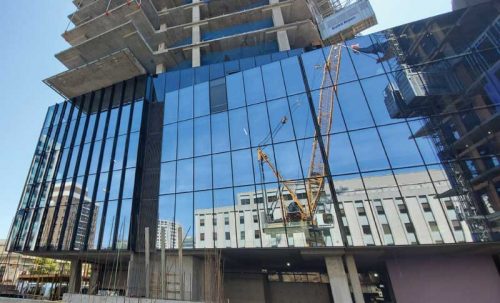
Curtain wall systems are ever present in today’s commercial construction marketplace. Whether creating new architectural expressions or rehabilitating architecturally significant historic buildings, from stick-built to unitized, “off-the-shelf” commodity to custom bespoke systems, utilizing insulating glass units or opaque spandrel panels, simple flat or complex geometry; it seems the sky is the limit with curtain wall design today.
The architectural design of curtain walls must be developed alongside increasing demand for high-performing, energy-efficient solutions. Technological advancements in curtain wall design tools, materials, prototyping, and fabrication techniques offer new avenues for achieving these lofty design and performance goals. However, budgets are limited, materials are expensive, design and construction schedules are constrained, and global supply chain logistics continue to apply pressure to projects. These and other factors present unique challenges and exciting opportunities for projects—all of which must be carefully balanced to successfully achieve the architectural vision and meet performance requirements while staying within the owner’s budget and schedule.
Design-assist is a popular procurement method for curtain wall systems in today’s commercial market, intended to help resolve these challenges, particularly for custom curtain walls with unique performance requirements and/or unique material configurations. Understanding the fundamentals of the design-assist process, roles and responsibilities of the various parties, the timeline for important decision-making, and navigating the process to avoid potential pitfalls are keys for maximizing the value that design-assist can offer projects.
What is design-assist
Design-assist, at its core, is rooted in a close collaborative relationship between the owner, architect, and contractor. AIA provides the following general definition of the design-assist delivery method:
Design Assist:
Design Assist is a collaborative process where the contractor joins the design team early in the project to provide input, expertise, and cost-related insights.
In this approach, contractors’ perspectives are considered during the design phase, allowing them to offer valuable feedback on constructability, materials, and methods.
The goal is to enhance the design’s feasibility, cost-efficiency, and functionality, while still maintaining the architect’s creative vision.
Key Features of Design Assist:
1. Early Contractor Involvement: Contractors are brought on board during the design phase, fostering a multidisciplinary collaboration that integrates construction expertise from the outset.
2. Constructability: Contractors contribute insights on how design decisions may impact the construction process, highlighting potential challenges and proposing solutions.
3. Cost Control: By involving contractors in design discussions, cost implications of design choices can be addressed in real time, preventing costly changes during construction.
4. Optimized Project Delivery: Design Assist can lead to a smoother construction phase, as design-related conflicts and inefficiencies are mitigated early on.1
Specifically for curtain walls, design-assist provides an opportunity for the curtain wall subcontractor as well as the construction manager/general contractor (CM/GC) to work alongside the design team early in the design phase to develop the curtain wall delegated design documented in the architectural drawings and in the subcontractor’s shop drawings. This may begin as soon as schematic design or design development and can provide the design team greater assurance that the architectural vision and technical performance requirements can be successfully achieved within the project budget and schedule. Design-assist also allows the subcontractor and CM/GC the opportunity for early coordination of construction logistics, including selecting key material suppliers (e.g. glass, opaque panels), mockup testing, factory fabrication, transportation, and field installation. This early contractor engagement often provides more time for contractors to engage the market/supply chain, particularly during volatile markets, allowing owners to better secure orders and pricing for key materials.
The degree to which design-assist is appropriate/valuable varies from project to project. For example, if the architectural intent and design requirements of a curtain wall project are relatively simple and straightforward and ample time is provided in the project’s schedule, design-assist may not be as valuable/necessary. In this case, a basis-of-design, commodity, stick-built curtain wall system can be shown on the architectural drawings and included in the performance specifications and can be competitively bid by the CM/GC after final construction documents are produced. A traditional sequence of design-bid-build procurement arrangement of the curtain wall is likely appropriate in this example, so long as the initial basis-of-design selection does not require significant system design alterations to fit unique project requirements. The greater the amount of customization to the system and the more constrained the project schedule, the greater the value design-assist can offer in reducing risk. In some cases, for example with some state/government projects, design-assist and early award is not permitted as it conflicts with procurement regulations.
