Two-hour floor
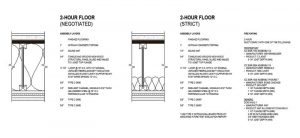
Like the one-hour floor, the main difference between the “strict” and “negotiated” assemblies is the cavity insulation. In this case, pictured in Figure 3, the insulation depth in the “negotiated” assembly is increased from 76.2 to 305 mm (3.5 to 12 in.), a non-trivial change which should be discussed with the code official. Unlike with the one-hour floor, the increased insulation is doing more work acoustically. Note that WIJ-2.1 lists an IIC of 45 when using vinyl flooring. This is below the code minimum of 50 IIC, so for the “strict” assembly to meet code, the finish floor must be carpet and pad, or a more robust topping slab and sound mat should be specified. The other more minor difference between the “strict” and “negotiated” assemblies is in the gypsum board ceiling. The “negotiated” assembly calls for generic Type C gypsum board; the “strict” assembly calls for a Type C gypsum board product compatible with the relevant fire test. In practice, this means proprietary gypsum board products will be required if one of the ICC-ES tested I-joists is selected.
Two-hour roof
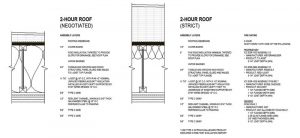
As with the one-hour roof, a code official’s flexibility regarding cavity insulation thickness will drive the overall approach for the two-hour roof shown in Figure 4 (page 26). If full cavity insulation is permitted, then R-49 can be achieved within the I-joist cavity. If the “strict” assembly is used instead, then the minimum 76.2 mm (3.5 in.) insulation should be installed tight to the deck above. Prescriptive compliance with the energy code can be achieved with continuous rigid insulation above the sheathing. Like the two-hour floor, the Type C gypsum board in the “strict” assembly is contingent on the I-joist installed.
Parting thoughts
The custom assemblies above demonstrate it is indeed possible to find middle ground between the DCA3 WIJ assemblies and independent, proprietary assemblies. The “strict” assemblies following the dictates of both sets of requirements (generic and proprietary) are not perfect, but they are not fatally flawed either. The negotiated assemblies are likely preferred, but code official acceptance is not guaranteed.
So, there are functional solutions, but why this effort is needed at all is a topic worth investigating. Have manufacturers gone rogue? Have the American Wood Council and DCA3 been too slow to adapt? In 2021, there is no reason why the design and specification of I-joist assemblies must be so laborious. In fact, it ought to be dead simple. This simplicity once existed in the form of the DCA3 WIJ assemblies, but it has been lost. Fortunately, there are ways for the industry to correct course.
First, proprietary assemblies should provide a baseline level of compatibility with long-accepted generic industry standards. At a bare minimum, this means allowing full cavity insulation, but ideally it would also entail allowing generic gypsum products to be used as well.
Second (and even better), manufacturers and industry groups should come together and continue to invest in the generic DCA3 WIJ assemblies. This means adding compatibility for I-joists with different dimensional characteristics (either by extrapolating existing test report data or by jointly financing new test reports) to DCA3 and committing to keeping the document abreast of future advances.
I-joists and engineered lumber have seen broad adoption over the last decade, in no small part because of documents like DCA3. The common cause and shared purpose bringing manufacturers and industry groups together under one umbrella—the ethos of collaboration that pushed the entire industry forward—should once again be revived.