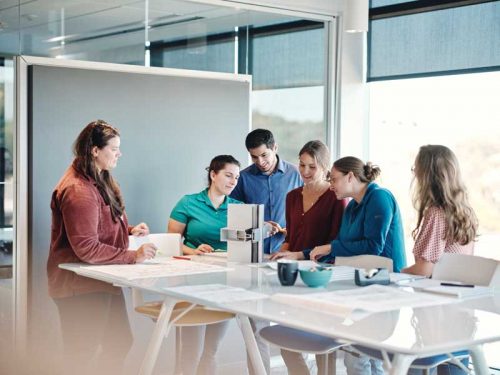
However, it is important to note that design-assist procurement, if executed properly, does not restrict the opportunity for competitive bidding and value for the owner but rather simply shifts the timeline for bidding/award of the curtain wall earlier in the design process (Figure 1). In this case, risk can be minimized by engaging in design-assist, though not at the expense of healthy competition. In most cases, the design-assist contract also includes the construction contract. However, some projects may elect to award only design-assist initially and then award construction after design-assist is complete. This gives the team the option to rebid the curtain wall if determined beneficial for the project.
Roles and responsibilities
The design-assist team includes a variety of parties, each with varying roles and responsibilities. Each party brings its own unique and diverse set of skills to the collective team. It is important that all team members understand each other’s roles and responsibilities; they must be aligned on intent and committed to the success of the process. Each project is unique, but in general, the following parties are key members of the design-assist team:
Ownership team
The ownership team is key during design-assist as the ultimate responsible party for making final decisions, particularly key budget/schedule decisions. It is, therefore, incumbent on the rest of the team to provide their individual expertise and recommendations aligned with the owner’s interests. Ownership teams often include the owner directly as well as representatives/project management firms on behalf of the owner who are experienced with project delivery. In design-assist, owners typically hold a separate contract with the design team and one with the construction team, as is common in design-bid-build.
Design team
Architect: typically leads the design team. Some projects include both a design architect and an architect-of-record (AOR). In this scenario, the design architect typically establishes the overall architectural vision and design-intent of the curtain wall (e.g. establishing aesthetics, geometry, materials, etc.), whereas the AOR (also commonly known as the executive architect) is responsible for developing the construction drawings and performance specifications, which typically delegate the final design and engineering responsibility of the curtain wall to the curtain wall subcontractor. Note that delegating the design of curtain walls to the subcontractor is typical in the industry, whether utilizing design-assist or traditional design-bid-build procurement.
Curtain wall consultant: The curtain wall consultant is a key member of the design team whose scope of consulting with the architect may vary from project to project. This consulting often includes working closely with the architect and design team in helping achieve the vision for the curtain wall, providing consulting services such as proof-of-concept analysis of the system(s), assisting with system detailing and performance specifications, and various other consulting services.
Structural engineer: The structural engineer of the building typically defines the loading criteria the curtain wall will need to resist (e.g. wind, ice/snow/rain, seismic) alongside other loads often defined by the curtain wall consultant (impact, barrier, accidental) and, if applicable, the security consultant (e.g. blast loading). The structural engineer will also provide the anticipated building movements (e.g. live load deflection, interstory-drift) which the curtain wall must be designed to accommodate.
Mechanical engineer: The mechanical engineer is typically responsible for confirming the project’s energy code compliance, most typically by developing an energy model. The curtain wall energy performances (e.g. U-factor, solar heat gain, daylighting) must be carefully defined and coordinated between the architect, curtain wall consultant, and mechanical engineer and included as part of the performance specifications.
Other consultants: Depending upon the project, other consultants that may be included as part of the design team include an environmental laboratory (for wind tunnel study), a security consultant (for blast, forced-entry, ballistics), a facade access consultant (for access strategy, imposed loads), an acoustic consultant (for acoustic design requirements), a lighting consultant, and/or a sustainability consultant.
Contractor team
Construction manager/general contractor (CM/GC): The project’s CM/GC typically leads the design-assist process for the contractor team. They will also typically lead the bidding process and bid review and work alongside the team during design-assist to coordinate meetings and construction logistics. The term “construction manager” is typically used prior to the construction contract award and “general contractor” is used post-award. The GC typically holds the contract with the curtain wall subcontractor.
Curtain wall subcontractor: The curtain wall subcontractor is the key contractor during design-assist. The subcontractor will typically be the single-source contractor providing all final design and engineering as part of the delegated design requirements, as well as all material sourcing, fabrication, and installation of the curtain wall. In some cases, the subcontractor may only provide system installation and subcontract the design/engineering and fabrication to a curtain wall system manufacturer. Either way, the subcontractor typically holds the contract with the key material supplier (e.g. glass) and any other subcontracts for the curtain wall system furnishment.
Material suppliers: Key material suppliers for the curtain wall system include glass manufacturers (e.g. providing float glass, low-e coatings), glass fabricators (e.g. providing heat treatment, heat soaking, lamination, insulating glass unit fabrication, ceramic frit, other specialty glass processing), and other materials (e.g. opaque panels, aluminum extrusions, finishes, insulation, sealants, gaskets, etc.).
Third parties
Testing agencies: Third-party laboratory testing agencies are often engaged during the mockup testing phase to perform the laboratory testing of the design of the curtain wall system. Third-party field testing agencies are also engaged during the construction phase to perform field testing to verify the performance of the installed system. Testing agencies are often contracted directly to the owner or the GC.
Building enclosure commissioning agent (BECxA): A BECxA, if engaged on the project, provides third-party peer review of the curtain wall design and construction during design-assist, particularly for custom curtain wall projects. Not all projects have a BECxA; however, if utilized, the BECxA is typically a third-party curtain wall consultant, often hired directly by the owner or, in some cases, by the GC/CM. The BECxA may also provide third-party testing of the curtain wall in their scope.
Navigating the process
As discussed earlier, design-assist shifts the timeline for bidding/awarding the curtain wall earlier in the design process compared to traditional design-bid-build, sometimes as early as schematic design or design development. Once the curtain wall is awarded to the successful bidder, design-assist runs in parallel with the rest of the design phases of the project.
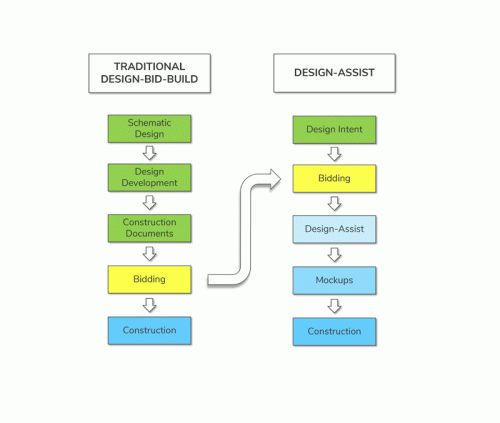
The timeline and stages of curtain wall design-assist can vary from project to project but generally can be categorized into the following key stages (Figure 2):
Design intent
During this phase, the architect, with input from the curtain wall consultant, establishes the design intent of the curtain wall. Varying levels of design intent/proof-of-concept design are provided in this stage (i.e. before bidding and contractor engagement) and can vary from project to project depending upon the project complexity and schedule, but often includes:
- Establishing design-intent of curtain wall, studying system/material options, geometry/panelization, method of attachment.
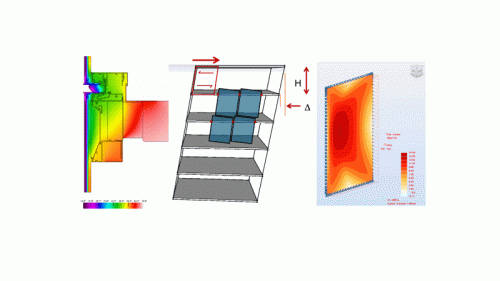
- Performing proof-of-concept analyses (e.g. structural, thermal) to inform the bid drawings and performance specifications. These preliminary analyses, often performed by the curtain wall consultant, are particularly important for custom projects, demonstrating the curtain wall systems/details shown on the drawings (unique as they may be) can meet the specified performance requirements (Figure 3):
- Defining system air/water management strategies.
- Reviewing code requirements for safety glazing and the use of fully tempered glass.
- Studying constructability as well as waterproofing tie-ins to adjacent systems.
- Considerations for in-service maintenance/facade access, including glass cleaning and replacement.
- Coordinating curtain wall design with other key consultants (e.g. structural engineer, mechanical engineer, security consultant, etc.).
- Developing sketches/details, basis-of-design systems/materials, developing a list of appropriate subcontractors for bidding.
- Defining specific requirements for fabrication samples, mockups, and testing.
- Developing bid documents (e.g. drawings, proof-of-concept reports, wind tunnel studies, performance specifications, bid submission requirements).
Bidding
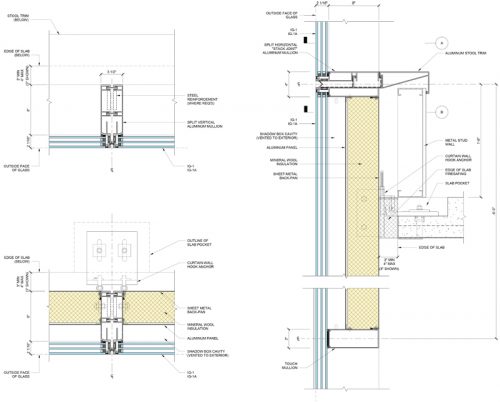
Once the design team produces the bid documents (Figure 4), the CM/GC will typically lead the process of distributing the documents to bidders. Depending upon the market and complexity of bid submission requirements, bidders will often be provided several weeks/months to prepare and submit their bids. Once bids are received, the team will review against the bid requirements (e.g. bidder’s approach to design-assist, proposal drawings, proposal calculations, test reports, cost estimate/alternates/cost management, proposed team, work schedule, capacity to meet project schedule, quality control plans, construction logistics requirements, bonding capacity, including any bid qualifications/exclusions). Bidders may also be shortlisted and/or interviewed by the team before final selection.
Design-assist
Once the curtain wall subcontractor has been selected, the design-assist process begins. Depending upon the complexity of the system(s) design and project schedule, design-assist often takes several weeks/months to complete. This stage’s key focus/end goal typically culminates in a final set of approved laboratory performance mockup (PMU) shop drawings and development of a final guaranteed maximum price (GMP) for the curtain wall. Key steps in this stage include:
- Kickoff meeting with the team members, discussing the design-assist process, system design, mockups, schedule, etc.
- Collaborative design-assist meetings, typically held weekly or biweekly, including continued development of the curtain wall design begun by the design team during design intent now with the selected curtain wall subcontractor’s system. This typically includes detailed curtain wall design by the subcontractor (e.g. engineering calculations, shop drawings, material sampling, system prototyping, etc.) and review by the design team. The subcontractor will also maintain a cost analysis log throughout this phase to track adjustments in the anticipated system cost based on decisions made throughout the process.
- Development and approval of material samples, fabrication samples, and mockup shop drawings.
- Development of a final comprehensive package documenting the work of the design-assist process.
Design-assist typically runs concurrently with the rest of the building design during design development and construction documents, and the architect will, therefore, often incorporate the subcontractor’s details into the final construction documents and can also tailor the final performance specifications in line/commensurate with decisions made during design-assist.
Mockups
Design-assist most typically includes a series of mockups to validate design and performance. The extent of mockups can vary from project to project; below is a list of a variety of mockups often utilized, specifically for custom curtain wall projects during design-assist. Note these mockups can be provided separately and/or combined depending on project schedule and budget:
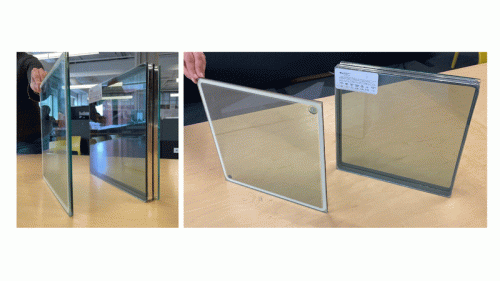
Material sample mockups: One of the first steps in mockups is providing hand-held material samples of the key elements of the curtain wall system (e.g. insulating glass units, opaque panels, aluminum finishes, etc.) to study the quality and finish of materials proposed (Figure 5).
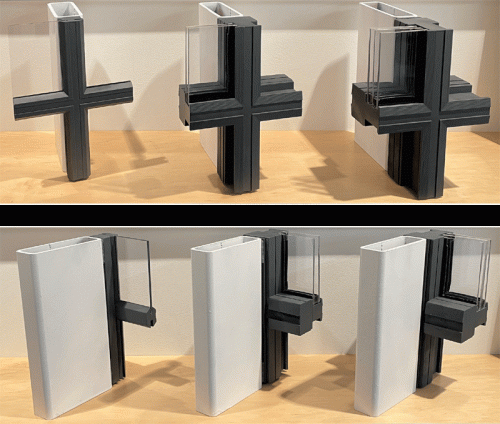
Fabrication mockups: Tabletop fabrication mockup samples of key features of the curtain wall can be provided (e.g. typical framing joint details, including four-way intersections) to study the details/geometry, particularly for complex geometric designs (Figure 6).
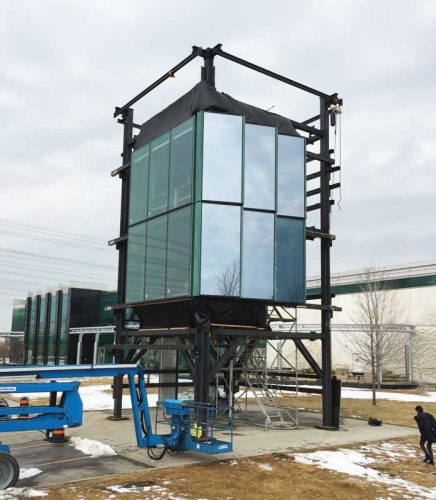
Visual mockup: Once materials have been reviewed/narrowed down, the team may desire the opportunity to review the glass type(s) and other opaque panels at full scale with a full-scale visual mockup (VMU). The visual effects of glass (e.g. reflectivity, flatness, bow/warp, anisotropy, and other distortions) are often difficult to capture in small hand-held samples; therefore, to appropriately manage expectations, a VMU is often critical for review and approval to establish an agreed-upon level of quality and acceptability of the glass and other materials (Figure 7).
The VMU typically does not include the final system framing/aluminum extrusions but focuses on full-scale material selection. The VMU may also include various interior lighting conditions, as well as interior window treatments (e.g. roller shades), which may affect glass selection. Often, the VMU is constructed at either the glass fabricator’s facility, the curtain wall subcontractor’s facility, or at/near the project site.
Laboratory performance mockup: Once the VMU has been accepted, an off-site laboratory performance mockup (PMU) of the curtain wall system is constructed and tested to validate the system design. In addition to validating design, the PMU also provides the design team the opportunity to confirm the selected systems, materials, finishes, etc., from the VMU and to provide a benchmark for quality and construction of the curtain wall system, including tie-ins to adjacent waterproofing systems.
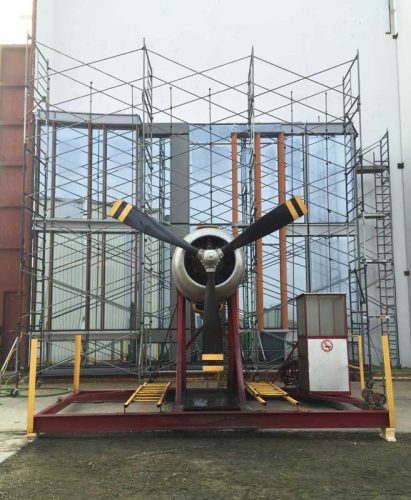
The PMU is typically constructed by the subcontractor at a third-party testing agency facility. PMU testing varies from project to project and is often customized based on the project, but it typically includes testing in general accordance with AAMA 501-24, including testing for airtightness, static and dynamic water tightness, structural deflection and overload, differential movement, impact, demonstration of glass replacement, etc. (Figure 8).
Adjustments/tweaks to the design and/or installation procedure resulting from the PMU testing are then incorporated into the final shop drawings and can also inform recommendations for field testing during installation on site.
The PMU provides valuable information that can inform the design and constructability of the curtain wall system before wholesale fabrication and installation as an important quality control (QC) measure for the project. In the author’s experience, there is always something valuable to learn from a PMU and a critical QA/QC procedure for custom curtain wall projects. Although custom systems are typically based on tried-and-true curtain wall design principles, including project-specific design and engineering, there is no match for environmental simulations to test the curtain wall’s design and construction to appropriately mitigate risk for the project. For example, if a design adjustment must be made to the curtain wall system as a result of PMU testing, it is typically much more beneficial to learn that during the PMU when there is still time to make adjustments rather than learning this during curtain wall installation and/or post-turnover when changes/remediation can be significantly more costly and/or compromises to design or performance must be made.
Construction
Following the successful completion of mockups, the team now focuses on wholesale fabrication and installation of the curtain wall system. Key steps during the construction phase typically include:
- Submittals: Now that the PMU has successfully passed, the subcontractor will incorporate results from the PMU and develop full building shop drawings for review and approval. To comprehensively capture the final design of the curtain wall, record submittals (e.g. signed and sealed engineering calculations and shop drawings, PMU test reports, installation procedures, warranties, etc.) should be submitted for the project record.
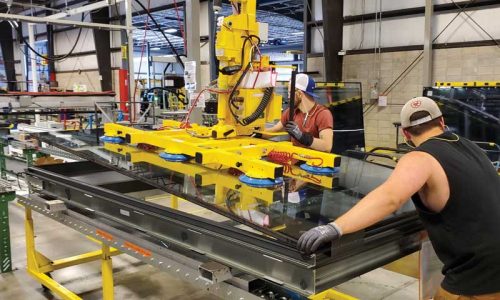
- Factory fabrication: Factory fabrication of the curtain wall systems typically begins with the fabrication of insulating glass units at the glass fabricator facility. For unitized systems, once glass is fabricated, it is typically shipped to the curtain wall manufacturer’s facility for factory glazing, or for stick-built systems, glass is shopped to the project site for field glazing. Members of the team, including the owner, architect, curtain wall consultant, and/or BECxA, will often perform site visits to the fabrication facilities to observe and review fabrication quality (Figure 9).
- Preconstruction meetings: Prior to installation on site, the team will typically hold preconstruction meetings to review items such as field safety, any outstanding submittals/RFIs, construction timeline, design team field reports, field testing, etc.
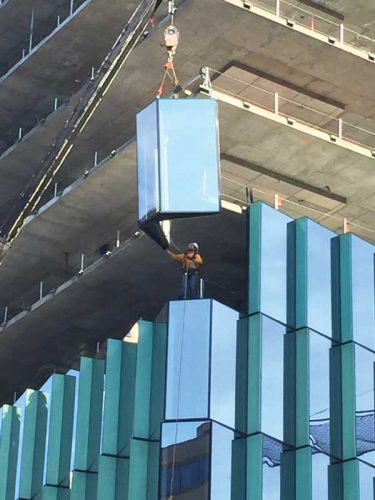
- Installation: Once the first curtain wall panels arrive on site, the curtain wall installer will typically install a sample installation on the building for the design team to review. The sample installation can be used as a standard for judging the acceptability of installation on-site. Throughout the installation, the architect, curtain wall consultant, and/or BECxA will often visit the site to observe installation and compliance with the contract documents. While on-site, the team can meet to help resolve detailing issues and unforeseen field conditions (Figure 10).
- Field testing: Throughout the installation process, an important QA/QC procedure includes field testing the installed curtain wall units to help ensure the system has been installed air and watertight, typically in general accordance with AAMA 503. Note: PMU testing is used to test design, whereas field testing is used to ensure the panels are installed properly. Typically, field testing is carried out through the installation process (e.g. 10 percent, 50 percent, and 75 percent of installation) to catch any potential issues and rectify them early and throughout installation.
- Record documentation: One of the last important steps in the process is for submission of final documentation of the curtain wall design and installation, including signed and sealed as-built record shop drawings (including documentation of any field modifications), record submittals, calculations, field reports, final warranties, and maintenance manual(s).
Case studies
In this section, brief case studies are provided, showcasing a variety of different project types from the author’s experience that utilized curtain wall design-assist procurement to varying degrees.
National Air and Space Museum
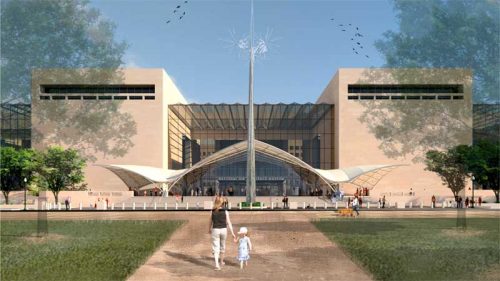
The National Air and Space Museum was one of the largest museums on the National Mall when it opened in 1976. Originally designed by Hellmuth, Obata + Kassabaum, the Smithsonian Institution is undertaking a comprehensive modernization project to replace the building envelope systems, including the existing stone facade, glass curtain wall, and skylights. The project utilized a design-assist procurement method for the new aluminum-framed stone-clad curtain wall, steel-framed glass curtain wall, steel-framed skylights, and new structural glass entry vestibule.
Project challenges
- Facade replacement of a historically significant landmark, including architectural sensitivity of matching existing Tennessee Pink marble stone.
- Challenge of balancing solar heat gain, natural daylight, color rendering, and ultraviolet filtering into glass-clad atrium gallery spaces housing precious museum artifacts.
- Interior wintertime humidification, requiring computational fluid dynamics (CFD) modeling of the glass facade and skylights of the atriums to predict risks of wintertime condensation within the facade accurately.
- Challenge of recladding an existing steel-framed superstructure while limiting the offset of the new stone plane due to increased assembly thickness.
- Special security requirements as part of the new facade design.
- Unique free-form design of new entry vestibule with architecturally exposed structural steel (AESS), tensile-fabric roof membrane, and structural glass curtain wall.
Team
- Owner: The Smithsonian Institution
- Renovation architect: Quinn Evans
- Enclosure consultant: Simpson Gumpertz & Heger Inc.
- Structural engineer: Robert Silman Associates, a TYLin Company
- Mechanical engineer: Mueller Associates
- Security consultant: Hinman / Woods Peacock
- General contractor: Clark/Smoot/Consigli, (joint venture [JV])
- Glass curtain wall, skylight, and vestibule subcontractor: Roschmann Group
- Stone curtain wall subcontractor: Rugo Stone
- Stone curtain wall manufacturer: Eclad Limited
- Building enclosure commissioning agent (BECxA): ECS Mid-Atlantic LLC
- Contractor’s consultant: Wiss Janney Elstner
- Laboratory testing: Intertek
Year
- Under construction (2024 anticipated enclosure completion)
Midtown Center
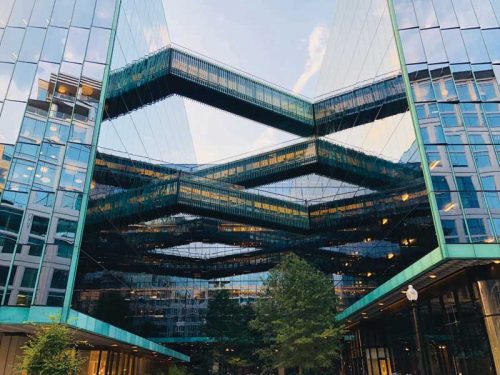
Midtown Center is a new office building in downtown Washington, D.C., with a unique corrugated pre-patinated copper and glass unitized curtain wall featuring three crisscrossing sky bridges with copper fin sunshades spanning over the plaza below. The building is elevated above the street level, including glass-clad retail pods along a network of alleys in the plaza with landscaping and water features, integrating the building with the streetscape. The project utilized a design-assist procurement method for the unitized glass and copper-clad curtain wall system.
Project challenges
- Unique geometry of 3D corrugated curtain wall. The team studied options using a flat curtain wall with a corrugated slab edge versus a 3D curtain wall with a flat slab edge, deciding on the latter.
- Curtain wall panelization and geometry studies, balancing aesthetics with fabrication and cost.
- Utilizing computational fluid dynamics (CFD) modeling to evaluate spandrel options and assess risks of interior condensation due to the complex curtain wall geometry and proximity to interior diffusers.
- Challenges of edge-of-slab firesafing and inter-story fire separating due to unique curtain wall geometry.
- Material sampling and challenges of integrating pre-patinaed copper panels as part of the curtain wall assembly.
- Careful detailing and trade coordination at the intersection of the sky bridges with the glass curtain wall, roofing, and expansion joints, including accommodation for differential movement in-service while providing thermal continuity and remaining airtight and watertight.
Team
- Owner: Carr Properties
- Design architect: SHoP
- Executive architect: WDG Architecture
- Curtain wall consultant (for owner): Simpson Gumpertz
& Heger Inc. - Curtain wall consultant (for architect): Curtain Wall Design Consulting
- Structural engineer: SK&A
- Mechanical engineer: Girard Engineering
- General contractor: Clark Construction
- Curtain wall subcontractor: Oldcastle Building Envelope
- Laboratory testing: Construction Research Laboratory
- Wind tunnel laboratory: RWDI
Year
- Construction completed 2018
UPMC Mercy Pavilion
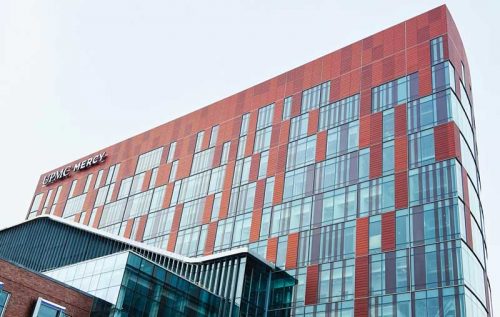
The new UPMC Mercy Pavilion at the University of Pittsburgh Medical Center (UPMC) campus in Pittsburgh, Pa., was designed for clinicians, researchers, and educators as a destination for healing, an incubator for medical advancements, and a hub for biomedical research. The facade design features a unique pattern of terracotta, ceramic-fritted glass, and vision glass integrated into the unitized curtain wall system, including a glass-clad interconnecting stairway with exterior vertical glass fins and a point-supported structural glass curtain wall at the ground-level main entry.
Project challenges
- Balancing facade opacity and transparency considering the overall energy performance of the facade, solar control, and interior thermal comfort. Using terracotta, ceramic-fritted glass, and vision glass to provide this balance and overall aesthetic, featuring visual contrast of facade materials for low-vision patrons.
- The design team developed a custom, parametric, digital tool for automated calculation of curtain wall U-factor, solar heat gain, and visible light transmission for various glazing types, low-e coatings, ceramic frit, and terracotta configurations to achieve the desired aesthetic while meeting energy requirements, developing a “family” of facade panel types.
- Evaluating the curtain wall at the humidified vivarium and its condensation potential.
Team
- Owner: UPMC Mercy
- Architect: HOK
- Curtain wall consultant: Simpson Gumpertz & Heger Inc.
- Structural engineer: HOK
- Mechanical engineer: CJL Engineering/AEI Affiliated Engineers
- General contractor: Mascaro/Barton Malow joint venture [JV]
- Curtain wall subcontractor: United Architectural Metals/DM Products/Larson Engineering
- Building enclosure commissioning agent (BECxA): Intertek
Year
- Construction completed 2022
Australian Embassy
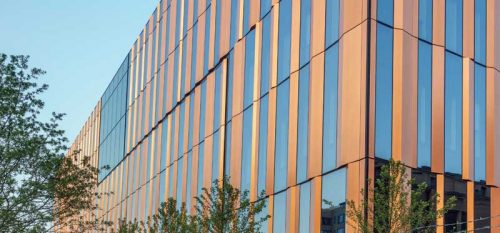
The new chancery building for the Australian Embassy in downtown Washington, D.C., is located on Scott Circle and replaces the former chancery building that officially opened in 1969. The facade design features a custom glass and copper-clad unitized curtain wall, inspired by and evoking the hues of the landscape of the Australian Outback, captured by the unique composition and geometry of the copper panels reflecting the sunlight. The project utilized a design-assist procurement method for the security-rated unitized curtain wall system with integrated copper panel rainscreen.
Project challenges
- The team studied panelization and geometry options for varying curtain wall geometry, balancing aesthetics and performance, with constructability, fabrication, and cost.
- Material sampling and challenges of integrating coated copper panels as part of the curtain wall assembly.
- Special security requirements for curtain wall design
Team
- Owner: Australian Department of Foreign Affairs and Trade (DFAT)
- Project manager: Jacobs
- Design architect: Bates Smart
- Executive architect: KCCT
- Curtain wall consultant/structural engineer: Simpson Gumpertz & Heger Inc.
- Security consultant: Aurecon
- Mechanical engineer: Interface Engineering
- General contractor: Clark Construction
- Curtain wall subcontractor: Enclos
- Laboratory testing: Intertek
Year
Construction completed 2023
The Wilson
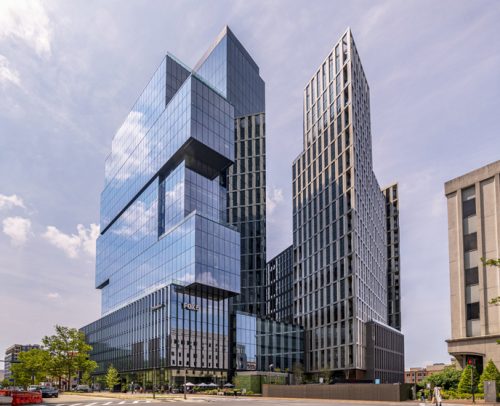
The Wilson is a new all-glass office tower as part of a new mixed-use complex in Bethesda, Md. The development also includes two residential towers (known as The Elm), and all three towers sit atop a multi-level podium with a landscaped public plaza, retail space, three levels of below-grade parking, and a connection to the Maryland Department of Transportation (MDOT) Purple Line underground subway station that passes through the below-grade structure. The Wilson utilized a design-assist procurement method for the unitized glass curtain wall, which features a unique “offset” massing of the glass facade, providing multiple exterior terraces for occupants.
Project challenges
- Challenges of integrating offset metal copings, metal soffits, and exterior terraces with glass curtain wall at offset building massing, including waterproofing tie-in and thermal continuity between system.
- Studying a variety of options for various glass low-e coatings and ceramic frit patterns for controlling solar heat gain, daylighting, and views out.
- Integration of sprinkler system within curtain wall for fire protection in close proximity to adjacent buildings.
- Integrated exterior vertical metal fins at podium-level curtain wall, transitioning between an unconditioned elevated parking garage and conditioned office space above.
Team
- Owner: Carr Properties
- Architect: Shalom Baranes Associates
- Curtain Wall Consultant: Simpson Gumpertz & Heger Inc.
- Structural Engineer: Tadjer Cohen Edelson
- Mechanical Engineer: Girard Engineering
- General Contractor: Clark Construction
- Curtain Wall Subcontractor: Harmon, Inc.
- Laboratory Testing: Intertek
- Wind Tunnel Laboratory: RWDI
Year
Construction completed 2021
Gund Hall Glazing System Replacement
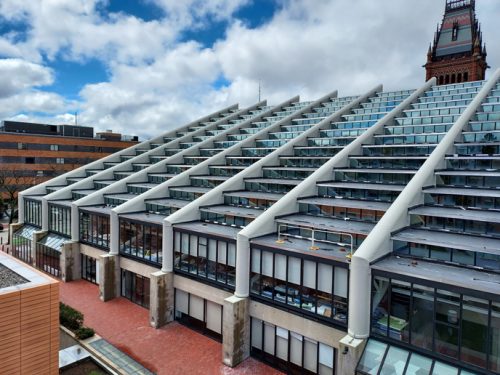
Gund Hall is the home of Harvard University’s Graduate School of Design (GSD) in Cambridge, Mass. Originally designed by John Andrews in 1972, this unique structure features a series of stepped roofs and clerestory windows between long-span trusses over the studio space below. As part of its recent 50th-anniversary celebration, the university is undergoing a replacement project for the exterior glazing systems of the studio. The project used a design-assist procurement method for the new glazing systems, including the multi-story north and south veneer curtain wall, east curtain wall and sloped glazing, and clerestory windows.
Project challenges
- Glazing system replacement of a historic building, including architectural sensitivity of matching the existing profile of the lock-strip gasket and monolithic glass curtain wall.
- Studying various options for system replacement to meet the aesthetic requirements of the existing system while providing a modern, drained, thermally broken curtain wall system.
- Meeting aggressive energy code requirements for U-factor of glazing systems while maintaining existing historic glass module size, resulting in the use of vacuum insulating glass (VIG) and triple glazing.
- Challenge of reglazing an existing structure, including maintaining existing steel framing at north and south curtain wall.
- Waterproofing challenges of unique stepped roof geometry and clerestory windows, including tie-ins to existing roofing.
Team
- Owner: Harvard University
- Owner’s Representative: Redgate
- Renovation Architect: Bruner/Cott Architects
- Enclosure Consultant/Structural Engineer: Simpson Gumpertz & Heger Inc.
- Mechanical Engineer: RG Vanderweil
- General Contractor: Shawmut
- Glazing System Subcontractor: Oldcastle Building Envelope/A&A Window Products
- Owner’s Consultant/BECxA: Heintges
- Testing Agency: RJ Kenney
Year
Under construction (anticipated completion 2024)
Conclusion
Curtain wall systems are ever present in today’s commercial marketplace. Advancements in design, materials, performance, and technology will continue to push the industry and provide exciting opportunities for the future. Design-assist is a valuable procurement method for curtain wall systems to help meet the unique challenges of both new design and reglazing historic projects. Whether unique geometry, novel materials, high energy targets, special project security requirements, and/or project schedules and budgets, the curtain wall design-assist process requires close collaboration among project teams, each bringing their collective and unique set of diverse skills and experiences for project success.
Notes
1 Refer to learn.aiacontracts.com/articles/comparing-design-assist-and-delegated-design-in-construction-projects.
Author
John A. Jackson is an associate principal with Simpson Gumpertz and Heger Inc. in Washington, D.C. His work focuses on the design and engineering of innovation building enclosure systems, with particular expertise in curtain walls, custom glazing systems, structural glass, and glass investigations. He is an active member of ASTM Subcommittee E06.52—Glass Use in Buildings, collaborative research project on spandrel thermal performance with the Pankow Foundation, and frequently delivers lectures on building enclosure design. Jackson can be reached at jajackson@sgh.com.
Take our quiz on this article!